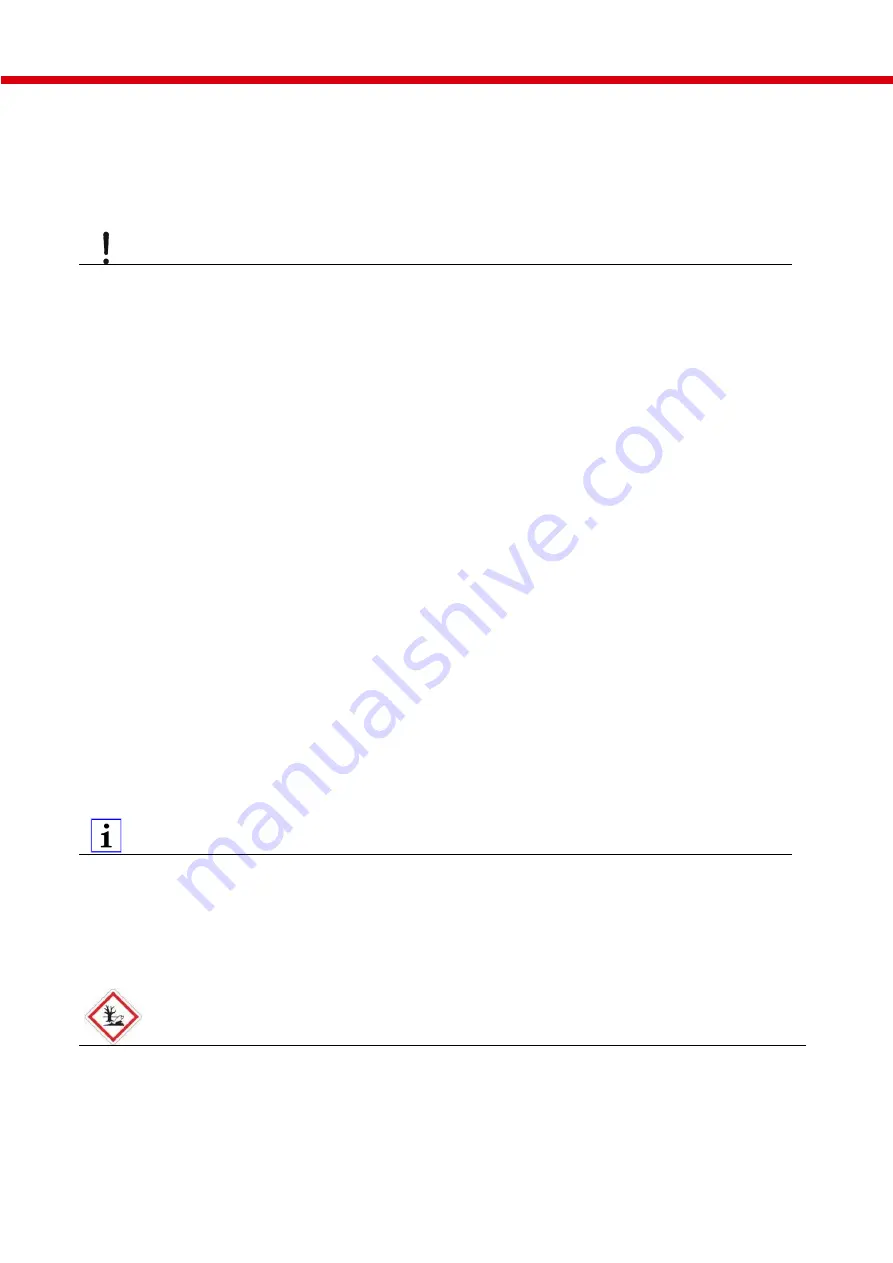
Maintena nce
WBV.PU.002.EN VX215QD V2.0
47
8.1.5
Buffer or quenching fluid - type
For optimum functioning of the mechanical seal, we recommend the oil grades listed in
Chapter
"Oils".
Please check your order confirmation to see whether the buffer chamber of your machine is filled with an oil
that deviates from this chapter.
Only use the oil specified on your order confirmation.
ATTENTION
To prevent premature wear of the seal, mineral oils or greases must not be used with EPDM O-rings. Use
glycol as an alternative.
To prevent contamination of the pump medium,
no fluid
must be filled into the buffer chamber of pumps with
the "dry buffer chamber" sealing system.
8.1.6
Buffer or quenching fluid - quantity
3.5 litres
per buffer chamber (guideline, depending on the buffer chamber assembly
Chapter
"Buffer
chamber")
8.1.7
Buffer or quenching fluid - inspection and change
Buffer fluid or quenching fluid
•
Check:
After the first 20 operating hours
Every 200 operating hours
Electronic buffer chamber monitoring is possible. Ask us
.
•
replace:
Every 2000 operating hours
When there is severe contamination
When there is intense leakage, replace the cartridge mechanical seal
Chapter
“Changing cartridge
mechanical seal"
Chapter
“Maintenance plan"
Buffer or quenching fluid properties
•
The hydrodynamic lubrication film of a mechanical seal can cause:
Slight contamination of the buffer or quenching fluid
Slight increase or decrease in the buffer or quenching fluid level
•
A slight increase in the buffer or quenching fluid level is also possible due to thermal expansion during
pump operation.
Environmentally friendly disposal
Treat buffer fluid or quenching fluid, for example, oils and hydraulic fluids, like hazardous waste and dispose
of them properly.