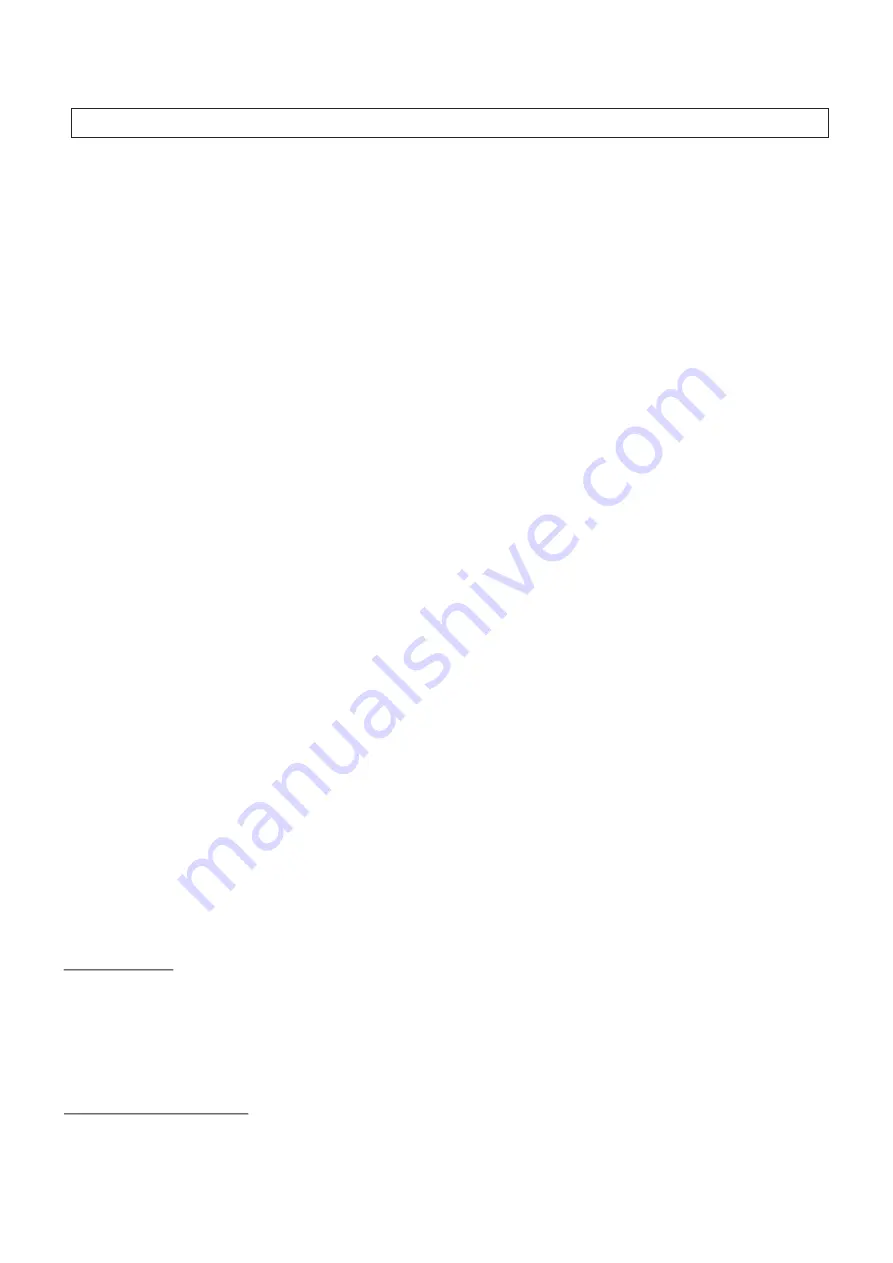
3
1.1
General warnings
Make sure you have a complete copy of this manual and the enclosed Assembly Instructions available. Read
•
both documents fully and make sure you understand them adequately before proceeding with subsequent steps.
If you have any doubt about a task to be carried out, apply the criterion of maximum personal and collective safety.
Immediately interrupt your work, make everything done so far in complete safety, and ask for adequate
instructions, if necessary, from the manufacturer as well.
Check the integrity of the equipment when opening the packaging. Pay particular attention to damage to or
•
deformation of mechanical parts, which may result in breakage and/or malfunctions when in use. If any of these
are found, do not connect the machine to the power supply. Carry out these checks every time before use.
Before connecting the machine to the power supply, check that the indications on the data plate cor-respond to
•
the electricity supply. The data plate is located on the electronic motor (see par. 1.9).
Each and every person that may come into contact in any way with the product marketed by VORTICE S.p.A.,
•
and described here, must be adequately informed by the purchaser of about use, risks, dan-gers and safety
procedures, in the ways provided for by law and as described below in this document.
Conform to safety norms indicated for electrical equipement, and especially:
Conform to the assembly and installation instructions for the equipment.
•
Do not put items on top of the ceiling fan, and do not hang anything from the ceiling fan's blades.
•
Do not touch the ceiling fan when it is running, or immediately after it has stopped. Remember that the motor
•
could be hot.
Never immerse the equipment in water or any other liquid, and do not use water, especially pressur-ised, for
•
washing or cleaning the fan or its parts. This equipment is not designed to be impermeable to water. Do not touch
the equipment if it gets wet by accident. Immediately disconnect the power supply by switching off the switch on
the electrical panel for your system, and immediately disconnect the feeder before touching the equipment. Use
suitable means to indicate that reinstating the power supply at the panel is forbidden.
Do not touch the equipment with wet and/or damp hands.
•
Do not use accessories, spare parts and/or components that are not indicated or supplied by the manufacturer
•
Do not pull the power supply cable or expose it to a risk of being sheared.
•
If a fault occurs and/or the equipment works badly, switch it off immediately and disconnect the power supply.
•
Use suitable means to indicate that reinstating the power supply at the panel is forbidden. Do not attempt to open
or tamper with the equipment. Contact VORTICE's technical service department.
1.2
Conventions used in this manual
The Manual is broken down into independent chapters, each of which is addressed to a specific type of opera-tor
(INSTALLER, MACHINE OPERATOR AND MAINTENANCE TECHNICIAN), for which the skills required to operate
on the machine in safety have been defined.
The sequence of the chapters follows the temporal logic of the machine's lifespan.
To facilitate immediate understanding of the text terms, abbreviations and pictograms are used, the meaning of
which is indicated below.
ABBREVIATION
Cap. = Chapter
Par. = Paragraph
Pag. = Page
Fig. = Figure
Tab. = Table
UNIT OF MEASUREMENT
The units of measurement used are those from the International System (SI).
1 INTRODUCTION
Summary of Contents for Nordik HVSL Super Blade 110 V Series
Page 1: ...NORDIK HVLS SUPER BLADE E SUPER BLADE 110 V Instruction booklet COD 5 571 084 939 23 07 2021 ...
Page 25: ...25 INVERTER MOTOR ELECTRONICS QUICK CONNECTORS ...
Page 28: ...28 Destratification Fan assembly ...
Page 56: ...56 Attachment 2 Electric connection ...
Page 67: ...67 Multi wire diagram for system wiring SINGLE PHASE 85 264V 50 60 Hz ...
Page 78: ......
Page 79: ......