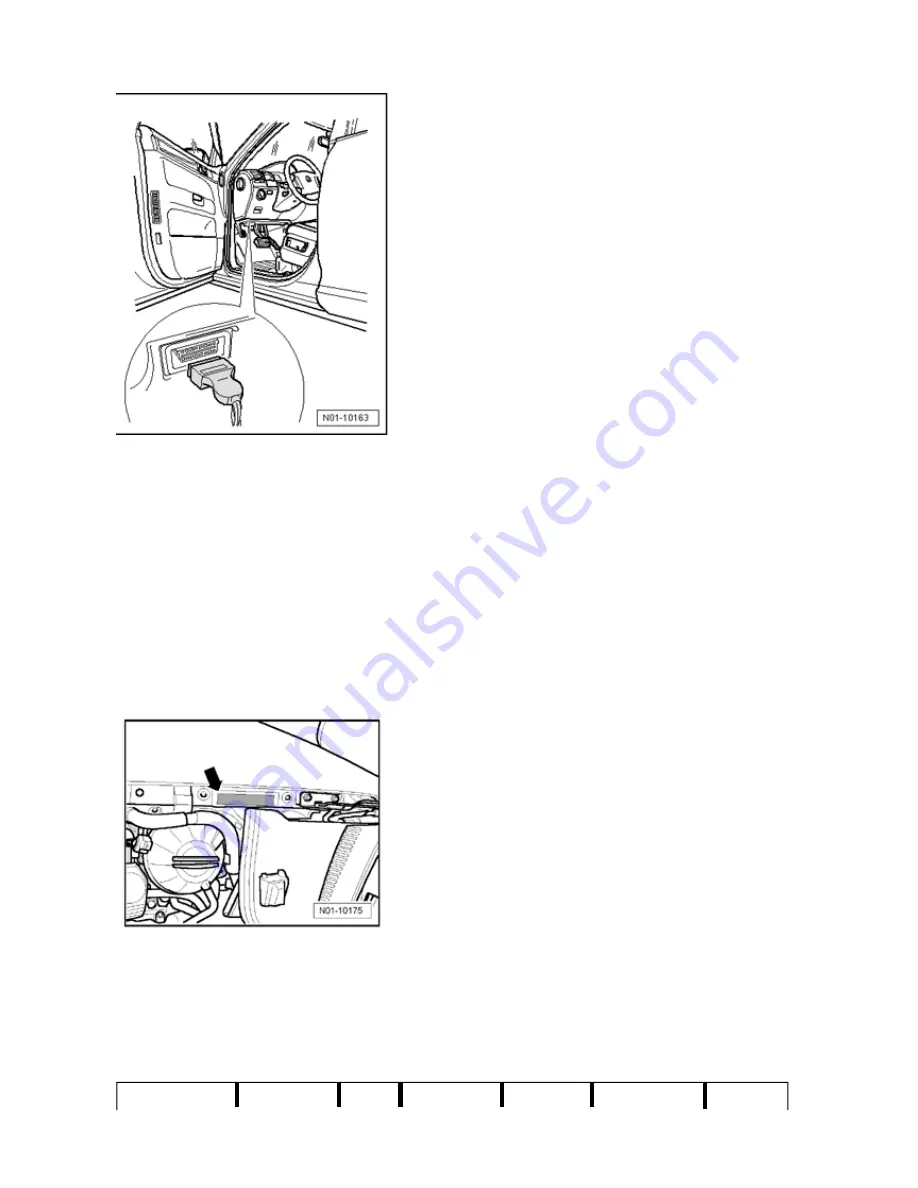
- Perform the following work procedure:
- Connect diagnosis cable connector to data link
connector.
- Turn on the tester.
- Switch ignition on.
Now follow information given on screen to start the desired
functions.
Vehicle Identification Number (VIN)
Component location engine compartment
Vehicle Identification Number (VIN) is located on extension
of longitudinal member
- arrow -
.
Meaning of Vehicle Identification Number (VIN):
000 234
Page 6 / 10
General