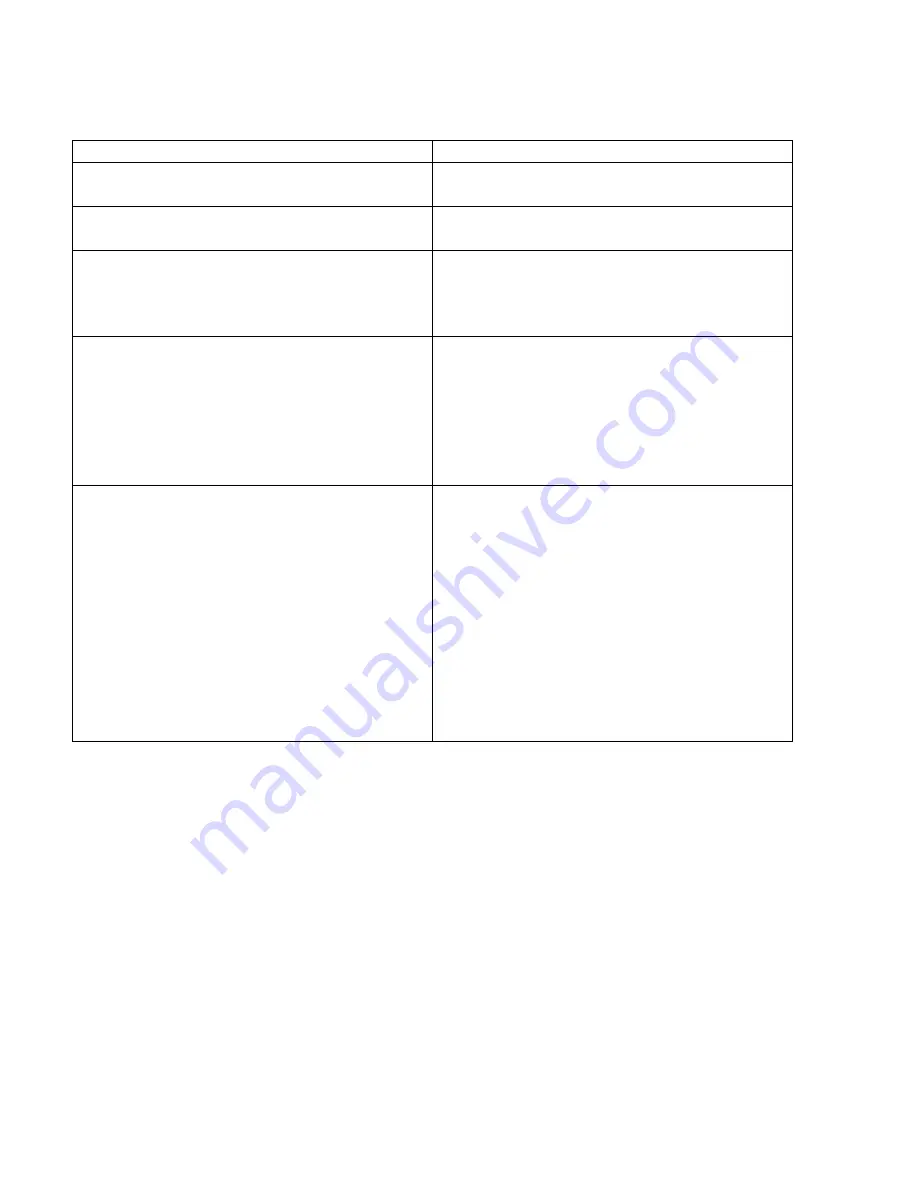
P24A & P34A Service Manual
TROUBLESHOOTING
12/2016
8-4
Symptom:
Freeze-up due to extended freeze period
Possible Cause
Possible Remedy
Freeze timer (1TR) set to long
Adjust timer or replace if defective. See Figure
9-2.
Freezer pressure switch (2PS) set too low or
defective (optional)
Adjust switch or replace if defective. See
Figure 9-3.
Water tank drain valve, make-up water float
valve or flushing valve stuck or opened (if 2PS
is used)
Close, repair, or replace valve as needed. The
float valve should be adjusted low enough that
water should not run out the tank overflow
during the freeze cycle.
Thaw gas solenoid valve (18) leaking through
during freeze (if 2PS is used)
Check the manual opening stem to make sure it
is in the automatic position (stem screwed in).
Check for leakage by sound, temperature
difference and frost during the freeze cycle.
Leakage should stop by closing the hand stop
valve downstream of thaw gas valve. Isolate
and repair or replace the valve as needed.
Compressor running unloaded
If the compressor is running unloaded, the
motor amp draw will only be 60%-70% of the
normal amp draw of a loaded compressor.
Check the load delay timer electrical circuit to
make sure the “UR-SOL” coil is not energized.
Refer to the compressor manual for normal oil
pressure needed to load the compressor
cylinders and any further procedures to check
the mechanical function of the unloader
mechanism.
Summary of Contents for P-24AL
Page 1: ...12 2016 P 24AL P 34AL TUBE ICE MACHINE Service Manual 5000 ...
Page 10: ...P24AL P34AL Service Manual TABLE OF CONTENTS 12 2016 vi ...
Page 15: ...P24AL P34AL Service Manual INTRODUCTION 12 2016 1 5 Figure 1 2 P24AL Right Side ...
Page 16: ...P24AL P34AL Service Manual INTRODUCTION 12 2016 1 6 Figure 1 3 P24AL Back Side ...
Page 17: ...P24AL P34AL Service Manual INTRODUCTION 12 2016 1 7 Figure 1 4 P24AL Left Side ...
Page 18: ...P24AL P34AL Service Manual INTRODUCTION 12 2016 1 8 Figure 1 5 P34AL Front Side Control Panel ...
Page 19: ...P24AL P34AL Service Manual INTRODUCTION 12 2016 1 9 Figure 1 6 P34AL Right Side ...
Page 20: ...P24AL P34AL Service Manual INTRODUCTION 12 2016 1 10 Figure 1 7 P34AL Back Side ...
Page 21: ...P24AL P34AL Service Manual INTRODUCTION 12 2016 1 11 Figure 1 8 P34AL Left Side ...
Page 22: ...P24AL P34AL Service Manual INTRODUCTION 12 2016 1 12 ...
Page 62: ...P24AL P34AL Service Manual START UP OPERATION 12 2016 5 8 ...
Page 84: ...P24A P34A Service Manual TROUBLESHOOTING 12 2016 8 12 ...
Page 110: ...P24AL P34AL Service Manual SERVICING OPERATIONS 12 2016 9 26 ...
Page 126: ...P24AL P34AL Service Manual TABLES CHARTS 12 16 16 11 8 ...
Page 130: ...P24AL P34AL Service Manual INDEX 12 2016 12 4 ...
Page 131: ...Appendix A ...
Page 134: ......
Page 136: ...i ...
Page 137: ...ii ...
Page 138: ...1 ...
Page 139: ...2 ...
Page 140: ...3 ...
Page 141: ...4 ...
Page 142: ...5 ...
Page 143: ...6 ...
Page 144: ...7 ...
Page 145: ...8 ...
Page 146: ...9 ...
Page 147: ...10 ...
Page 148: ...11 ...