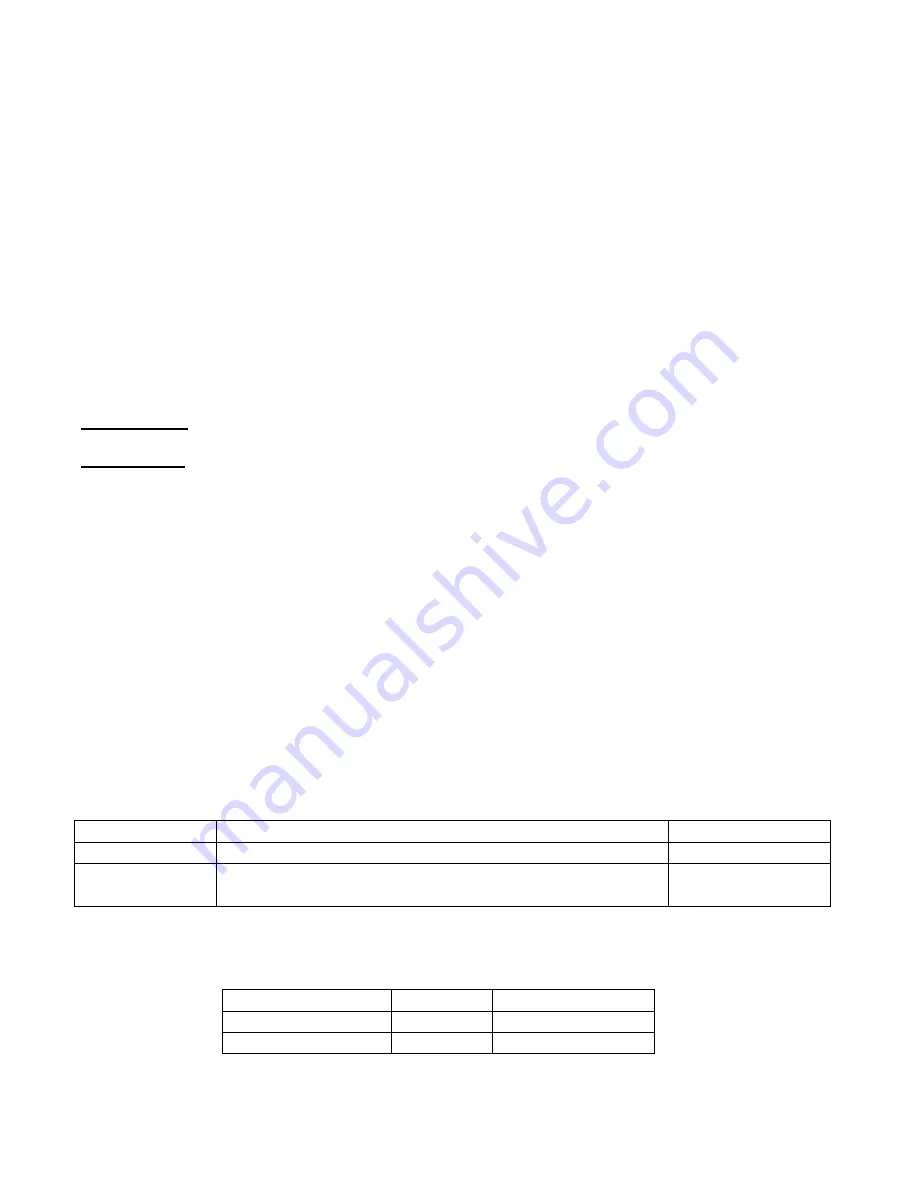
10TA Service Manual
MAINTENANCE
4/15/14
7-6
Flush condenser tubes clear with air, water, or a piece of rag on a stick or wire. In many cases this is all
that is required. If the inside surfaces are smooth, even though discolored, further cleaning is not
necessary. It is useless to try and get a bright copper surface on the inside of the tubes. They will
discolor almost immediately in service and the condenser has been designed with an adequate reserve
for moderate fouling on these surfaces.
If, however, a rough coating remains inside the tubes after flushing and wiping, further cleaning is
desirable. The color of this coating varies with water conditions, but roughness indicates cleaning
tools should be used.
Any type tool to be considered should be tried first on a piece of copper tubing held in a vise or flare
block. Nylon, brass, or copper brushes are recommended. If any flakes of copper appear or if score
marks are made inside the tube, the tool should not be used. Never use anything with sharp or rigid
edges, which could cut into the copper tubing.
Lubrication
Compressor.
When starting and charging the unit, the oil sight glass (33) in the crankcase of the
compressor should be watched carefully for the first hour to make certain the proper lubrication is
being maintained. The oil may become low in the crankcase on an initial start-up if electrical current
has been interrupted to the machine, thus de-energizing the compressor crankcase heater.
Before starting the machine again, the heater should be energized for a time period of at least two
hours to evaporate refrigerant that may have condensed in the crankcase during the shutdown period.
If the level is low after start-up, it should begin to return after a short period of operation.
The oil level should be checked frequently, particularly during the start-up operation, to see that a
sufficient amount of oil remains in the crankcase. While it is important to observe the oil splash during
operation, the true level can be obtained only when the compressor is stopped. With the compressor
idle, the oil level should be at a height of 1/4 to 1/2 of the sight glass but never out of sight above it.
The machine is properly charged with oil for the test operation, but it may be necessary to add some oil
when or if new refrigerant is added to the system. Generally, air-cooled machines will require
additional refrigerant and oil to compensate for long piping runs to the condenser.
Refrigerant
Recommended Lubricants
Type of Lubricant
HCFC-22 (R-22) Suniso 3GS, Texaco WF32, Calumet RO15 (Witco)
Mineral Oil
R-404A
Mobil EAL ARCTIC 22 CC, ICI (Virginia KMP) Emkarate
RL 32S
Polyol Ester Oil
TABLE 7-3
Recommended Lubricants
Compressor
HP
Oil Charge
(oz)
6DYN & 6DY3
21
140
6DNN & 6DN3
24
140
TABLE 7-4
Compressor Oil Capacity
Summary of Contents for P18FXT
Page 4: ...Vogt Tube Ice Machines Installation Service Manual and Parts Catalog 12A4171M08 10TA Model ...
Page 10: ...10TA Service Manual TABLE OF CONTENTS vi BLANK ...
Page 20: ...10TA Service Manual INTRODUCTION 4 14 14 1 10 BLANK ...
Page 40: ...10TA Service Manual INSTALLING YOUR TUBE ICE MACHINE 4 14 14 3 18 BLANK PAGE ...
Page 50: ...10TA Service Manual START UP AND OPERATION 4 14 14 5 6 BLANK ...
Page 60: ...10TA Service Manual ELECTRICAL CONTROLS 4 14 14 6 10 BLANK ...
Page 112: ...10 8 10TA Service Manual OPTIONS AND ACCESSORIES BLANK ...
Page 120: ...10TA Service Manual TABLES CHARTS 7 2 14 11 8 BLANK ...