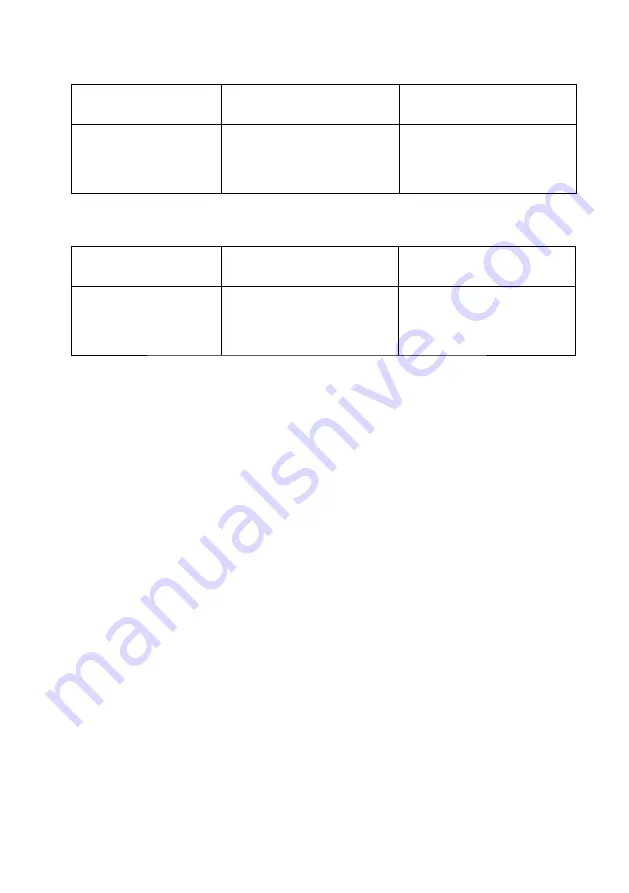
47
Tube cutting problems
The cut obtained is not
clean.
The cutter wheel is worn.
Replace the cutter wheel by a
new one. (See page 36).
The tube cutter is
damaged.
The tube cutter is worn or has
been used for tubes which are
too hard.
Replace the tube cutter by a
new one. (See page 37). Use
the tube cutter on carbon steel
or stainless steel tubes.
Reaming problems
Reaming is not
satisfactory.
The reaming cone is worn.
Replace the cone by a new
one. (See page 38).
The reamer is damaged.
The reamer is worn or has been
used for tubes which are too
hard.
Replace the reamer by a new
one. (See page 38). Use the
reamer on carbon steel or
stainless steel tubes.
EN
Summary of Contents for 162120
Page 1: ...Threading machine for tubes up to 2 Instruction Manual 162120 EN ...
Page 3: ...EN ...
Page 51: ...49 Exploded view of the motor and the oil pump Pump EN ...
Page 52: ...50 Exploded view of the transmission EN ...
Page 53: ...51 Exploded view of the saddle EN ...
Page 54: ...52 Exploded view of the automatic opening 2 die head EN ...
Page 55: ...53 Exploded view of the 1 4 3 8 die head EN ...
Page 56: ...54 Exploded view of the tube cutter EN ...
Page 58: ...56 Components of a nipple holder EN ...
Page 59: ...EN ...