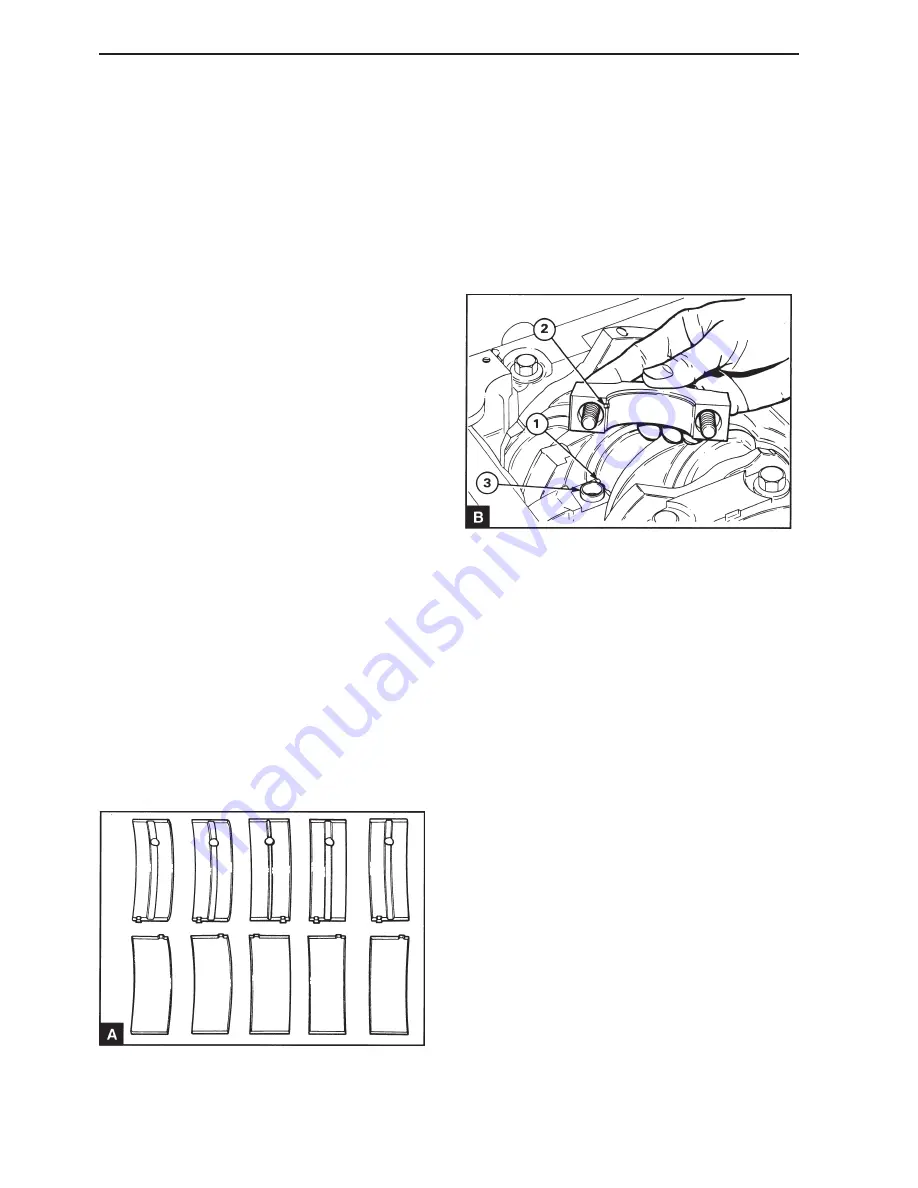
50
Crankshaft assembly
Main bearings, replacement
(14A-06)
(with crankshaft installed)
If the front bearing is to be removed the oil pump
must also be removed. Removing the main bearing
cap with the pump in position damages the pump
joint.
If the rear bearing cap is removed with the flywheel
installed, sealant must be applied to the underside
of the bearing cap rear surface before it is rein-
stalled.
1
Drain the engine oil and remove the oil pan, opera-
tion 18A-03.
2
Remove the oil screen and extractor pipe if re-
quired, operation 18A-04.
3
Remove the screws for the bearing cap and remove
the cap. Remove the lower bearing shell from the
cap.
4
Press the upper bearing shell on with a suitable tool
on the opposite side to the lug. This presses the lug
out of the cut out in the bearing housing. Turn the
crankshaft carefully to feed the bearing shell out of
the housing. Make a note of the respective bearing
shell locations.
5
Clean the upper bearing shell and lubricate the
bearing surface with fresh engine oil.
NOTE! There is only a lubrication hole in the upper
bearing shell and it must therefore be placed
against the cylinder block. The bearing shells for
the central main bearing are wider than the other
bearing shells (A). The bearing shells for the central
main bearing also have differently located lugs.
6
Insert the flat edge of the upper bearing shell be-
tween the main bearing journals and the side of the
bearing housing which has a cut out for the lug.
Slide the bearing shell into the bearing housing until
the lug on the bearing shell is well inside the cut out
in the bearing housing (B1).
7
Clean the lower bearing shell and lubricate the bear-
ing surface with fresh engine oil.
8
Install the bearing shell in the cap with the lug slid
well into the cut out in the cap (B2).
9
Check that the guide sleeves (B3) are correctly in-
stalled in the bearing cap or in the cylinder block.
Install the bearing cap so that both the bearing
shells lugs are turned in the same direction.
Summary of Contents for MD22
Page 1: ...Engine repair MD22 TMD22 TAMD22 Workshop Manual 2 0 A ...
Page 2: ......
Page 129: ...127 Notes ...
Page 130: ...128 Notes ...
Page 132: ...7738684 5 English 04 1999 ...