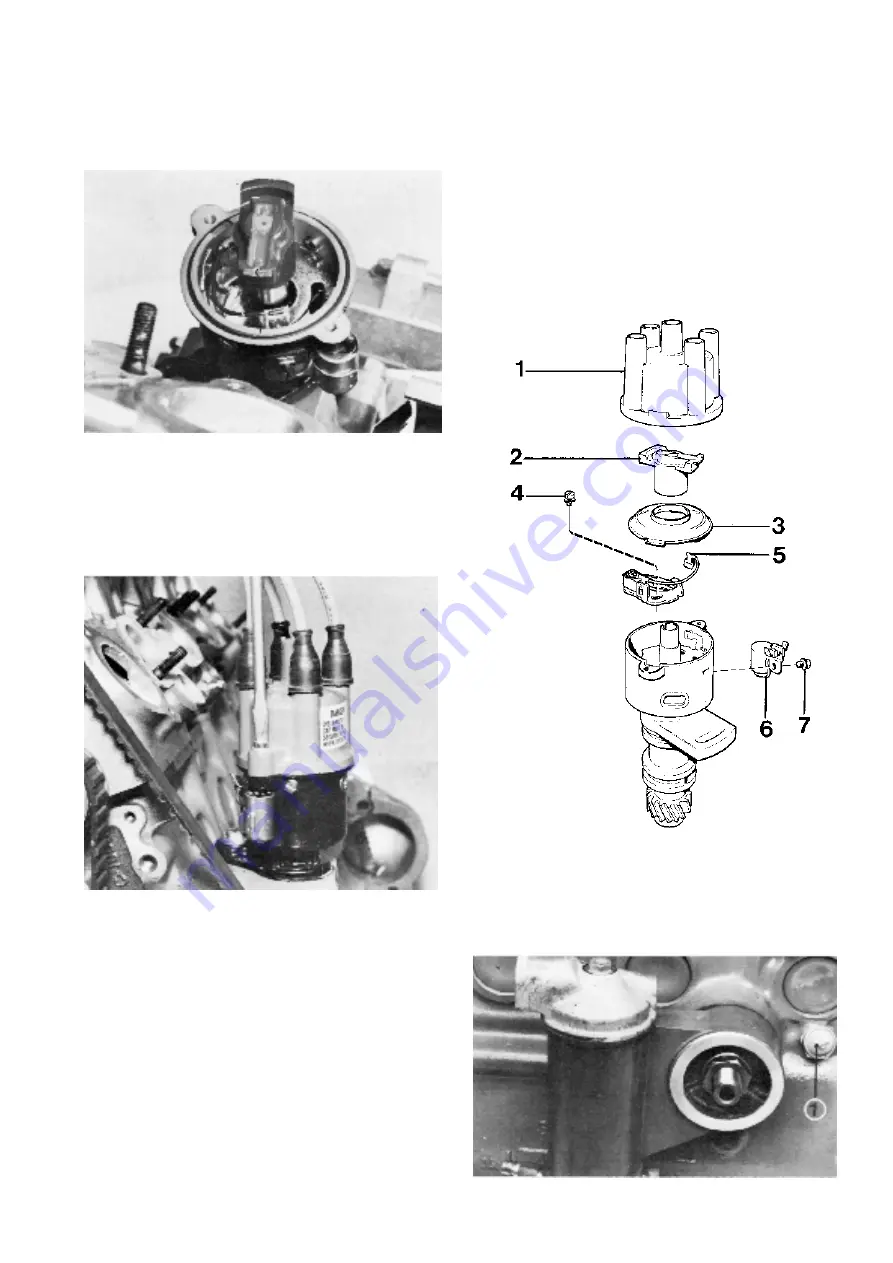
47
151. Press the distributor into position in the crankcase
and check that the line on the rotor and the line on
the distributor housing are opposite each other.
Tighten the distributor in this position.
152. Fit the distributor cover.
Replacing contact breakers
153. Remove the distributor cover (1), rotor(2) and the
washer (3). Then undo the screw (4) and the tab
connection (5) and then remove the contact
breakers. Fit a new breaker set. The contact brea-
king gap is 0.40 mm (0.016 in.). Change the con-
denser (6) at the time by undoing the screw (7).
Tighten a new condenser and connect the tab
connection and replace the washer. Press the ro-
tor in position and refit the distributor cap.
NOTE! The cam angle is checked and adjusted
during test running. See “Technical Data”
154. Fit the oil pressure sender (1). The tightening tor-
que is 12 Nm (1.2 kpm) (8.9 lbf. ft.). Lay a new
O-ring in the oil cooler’s groove and fit the oil coo-
ler to the engine. Do not tighten the nut before the
cooling water pipe has been fitted. Only AQ145.
Summary of Contents for AQ125A
Page 1: ...Workshop Manual Engine Unit AQ125A B AQ145A B C 2 0 ...
Page 2: ......
Page 74: ...7739856 8 English 11 1998 ...