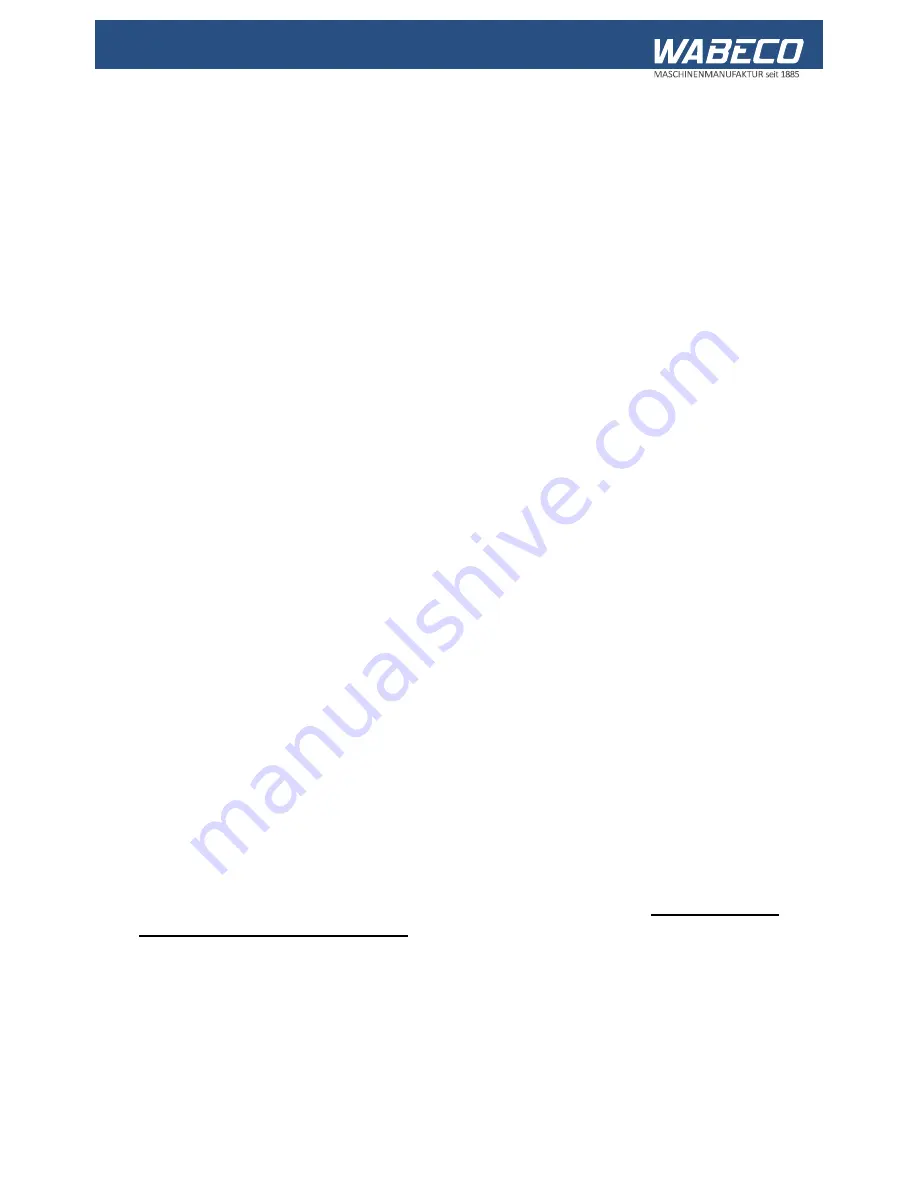
17
3.
Putting into operation
3.1
For all lathes
■
Use a dry cloth to remove the corrosion protection that was applied to all exposed parts for
transport
■
In the event of marine impregnation of exposed parts, it is recommended you spray them with oil,
allow it to work, and then remove the impregnation with a dry cloth
■
Once set up properly (see the section on delivery and set up) connect the grounded plug directly
to a safety socket and the 230 V 50/60 Hz (optional 110 V 60 Hz) mains power supply
■
Provision of sufficient coolant for the operation of a coolant system (optional)
■
Release the axis clamps and check the individual feed spindles for easy operation
■
Check all electronic operating elements, for example, ON/OFF switch, emergency off switch,
potentiometer, bush protection hood, etc. for functionality
3.2
For CNC lathes
■
When putting CNC machines into operation for the first time, always read the start-up manual
3.2.1 Setting up and connecting the control computer
When selecting a suitable control computer, pay attention to the system prerequisites of the
control software. These are listed on the rear of the CD case sent with the machine.
Follow the instructions in the start manual of the software to install the control software on the
computer. The start manual can be found in the CD case of the control software included with the
machine.
In the next step, the software must be adapted to your machine. To do this, follow the instructions sent
with the machine which detail the editing of the parameters.
When the software has been successfully installed on the control computer and all parameters have
been adapted successfully, the control computer must be connected with the machine controller.
The machine controller communicates with the computer via the serial interface (COM port). In order
to establish a connection between the machine controller and the computer, connect the end of the
interface cable that is on the machine console to the COM port of the computer.
CAUTION:
The axis cable of the multiphase motors and the serial interface cable may only be plugged or
unplugged with the control switched off. Otherwise damages to the control, the machine or the
control computer may occur!
Summary of Contents for D6000
Page 76: ...76 18 Drawings and legends 18 3 Protective hood drive 2 0 kW motor...
Page 78: ...78 18 Drawings and legends 18 4 Electronic console 2 0 kW motor...
Page 86: ...86 18 Drawings and legends 18 10 Bed with lead screw with trapezoidal threaded spindle...
Page 90: ...90 18 Drawings and legends 18 11 Bed with lead screw with ball screw spindle...
Page 94: ...94 18 Drawings and legends 18 13 Tool skid Transverse skid...
Page 96: ...96 18 Drawings and legends 18 14 Tool skid Lock plate...
Page 98: ...98 18 Drawings and legends 18 15 Tool skid Longitudinal skid...
Page 100: ...100 18 Drawings and legends 18 16 Transverse skid with lock plate with ball screw spindle...
Page 102: ...102 18 Drawings and legends 18 17 Tailstock...
Page 104: ...104 18 Drawings and legends 18 18 Motor for control of the x axis...
Page 106: ...106 18 Drawings and legends 18 19 Motor for control of the z axis...
Page 108: ...108 18 Drawings and legends 18 20 Operating console for 1 4 kW motor...
Page 110: ...110 18 Drawings and legends 18 20 Operating console for 1 4 kW motor...
Page 112: ...112 18 Drawings and legends 18 21 Operating console for 2 0 kW motor...
Page 114: ...114 18 Drawings and legends 18 21 Operating console for 2 0 kW motor...
Page 116: ...116 18 Drawings and legends 18 22 Bracket arm for operating console...
Page 118: ...118 18 Drawings and legends 18 23 Industrial screen and membrane keyboard...
Page 138: ...138 19 Circuit diagram 19 9 Multiphase motor with end stop...
Page 154: ...154 23 Safety cabin optional 23 8 Drawing and legend...
Page 163: ...163 26 Tensioning bracket with milling machine table optional 26 7 Drawing and legend...