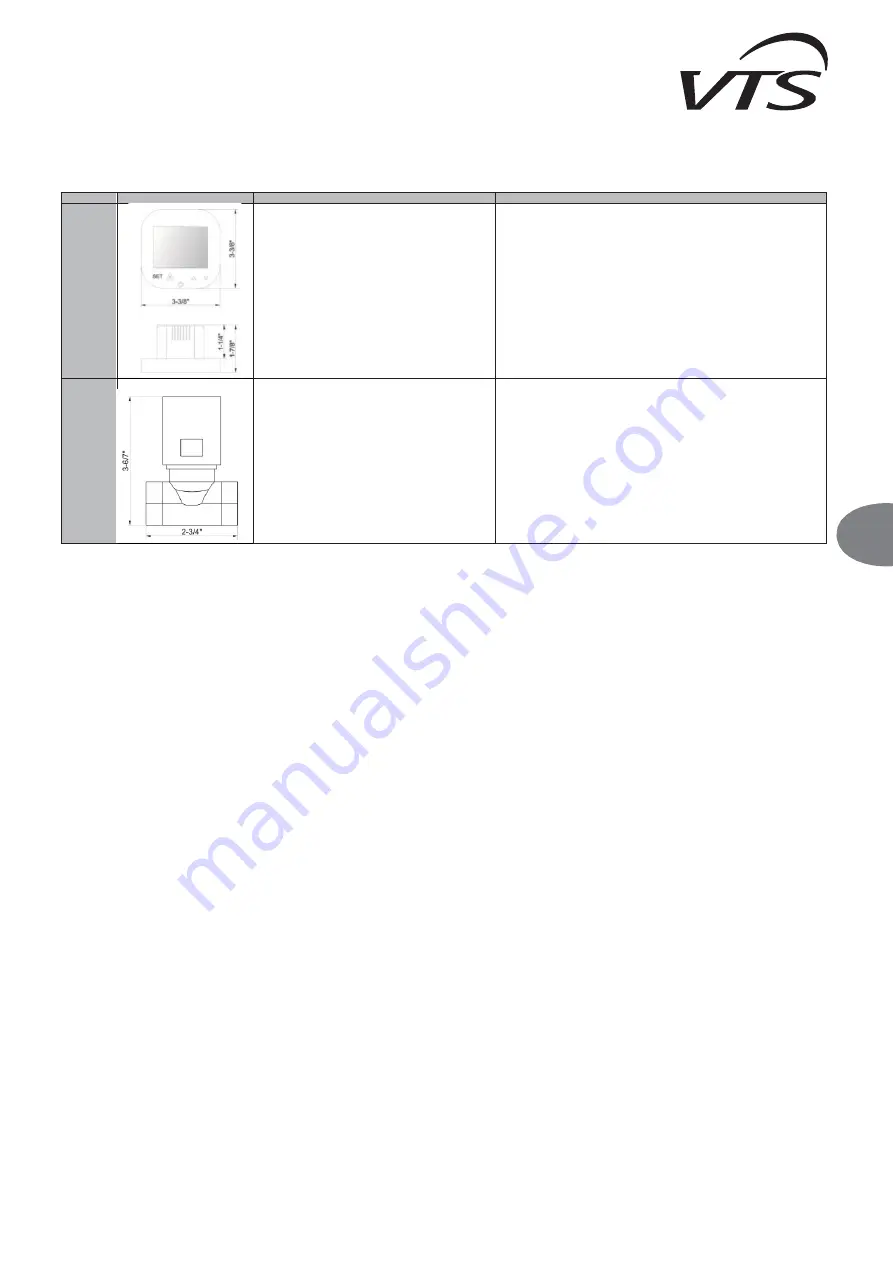
HM
I-
W
ING
EC
4. ELEMENTS OF CONTROLS.
Electrical connections can be carried out only by qualified electricians, according to the binding regulations of:
●
industrial safety;
●
installation instructions.
●
technical documentation for each individual element of automatics.
IMPORTANT!
Before starting the controls installation, please read the operation and installation instruction for each of them. Instructions are included in the box for each control.
