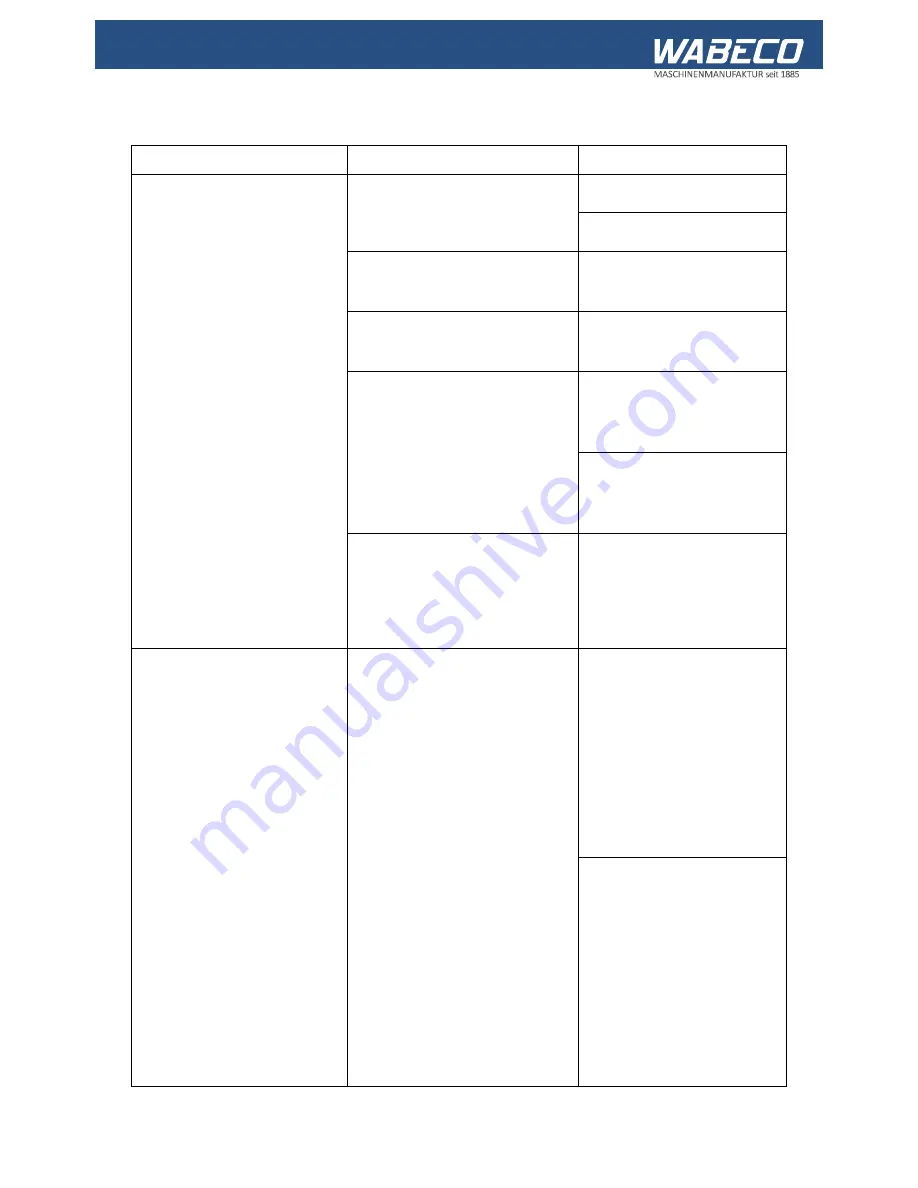
55
16. Operational faults and the elimination of such
Operational faults
Possible cause
Remedy
Machine cannot be switched on
230V voltage is not present
Plug is not fitted correctly
Check the fuse for the socket
The chuck protection hood is not
closed
Close the chuck protection
hood
Emergency off switch not
unlocked
Unlock the emergency off
switch
Direction of rotation has not been
selected
For machines with 1.4 kW
Select the direction of rotation
at the turn switch
For machines with 2.0 kW
Select using the 3 setting
switch
Vibrations (e.g. by transportation)
have caused the plugged contacts
of the drive motor (1.4 kW) board
to come undone
Pull the power plug!
Remove the cover sheet of the
electronic housing and check
all plugged contacts.
Main spindle motor no longer
starts after the unlocking of the
emergency off switch
Motor controller must be unlocked
For machines with a 1.4 kW
drive motor, the motor must be
switched on again using the
ON/OFF switch after the
emergency off switch is
unlocked. After unlocking, wait
approximately 5 seconds
before switching the machine
on.
For machines with a 2.0 kW
drive motor, the 3 setting
switch must first be set to
STOP after the emergency off
switch is unlocked. In this
position, wait approximately 5
seconds before switching the
machine on. After this, the
motor may be switched on as
usual.
Summary of Contents for D6000
Page 76: ...76 18 Drawings and legends 18 3 Protective hood drive 2 0 kW motor...
Page 78: ...78 18 Drawings and legends 18 4 Electronic console 2 0 kW motor...
Page 86: ...86 18 Drawings and legends 18 10 Bed with lead screw with trapezoidal threaded spindle...
Page 90: ...90 18 Drawings and legends 18 11 Bed with lead screw with ball screw spindle...
Page 94: ...94 18 Drawings and legends 18 13 Tool skid Transverse skid...
Page 96: ...96 18 Drawings and legends 18 14 Tool skid Lock plate...
Page 98: ...98 18 Drawings and legends 18 15 Tool skid Longitudinal skid...
Page 100: ...100 18 Drawings and legends 18 16 Transverse skid with lock plate with ball screw spindle...
Page 102: ...102 18 Drawings and legends 18 17 Tailstock...
Page 104: ...104 18 Drawings and legends 18 18 Motor for control of the x axis...
Page 106: ...106 18 Drawings and legends 18 19 Motor for control of the z axis...
Page 108: ...108 18 Drawings and legends 18 20 Operating console for 1 4 kW motor...
Page 110: ...110 18 Drawings and legends 18 20 Operating console for 1 4 kW motor...
Page 112: ...112 18 Drawings and legends 18 21 Operating console for 2 0 kW motor...
Page 114: ...114 18 Drawings and legends 18 21 Operating console for 2 0 kW motor...
Page 116: ...116 18 Drawings and legends 18 22 Bracket arm for operating console...
Page 118: ...118 18 Drawings and legends 18 23 Industrial screen and membrane keyboard...
Page 138: ...138 19 Circuit diagram 19 9 Multiphase motor with end stop...
Page 154: ...154 23 Safety cabin optional 23 8 Drawing and legend...
Page 163: ...163 26 Tensioning bracket with milling machine table optional 26 7 Drawing and legend...