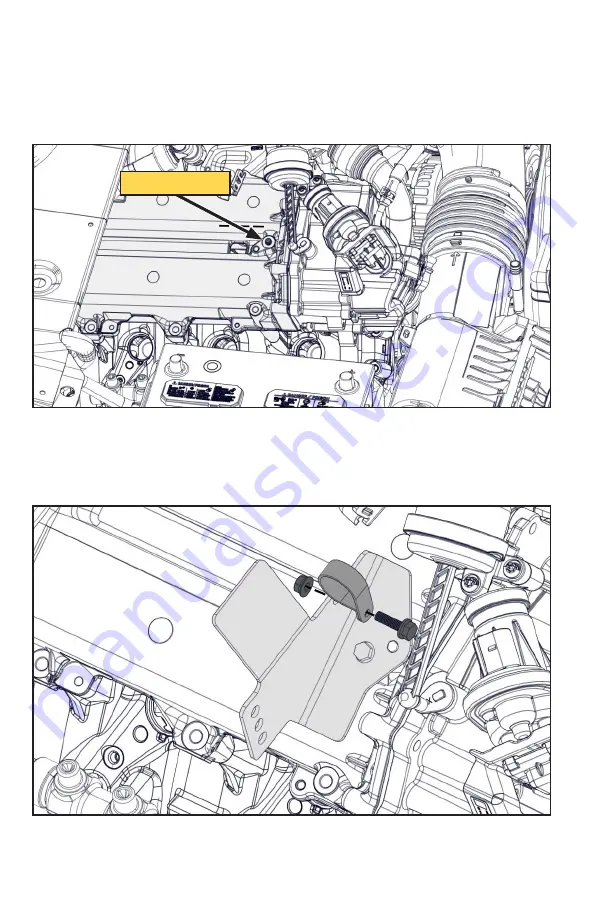
VMAC - Vehicle Mounted Air Compressors
VMAC Technical Support: 888-241-2289
VMAC Knowledge Base: kb.vmacair.com
18
☐
Mount the regulator assembly and secure it using the (×2) supplied M6 lock
nuts (Figure 17).
☐
Remove the plastic retainer clip from the wiring harness running over the EGR
cooler, unthread the clip from the hole and discard it.
☐
Position the oil fill bracket over the hole and align the smaller hole with the
nearby OEM bolt head (Figure 18).
Figure 18 — Install oil fill bracket
OEM fastener
☐
Secure the bracket using the supplied M8 fastener, ensuring there are no wires
or harnesses pinched under the bracket (Figure 18).
☐
Using the supplied P-clip and fasteners, secure the harnesses where they pass
over the oil fill bracket (Figure 19).
Figure 19 — Install oil fill bracket