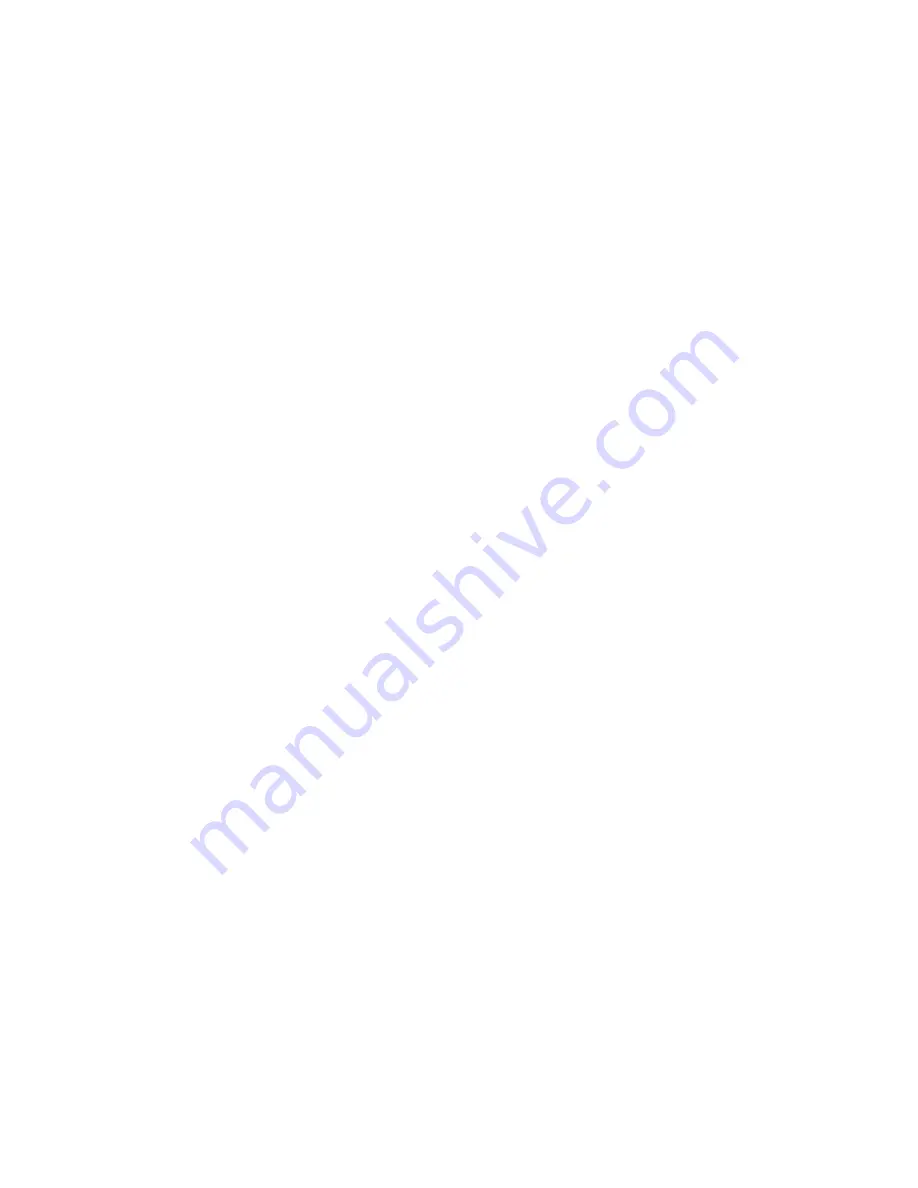
33
SUCTION LINE SOLENOID TESTING
To check for leaking valve seats, follow the procedure
outlined below. The liquid line solenoid must remain open
for this test.
NOTE
Machine barrels must NOT contain frozen product
for this test.
A.
Turn the Main Power OFF/ON switch and both
Freezing Cylinder OFF/ON switches to the OFF
position.
B.
Attach a gauge to the Schrader valve located after
the evaporator of the side being tested.
C.
Place the Main Power OFF/ON switch to the ON
position.