MODEL
DIAGRAM
TECHNICAL DATA
COMMENTS
H
M
I W
IN
G
U
L
HMI-WING UL
•
Device operation: touch buttons
•
Power supply: 120-240 V AC
•
Temperature
measurement: 14 °F ... 210 °F
; NTC10K
•
Outputs:
- 1 analog output 0-10V (8 bit, Imax = 20 mA)
- 2 relays outputs (250 VAC, AC1 500 VA dla 230 VAC)
•
Communication: Modbus RTU
•
used for control all types of WING EC curtains
•
touch control panel
•
the main on / off switch (ON / OFF)
•
three-stage adjustable fan speed of the EC motor
•
built-in thermostat with possibility weekly programing
•
continuous mode
•
function of heating and ventilation
•
door sensor operation
•
3-levels of heating power
•
RS 485 with ModbusRTU
•
Suggested cross sections of electrical cables::
- L, N : 2x18 AWG
- H1, H2 : 2x18 AWG
- AO, GND : 2x18 AWG
- RS 485 : 2xAWG18
T
W
O
-W
A
Y
V
A
LV
E
WIT
H
AC
T
U
A
T
OR
TWO-WAY VALVE
●
Terminal diameter:
3/4”
●
Mode of operation: two-way ON/OFF
●
Maximum differential pressure: 13psi
●
Pressure class: PN 16
●
Kvs flow ratio: 2.65 CFM
●
Maximum temperature of heating medium: 200
°F
●
Parameters of working environment: from 32 to
140°F
VALVE ACTUATOR
●
Power consumption: 7 VA
●
Supply voltage: /-10%
●
Closing/opening time: 4-5/9-11 s
●
Position without power: closed
●
Level of protection: IP54
●
Parameters of working environment: from 89 to 200
°F
●
It is recommended to install a two-way valve on the return pipeline.
●
The drawings with the elements of automatics contain only visualizations of
sample products.
●
It is recommended to connect the supply, using a conductor of the min. size
0.08x0.03 in
2
.
●
The drawings with the elements of automatics contain only visualizations of
sample products.
IMPORTANT!
If required, the conductors that belong to additional elements of control automatics (thermostat, door switch, wall-mounted controller) should be installed in separate cable
channels, out-of-parallel to the supply conductors.
5. START-UP, OPERATION, MAINTENANCE
5.1. START-UP/PUTTING INTO OPERATION
●
Prior to the commencing of any installation or maintenance work, disconnect power supply and secure it against unintentional reactivation.
●
It is recommended to use filters in the hydraulic system. It is recommended to clean/rinse the system, draining a few liters of water, prior to the connecting of hydraulic conduits (the supply conduits,
in particular).
●
It is advised to use vent valves in the highest point of the system.
●
It is recommended to install shut-off valves directly after the device, should the disassembly of the device be necessary.
●
All protective equipment is to be installed before the pressure increases, according to maximum the permissible pressure rating of 232 psi.
●
Hydraulic connection should be free of any stresses and loads.
●
Check the correctness of hydraulic connections (leak-tightness of the vent, collecting pipes, correctness of fittings installation), prior to the initial start-up of the device.
●
It is recommended to check the correctness of electrical connections (of automatics, power supply), prior to the initial start-up of the device. It is advised to use an additional, external residual-
current protection.
IMPORTANT!
All connections should be carried out, according to this technical documentation and the documentation delivered with automation equipment.
5.2. OPERATION AND MAINTENANCE
●
It is advised to carefully analyze all the operational and installation guidelines listed in chapter 3 and 4.
●
The casing of the device does not require maintenance.
●
The heat exchanger should be cleaned on a regular basis from dust and fat deposit. It is especially recommended to clean the exchanger before the heating season with the use of compressed air
from the air intake side (after removing the inlet grid). You should pay special attention to the exchanger's lamellae which are very delicate.
●
Should the lamellas be deformed (bent), straighten them with a special tool.
●
The fan's motor does not require any exploitation service, the only service activities that may be necessary concern cleaning the air intakes from dust and fat deposit.
●
Disconnect phase voltage, if the device is shut down for longer periods of time.
●
The heat exchanger does not have any anti-freezing protections.
●
It is recommended to provide a periodical purging of the heat exchanger, preferably using compressed air.
●
Should the temperature in the room drop below
32°F
, with a simultaneous drop of the heating medium temperature, there is a risk that the heat exchanger might freeze (crack).
●
The level of air pollutants should meet the criteria allowable concentrations of pollutants in indoor air, for non-industrial areas, the level of dust concentration up to 1.87x10
-5
lbs/ft
3
.
●
It is forbidden to use device for the duration of the construction works except for the start-up of the system.
●
The equipment must be operated in rooms used throughout the year, and in which there is no condensation (large fluctuations in temperature, especially below the dew point of the moisture
content). The device should not be exposed to direct UV rays.
●
The device should be operated at the supply water temperature up to 200
°F
with working fan.
EN
Summary of Contents for WING C100-200
Page 15: ...15 9 ELECTRICAL DIAGRAMS 9 1 Electrical diagram of WING W100 200 EC 1 240V ...
Page 17: ...17 9 3 Electrical diagram of WING E100 EC 1 240V ...
Page 18: ...WING W100 200 WING E100 200 WING C100 200 18 9 4 Electrical diagram of WING E100 EC 3 240V ...
Page 19: ...19 9 5 Electrical diagram of WING E100 EC 3 480V ...
Page 21: ...21 9 7 Electrical diagram of WING E150 200 EC 3 480V ...