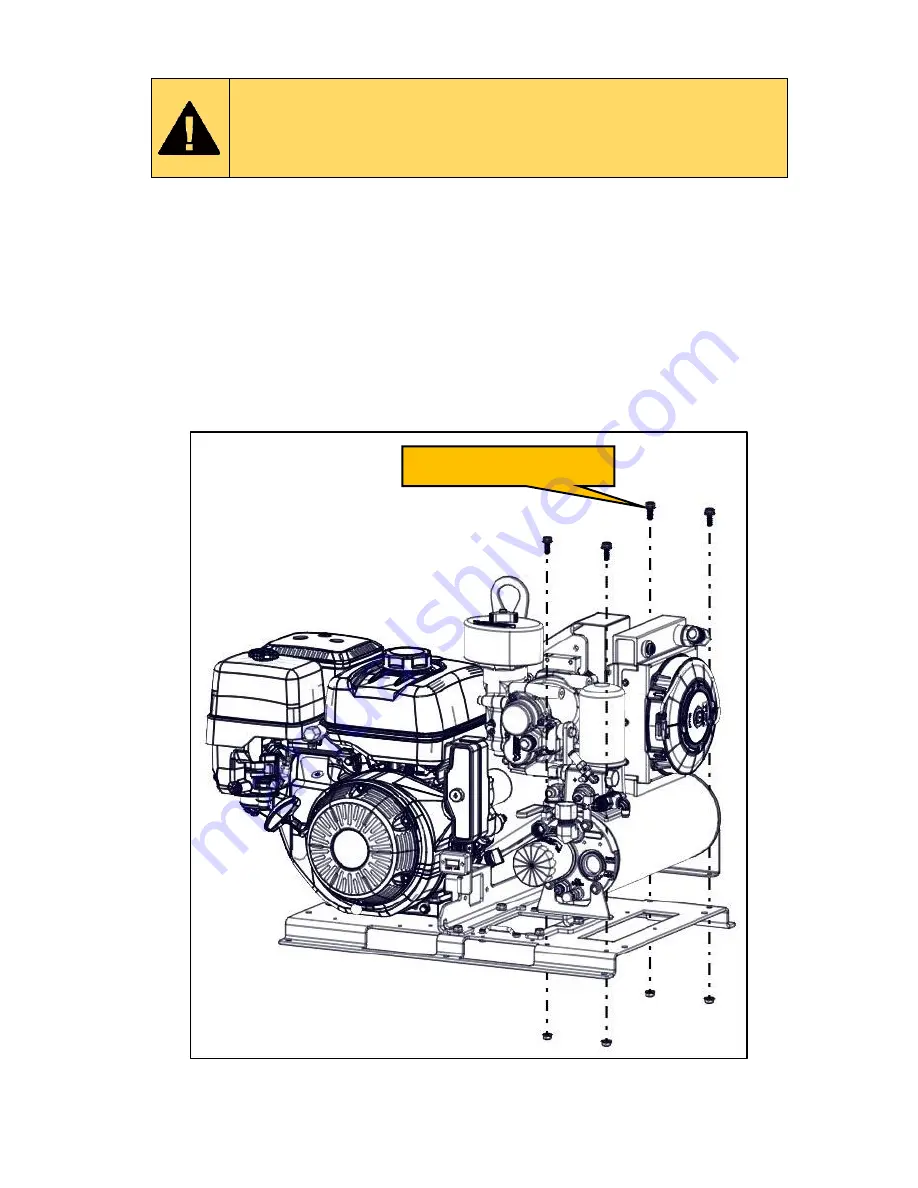
VMAC
– Vehicle Mounted Air Compressors
VMAC Technical Support:
1-888-241-2289
VMAC Knowledge Base: www.kb.vmacair.com
81
WHASP Tank Replacement
Read the
“Maintenance and Repair Safety” section prior to
performing any work on the system (beginning on Page 38).
Wear appropriate Personal Protective Equipment and follow
all industry standard safety practices.
Remove the WHASP Tank shroud.
Remove the battery.
Drain the compressor oil from the WHASP Tank (Page 48).
Disconnect the 3/4 in and 1/2 in hoses from the WHASP Tank.
Disconnect the PTFE tubes from the WHASP Tank.
Disconnect the electrical connectors from the fan and compressor
temperature switches.
Remove the 4 fasteners from the bottom of the WHASP Tank mounting
brackets.
Remove the WHASP Tank.
Figure 70
– Remove WHASP Tank
Install the WHASP Tank in the reverse order.
Remove fasteners (4x)
Summary of Contents for G300003
Page 1: ...Gas Engine Driven 30 CFM Air Compressor Installation Owner s and Service Manual G300003...
Page 2: ......
Page 97: ...This page intentionally left blank...
Page 98: ...This page intentionally left blank...
Page 99: ......
Page 100: ......