D.
Place the opposite side Freezing Cylinder OFF/
ON switch to the ON position.
NOTE
If checking the solenoid on the left side, place the
right side Freezing Cylinder OFF/ON switch to the
ON position. For the right side, place the left side
switch to the ON position.
E.
Start a freezing cycle of the opposite side by
pressing the Push To Freeze button or by pulling
the spigot handle.
F.
If the pressure drops more than 3 psi in 30 seconds
on the side being tested, the suction line solenoid
valve seat leaks and should be replaced. Repeat
the procedure for the other side.
LIQUID LINE SOLENOID TESTING
The following test will check if a liquid line solenoid has a
leaking valve seat. The power to the solenoid is discon-
nected and refrigerant flow is monitored through the sys-
tem. If the valve seat does not leak, the suction pressure
during the test will read the same as the pressure when only
the hopper refrigeration is running.
A.
Turn the Main Power OFF/ON switch and both
Freezing Cylinder OFF/ON switches to the OFF
position.
B.
Disconnect a terminal on each of the liquid line
solenoids.
C.
Insulate the terminals with electrical tape.
D.
Attach gauges to the Schrader valves located after
the evaporators on the suction line.
E.
Turn the Main Power OFF/ON switch and both
Freezing Cylinder OFF/ON switches to the ON
position
F.
Start a freezing cycle by pressing the Push To
Freeze button or by pulling on the spigot handles.
G.
The gauges should show approximately 14 psig
after 1 minute.
H.
Watch the pressure in both freezing cylinders. The
freezing cylinder with the greatest pressure rise
may have a leaking valve seat.
SOLENOID MAGNETIC COIL REMOVAL
A.
Remove the side panel.
B.
Disconnect the electrical wires.
C.
Remove the retainer screw from the top of the
solenoid and pull the magnetic coil off.
SOLENOID MAGNETIC COIL INSTALLATION
To replace the magnetic coil, perform the following proce-
dures:
A.
Connect the two electrical wires to the magnetic
coil.
B.
Push the coil on to the solenoid valve stem.
C.
Make sure there isn’t any foam insulation between
the valve coil and valve body. Trim any excess
insulation.
D.
Install retainer screw onto top of coil.
SOLENOID VALVE REMOVAL
A.
Identify and disconnect the two wires from the
solenoid coil.
B.
Remove the retainer holding the coil to the solenoid
body and remove the coil.
C.
Recover refrigerant charge per instructions in
Section 5.2.
D.
Remove insulation around valve and attached
refrigeration lines.
E.
Apply heat sinks (wet cloth) to the insulated
refrigerant lines near the valve.
F.
Leave a port open to prevent pressure buildup
during solenoid removal
G.
Unsweat the solenoid and remove.
SOLENOID VALVE REPLACEMENT
To replace the solenoid, perform the following procedures:
A.
Position the new solenoid with the arrow pointing
toward the direction of refrigerant flow.
B.
Apply a heat sink (wet cloth) to the solenoid valve.
C.
With the suction and discharge ports open, braze
the solenoid into the system.
D.
Remove the heat sink from the valve.
E.
Replace insulation around valve.
F.
Replace the filter drier. Refer to Section 5.8 for
details.
G.
Evacuate and recharge system per instructions in
Section 5.2.
Summary of Contents for Stoelting E131-OT2
Page 1: ...Model E131 OT2 F131 OT2 SERVICE MANUAL Manual No 513648 Rev 0 https appliancetechmanuals com ...
Page 2: ...https appliancetechmanuals com ...
Page 14: ...8 https appliancetechmanuals com ...
Page 16: ...10 https appliancetechmanuals com ...
Page 26: ...20 Figure 4 2 IntelliTec Control Menu Settings https appliancetechmanuals com ...
Page 52: ...46 8 2 AUGER SHAFT AND FACEPLATE PARTS https appliancetechmanuals com ...
Page 60: ...54 8 9 REFRIGERATION DIAGRAM WIRING DIAGRAM 01 2 3 3 3 3 https appliancetechmanuals com ...