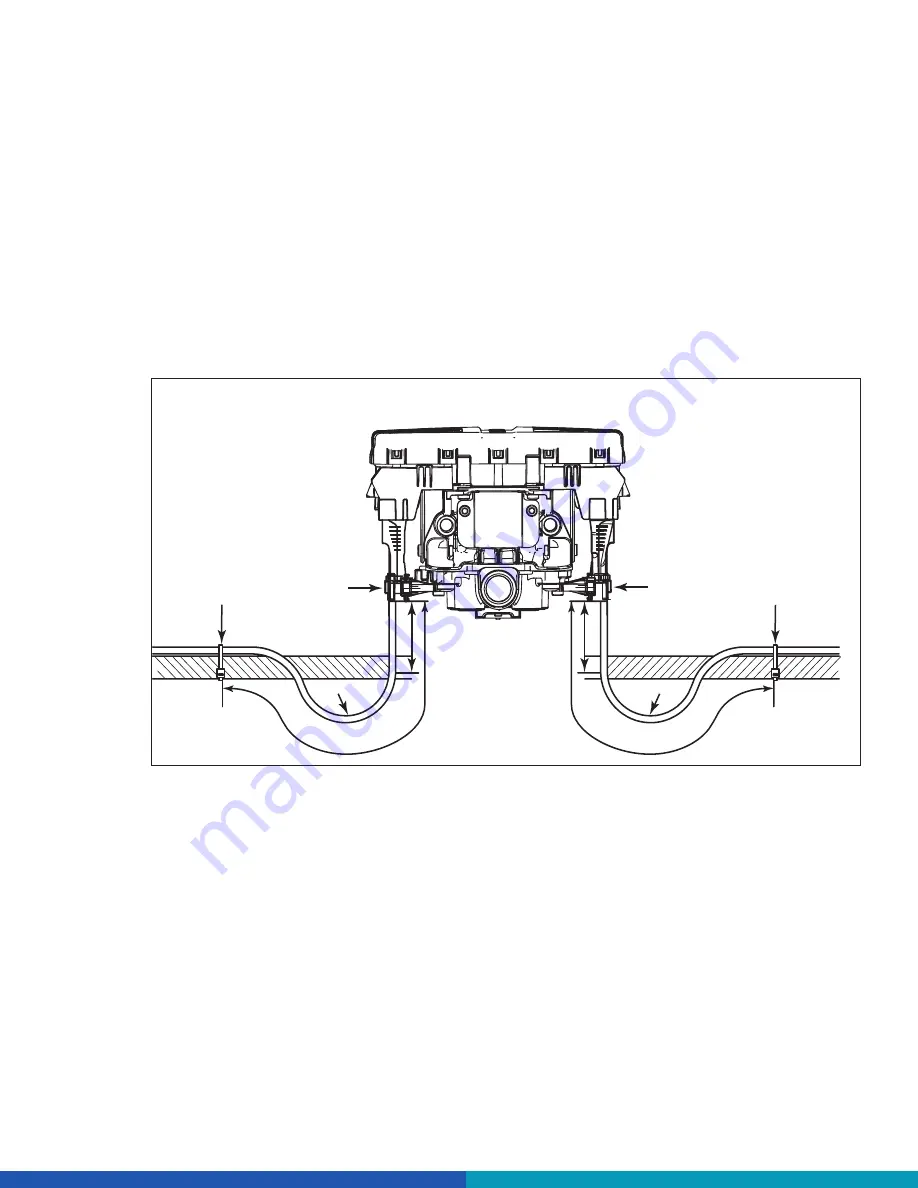
30
Appendix II
7.2.1
Strain Relief at the ECU — Bracket Mounting
WABCO recommends that cable connections to a component, such as an ECU valve assembly, display
a visible amount of slack in the cable up to the first tie or clip that secures the cable to the trailer structure
or air line. This first anchor point should be a minimum 6-inches (152 mm) of cable length from the cable/
component connection and maximum of 12-inches (305 mm). This applies to all sensor, power, valve and
GIO cables. Regardless of whether zip ties or cable clips are used, cables should be secured at intervals
not greater than 18-inches (457 mm) to avoid cable vibration.
Ideally, cables should be affixed to the rigid structure of the trailer. A good rule of thumb is to have the bend
of the cable, also known as bend radius, be greater than or equal to ten times the diameter of the cable. If
the cable is 1/4-inch (6.35 mm) in diameter, then the bend should be a minimum of 2-1/2-inches (64 mm).
Refer to figure for the ECU mounting of 2S/1M ABS.
4"
Max.
12"
R
4"
Max.
12"
R
≥
10 x D
R
FASTENER
FASTENER
ZIP TIE
ZIP TIE
Bend radius (R) equal to
or greater than 10 times
cable diameter (D).
R
≥
10 x D
First fastener must be
a minimum 6 inches (152 mm)
and a maximum of 12-inches
(305 mm) from connector.
BRACKET MOUNTING - ECU REAR VIEW
4017108a
ABS 2S/1M