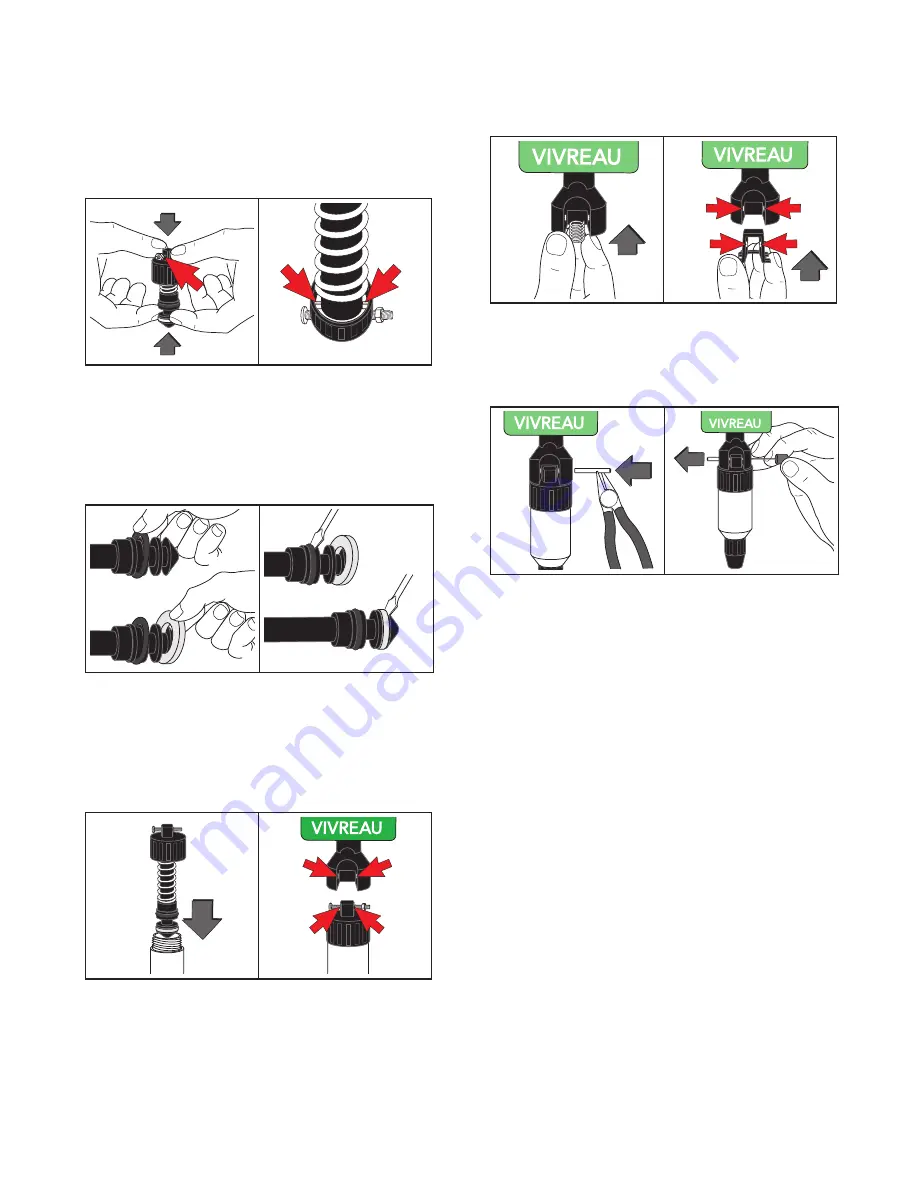
22
Reassemble the Dispenser
Press Dispenser Collar down firmly, reinsert screw
and release the spring pressure gently.
Alignment of the dimple and hole illustrated by the
position of the Screw.
Dimple and Hole alignment
Gently feed into position and then work the
remainder around the piston into groove.
Use a flat edged tool to ensure the Seal is located
correctly.
Position Seal with Flat Edged Tool
Reassemble Piston to Dispenser Body.
Screw the Cap onto the body. Ensure the Screw is
positioned properly to allow internal components
to align.
Reassemble Piston and Cap
Insert spring in Dispense Handle.
Push in Plastic Insert and position with Screw.
Insert Spring and Position Plastic Insert
Position Dispense Handle and align holes.
Drive Roll Pin back into position.
Dispense Handle Roll, Pin In Position
Summary of Contents for V3-202
Page 1: ...1 V3 201 and 202 Dispensing Systems Service Manual ...
Page 41: ...41 ...