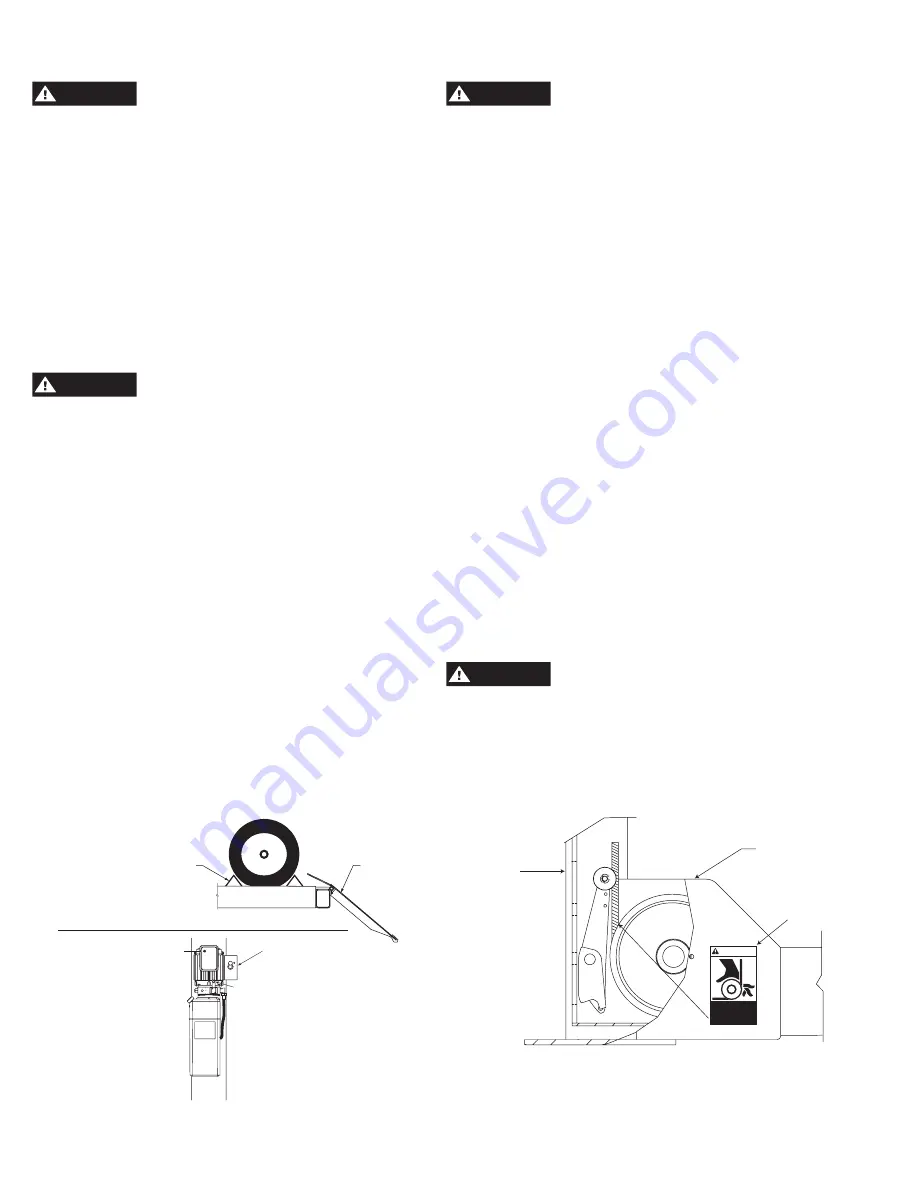
4
OPERATING INSTRUCTIONS
WARNING
To avoid personal injury and/or property dam-
age, permit only trained personnel to operate lift.
After reviewing these instructions, get familiar with lift con-
trols by running the lift through a few cycles before loading
vehicle on lift.
Observe and heed SAFETY and WARNING labels on the lift.
1. Loading: Lift must be fully lowered and no one in service
bay while the vehicle is brought on lift.
2. If lift is equipped with rolling jacks, jacks must be fully
lowered and the rear jack pushed toward center of lift to
provide under car clearance.
WARNING
Engage runway locks before raising vehicle on
jacks! DO NOT operate lift while jacks are engaged with a
vehicle!
3. Stop vehicle when it contacts the front wheel stops. At all
times, be sure rear wheels are forward of the ramp/chocks
and the ramp/chocks will clear tires when the lift is raised,
Fig. 1. Driver and passengers must exit before raising.
4. Place triangular wheel chocks on each side of one of the
rear tires, Fig. 1.
5. To Raise Lift: Push the “RAISE” button on the power unit.
Release button at desired height, Fig. 2.
6. For Rolling Jack Operating Instructions see Rolling Jack
Installation, Operation and Maintenance Instructions in the
rolling jack shipping carton.
7. Before Lowering Lift: Be sure no one is in the lift area and
that all tools, tool trays, etc. have been removed from under
the lift and vehicle.
CAUTION
Keep hands clear
of yoke ends
during lift
operation.
Fig. 2
Fig. 3
Triangular
Wheel Stops
Rear Wheel
Chock
Fig. 1
Latch Release
Air Button
LOWERING
Handle
RAISE
Button
Column
Yoke End
Hands
Clear
Warning
WARNING
The runways, ramps and connecting yokes at
each end of lift are designed to rest on the floor when fully
lowered. Observe pinch point warning decals, Fig. 3.
8. Repeat Step 2.
9. To Lower Lift: If lift has been resting on the locking latches,
lift must be raised high enough for all four latches to clear
the latch plate slots inside the columns.
10. Actuate the latch release valve on the power unit column to
disengage all four locking latches, Fig. 2. Hold actuator until
lift has fully lowered.
Note: If actuator on air valve is released, the latches will auto-
matically reset to the engaged position.
11. Push the lowering handle on the power unit to lower lift, Fig.
2. Lowering speed can be controlled by the force applied to
the lowering handle.
12. Observe lift and vehicle to be sure lift is level while being
lowered. If not, STOP repeat Steps 10 through 13.
13. Fully lower lift, remove the triangular wheel chocks and
check to be sure area is clear before removing vehicle from
lift, Fig. 1.
14. If your lift is not operating properly, DO NOT use until adjust-
ments or repairs have been made by qualified lift service
personnel.
WARNING
Keep hands clear of yoke ends while the lift is
being raised or lowered, Fig. 3.
*Maximum operation pressure is:
2500 psi (17237 kPa) for CR14
Summary of Contents for LP60032
Page 11: ...Notes...