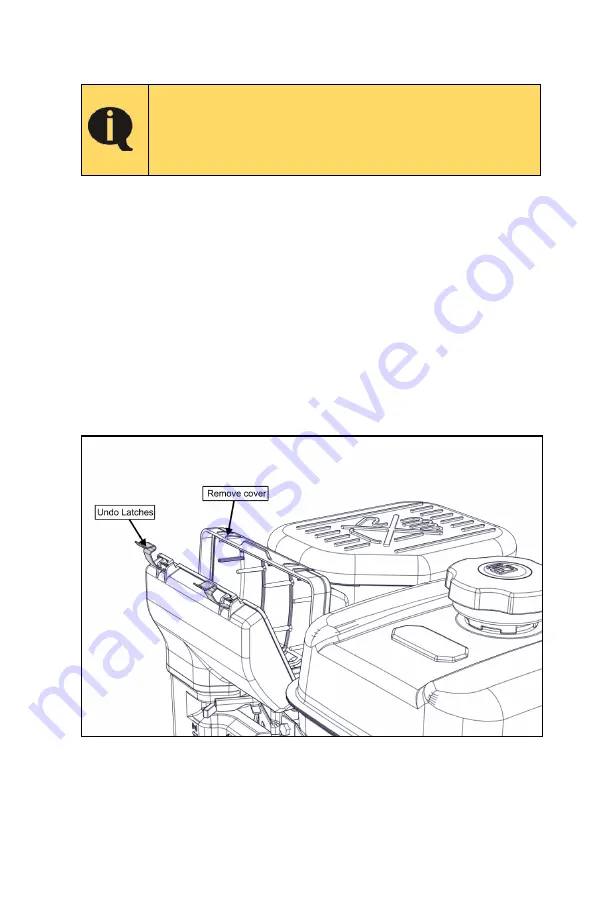
VMAC
– Vehicle Mounted Air Compressors
Toll Free:
1-888-241-2289
Fax: 1-250-740-3201
55
Changing the Engine Air Filter
Read the
“Subaru Engine Manual" before working
on the system.
Never run the compressor, drive the vehicle or
even allow the vehicle to sit parked without the
recommended air filter and filter cover installed.
1) Clean loose debris from the area around the filter cover to prevent
contamination entering the engine.
2) Undo the two latches on the air filter box, remove the filter cover and
the filter element.
3) Immediately cover the engine filter opening by masking with tape or
with a clean cloth to prevent contamination. Do not use compressed
air or perform any other tasks around the engine until the filter and
cover are replaced.
4) Clean the inside of the filter cover with a clean, dry cloth. Do not use
flammable solvents to clean the inside of the cover.
5) Remove the cloth or masking and install a new air filter.
6) Replace the cover and secure it with the two latches.
Figure 42 - Engine air filter
Summary of Contents for RAPTAIR-G30
Page 1: ...RAPTAIR G30 Gas Drive Air Compressor Installation Owner s and Service Manual G300002...
Page 2: ......
Page 89: ...This page intentionally left blank...
Page 91: ...This page intentionally left blank...
Page 92: ...This page intentionally left blank...
Page 93: ...This page intentionally left blank...
Page 94: ...This page intentionally left blank...
Page 95: ......
Page 96: ......