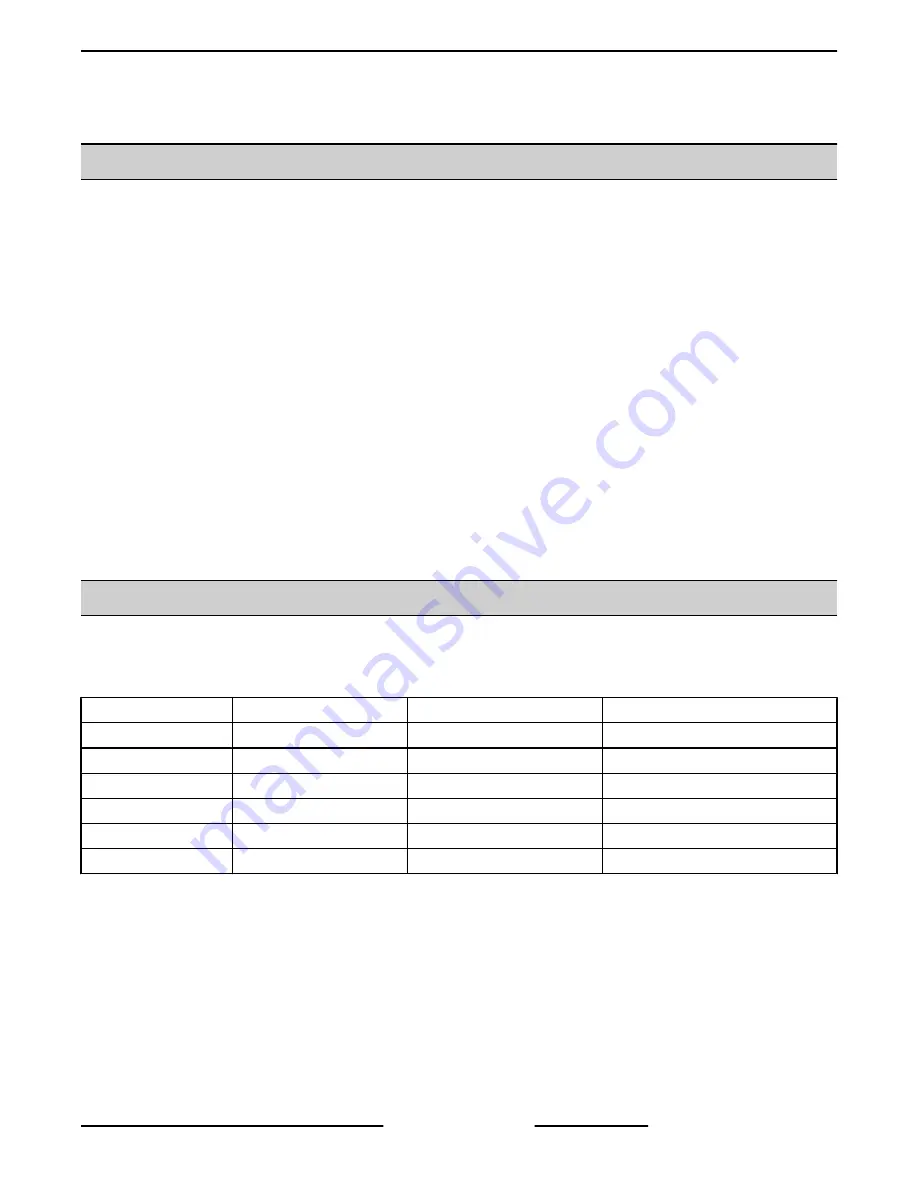
GENERAL
INTRODUCTION
General
The procedures in this manual apply to all models unless otherwise specified. The pictures and illustrations are of
a model K40GLT floor model tilting kettle unless otherwise noted. All information and specifications contained in
this manual are based on the latest product information available at the time of printing.
K Series - Tilting Kettles
The tilting kettles models are offered with a manual tilt mechanism as standard and are available with an optional
power tilt to automatically lower and raise the kettle. Kettles with the power tilt option can still be operated manually
using the crank handle as needed.
K Series - Floor Model Kettles
The 2/3 jacketed gas kettles are self contained. The lower two thirds of the kettle bowl is a double wall stainless
steel construction that provides a reservoir for a solution of heat transfer fluid and distilled water for improved heating
of the kettle contents. The kettles are used to prepare a variety of liquid or semi-liquid food products such as soups,
stews and sauces.
MODELS COVERED
All K Series kettles are mounted to the floor using legs with flanged feet for anchoring.
Model
Type
Gallons
Quarts
K20GL
Stationary
20
80
K40GL
Stationary
40
160
K60GL
Stationary
60
240
K20GLT
Tilting
20
80
K40GLT
Tilting
40
160
K60GLT
Tilting
60
240
K Series Gas Kettles 2/3 Jacketed Stationary and Tilting - GENERAL
Page 5 of 48
F45461 Rev. B (1117)