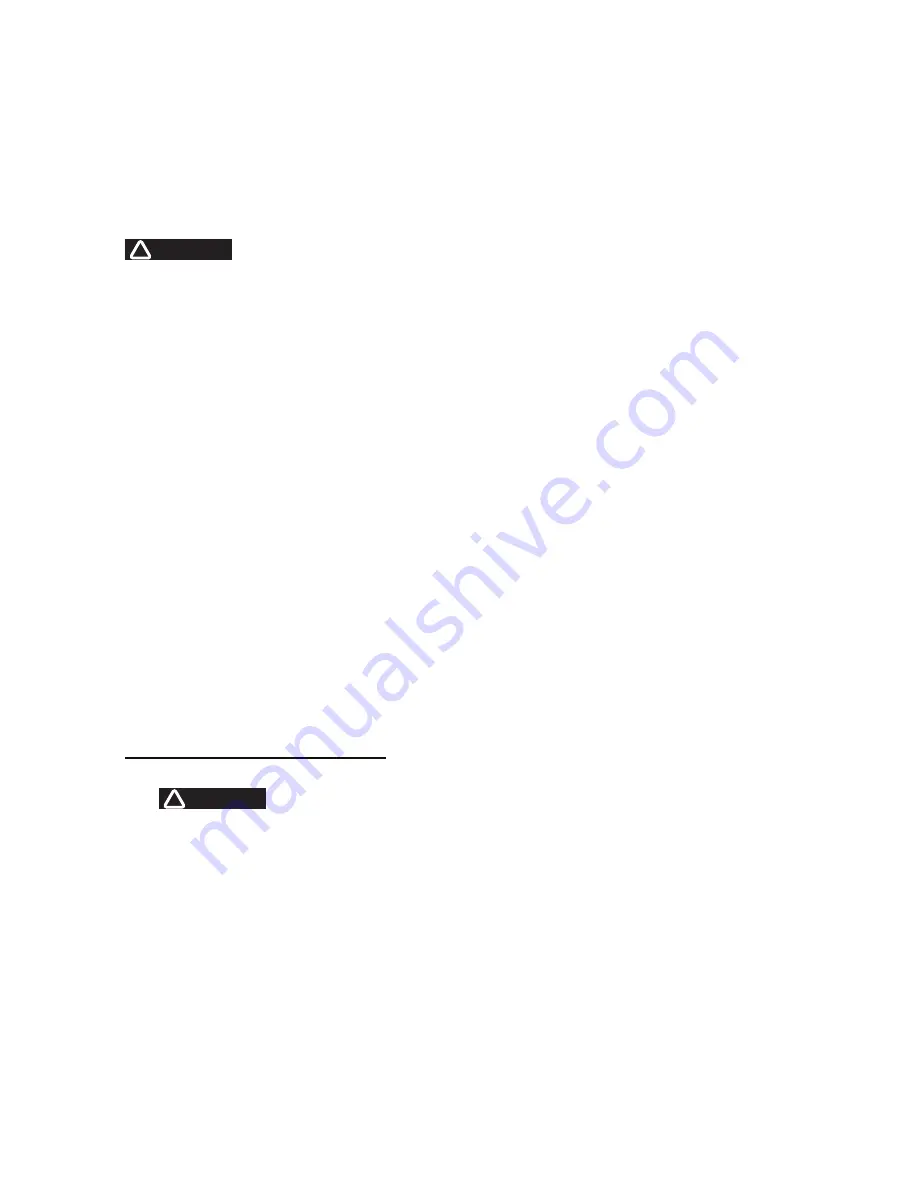
1b. Adjust the regulator to supply air at a higher pressure if increase drive depth is
desired. Decreasing supplied air pressure will result in the fastener driven depth also
being decreased.
1c. Test fire another fastener and check depth again.
CAUTION
!
l
Keep tool pointed in a safe direction at all times.
l
Never attempt to drive fasteners into materials too hard to penetrate, at too steep an
angle, or too near the edge of the workpiece. The fastener can ricochet causing personal
injury.
l
Disconnect tool from air supply before loading fasteners, doing any disassembly,
maintenance, clearing a jammmed fastener, leaving the work area, moving the tool to
another location, or handing the tool to another person.
l
Clean and inspect the tool daily. Carefully check for proper operation of trigger and safety
mechanism. Do not use the tool unless both the trigger and the safety mechanism are
functional, or if the tool is leaking air or needs any other repair.
2. Load the fasteners following the directions in the
LOADING THE FASTENERS
section.
3. Connect the tool to the air supply. Make sure the air pressure is within the minimum and
maximum operating pressures as noted in the
SPECIFICATIONS
section.
4. Hold the LONG ARM (
Parts List, 66
) and press the SHOE (
Parts List, 28
) against the
work surface.
5. Strike the HAMMER FACE (
Parts List, 10
) with the provided HAMMER (
Parts List, 68
)
to drive the fastener out.
6. Lift the tool off of the work surface.
7. In certain tight spaces, it may be useful to remove the handle.
8. Two spacers are provided, (
Schematic, 32 & 32a
). They provide a non-marring surface
on the bottom of the shoe. Choose the spacer thickness that places a fastener correctly
in the apex of the angle between the flooring tongue and its vertical edge.
CLEARING A JAMMED FASTENER
1.
CAUTION
!
Disconnect the tool from the air supply.
2. Open the magazine cover. Remove any remaining fasteners from the tool.
3. Use a slender, soft steel rod to push the drive blade to its uppermost position. Remove
the jammed fastener with needle nose pliers.
4. Follow instructions in
LOADING THE FASTENERS
to reload fasteners.
Summary of Contents for 827-1777
Page 13: ...13 SCHEMATIC DRAWING...