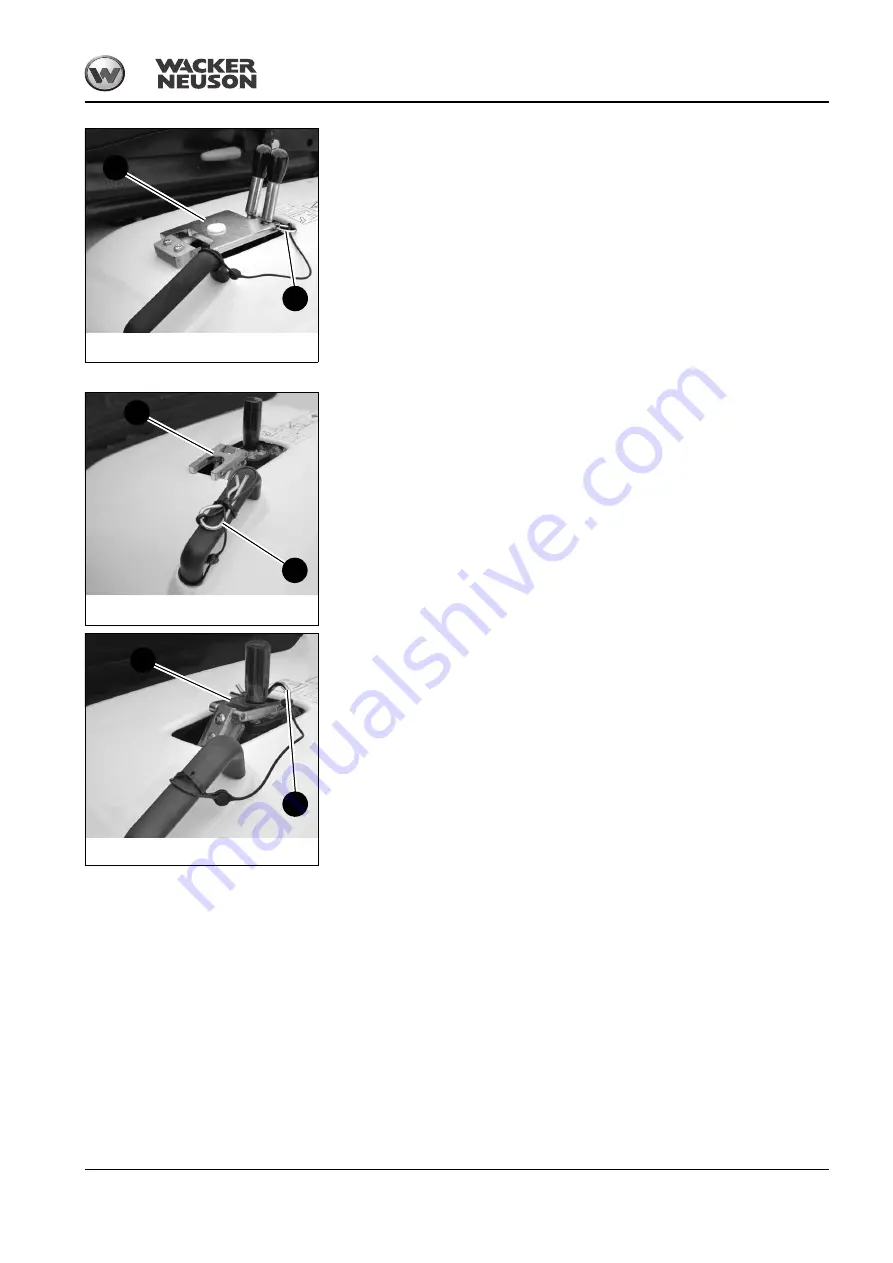
BA 1001/1501/2001 us – Edition 3.3 * 12001b330.fm
3-39
Operation
Fasten control lever lock
A
with split pin
B
.
Locking the control levers (2001)
Fold back control lever lock
A
.
Fasten control lever lock
A
with split pin
B
.
Fig. 63: Locking the control levers (1001/1501)
B
A
Fig. 64: Locking the control levers (2001)
B
A
Fig. 65: Locking the control levers (2001)
B
A