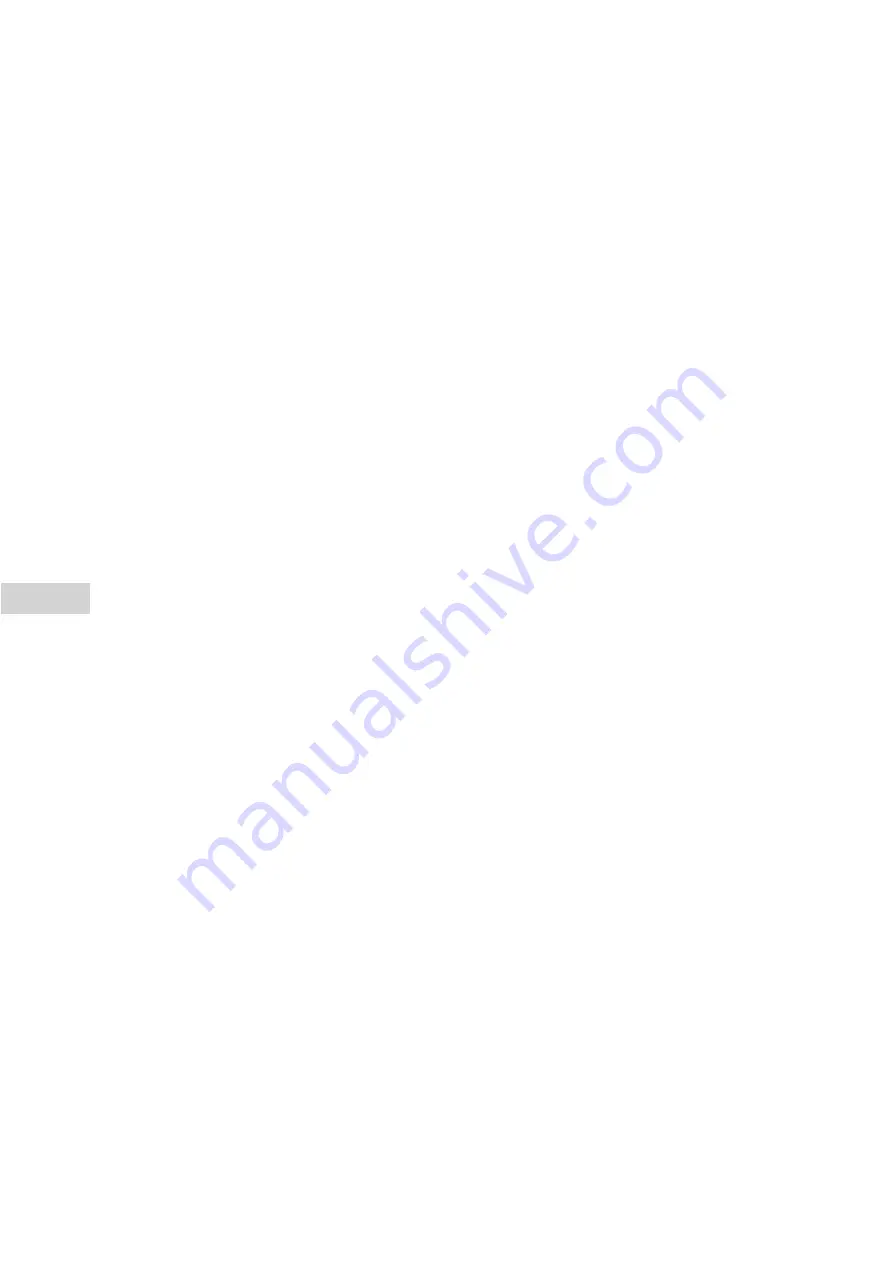
23
24
OIMM – VENTUS PRO
After start up and initial satisfactory operation of two weeks, it is recommended to have the following checks:
•
belt drive alignment and belt tension,
•
motor running current,
•
bearing temperature immediately after stop. Bearing temperature should not exceed 70C,
•
lubricate if necessary,
•
condition of filters,
•
condensate and drain, to see flow,
•
operation of control devices.
Investigate any changes to the fan. You may have more detailed explanation of problems and possible causes
in “troubleshooting” section. Consult your manufacturer or other qualified consultant for questions concerning
changes observed during periodic inspections.
If excessive vibration is observed, stop the fan until the cause is corrected. Check for material build up on the
impeller which causes an imbalance and leads to the fatigue failure or impeller.
Changes in the sound level of the fan may indicate troubleshooting is required.
If the motor temperature is high check cooling fan of the motor. It may be blocked or broken. Also check the input
current. An increase in current may indicate that some major changes have been made in system.
High bearing temperatures usually caused by improper lubrication. If the cause of the problem is not easily seen,
experienced personnel must examine the equipment before running it again.
»
AFTER TWO WEEK OPERATION
A preventive maintenance program is an important aspect of an effective safety program. Maintenance works
should be performed by experienced and trained personnel. Do not attempt maintenance unless electric supply
has been locked out and the impeller has been secured. Before the maintenance operation, the safety precautions
should be taken by locking out the main and maintenance switch and protecting against unlocking by anybody
else.
Especially at the hygienic air handling units, filters, coils, (by disconnecting the flange connections), droplet
eliminator and sound attenuators can be taken out from the service doors. Besides, all components can be
taken out from the unit for cleaning and disinfection processes.
In general air handling unit do not require special attention other than routine cleaning and maintenance
work. Frequency of maintenance depends on operating conditions. Following is the recommended schedule
maintenance.
Periodic checks should be made for thermal and acoustic lining and electrical insulation of the unit sections. Also
connecting cables and control panels should be checked. Any metal surface which shows signs of deterioration
should be cleaned.
Bols, nuts and other assembling elements should be checked. Any missing bolts, nuts and screws should be
replaced.
To clean the damper compressed air can be used. Do not lubricate the shaft of the damper.
Impurities on the droplet eliminator blades should be cleaned regularly. The period changes according to the
operating conditions and the air quality. As cleaning media any de-scaler available on the market can be used.
For the best cleaning process of the droplet eliminator at the hygienic air handling units it should be taken out
from the unit and disassembled by unscrewing.
To clean the inner surface of the unit (after necessary components taken out) water / steam spray and cotton or
directly wet cotton can be used by wiping.
MAINTENANCE
3.10