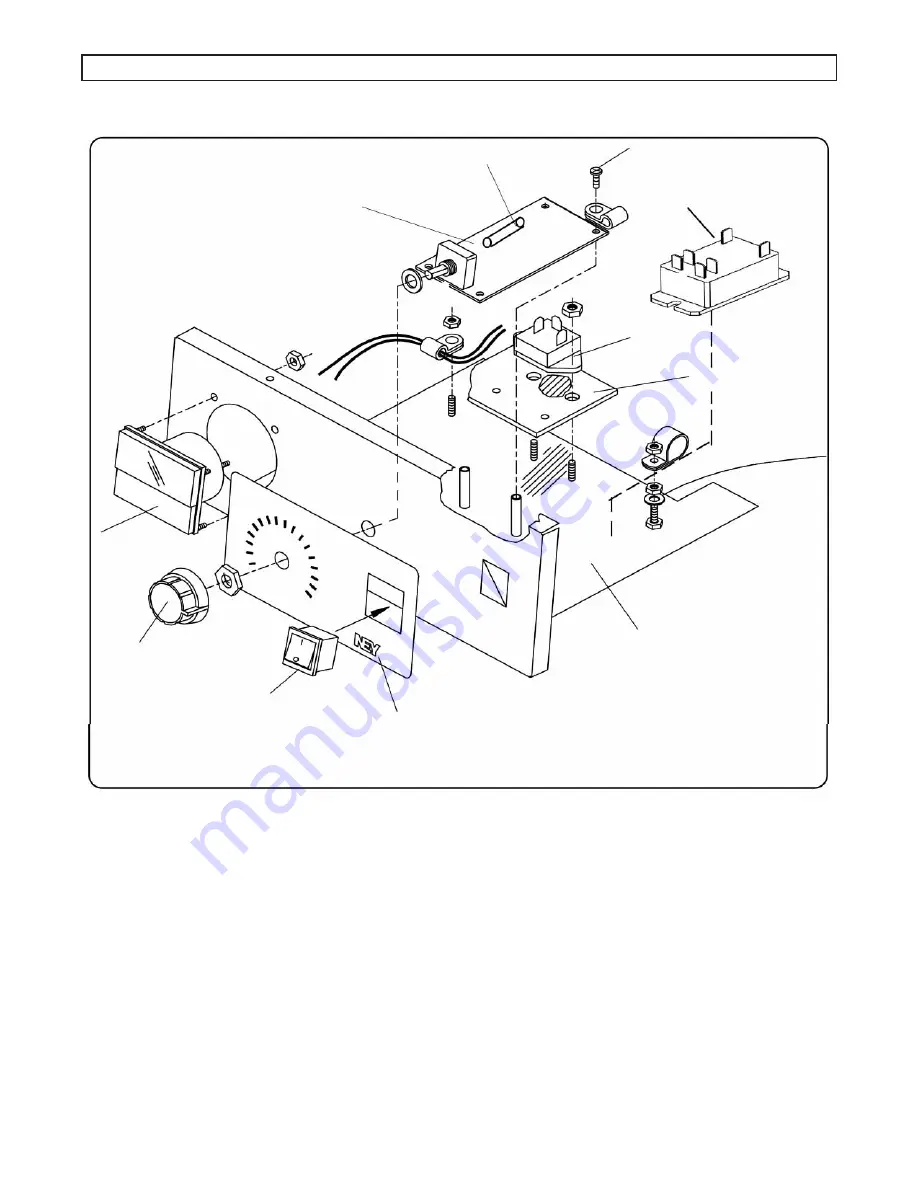
7.6 A- CONTROLLER PARTS
7 – 5
SECTION 7 - SERVICE PARTS - A-CONTROL
CONTROL PCB
(R9493348) 100-120V A-130
(R9493449) 200-240V A-130
(R9493349) 100-120V A-550
(R9493450) 200-240V A-550
(R9493451) 200-240V A-1750
FUSE (20A) - S/N 9525 and
9320072 earlier
SCREW, 6-32 x .375
RELAY, (1750 ONLY)
(9320075)
TRIAC
(9303015)
HEATSINK
PYROMETER
(9390451)
KNOB, SET POINT
(9355026)
POWER SWITCH
(9306038)
OVERLAY
(9354229) A-130
(9354230) A-550
(9354231) A-1750
CONTROL DRAWER
(9493316) A-130
(9493356) A-550
(9493386) A-1750
Summary of Contents for 3-130
Page 8: ...2 6 SCHEMATIC 2 4 SECTION 2 TROUBLESHOOTING A CONTROL...
Page 21: ...5 9 5 8 SCHEMATICS SECTION 5 TROUBLESHOOTING 3 STAGE POWER SUPPLY...
Page 22: ...5 10 SECTION 5 TROUBLESHOOTING 3 STAGE 5 8 SCHEMATICS TEMPERATURE CIRCUIT LCD DISPLAY CIRCUIT...
Page 23: ...5 11A 5 8 SCHEMATICS SECTION 5 TROUBLESHOOTING 3 STAGE MICROPROCESSOR CIRCUIT...
Page 24: ...5 11B 5 8 SCHEMATICS SECTION 5 TROUBLESHOOTING 3 STAGE...
Page 25: ...5 12 SECTION 5 TROUBLESHOOTING 3 STAGE PD A 5 9 WIRING DIAGRAM...