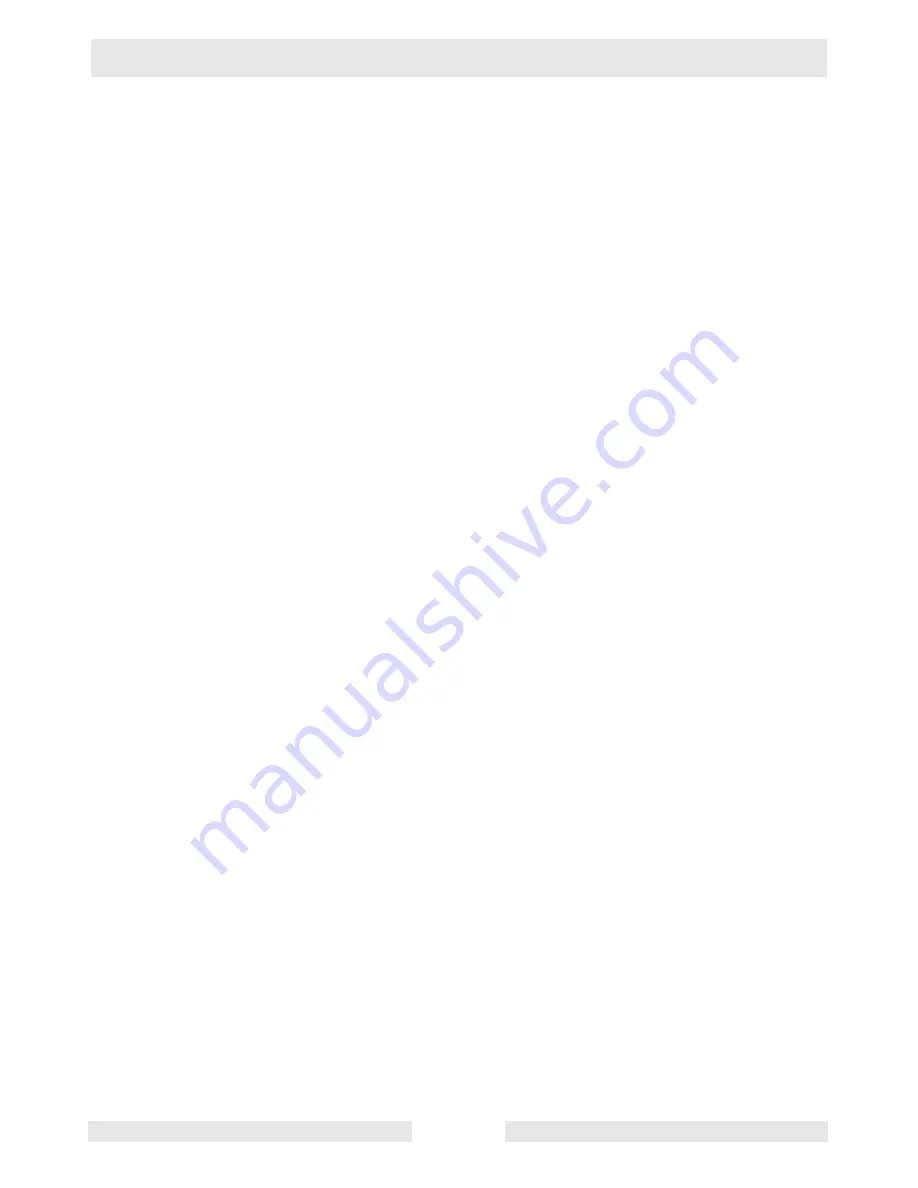
Maintenance
BS 65-V
wc_tx000923gb.fm
34
5.3
Lubrication
See Graphic: wc_gr005326
Ramming system
Check oil level:
5.3.1
Tilt the machine backwards approximately 15° until the engine is level
by placing a wedge under the shoe.
5.3.2
Check the oil level through oil sightglass (d). Proper ramming system
lubrication is indicated when approximately 1/2–3/4 of the sightglass is
full.
5.3.3
If the oil is not visible, oil must be added through the sightglass port.
Tilt rammer forward and remove sightglass (d). See Technical Data
for oil quantity and type.
5.3.4
Wrap the sightglass threads with teflon tape. Install the sightglass (d).
Torque to 9 Nm.
5.3.5
Note: After transporting the rammer horizontally, upright the rammer
and allow the oil to drain back through the engine. It may take up to 45
minutes for the oil level to recover.
Oil change:
5.3.6
Unscrew the oil drain plug (e) located below the oil sightglass.
5.3.7
Tip the rammer back until it is resting on its handle and allow oil to
drain.
Note: In the interests of environmental protection, place a plastic sheet
and a container under the machine to collect any liquid which drains
off. Dispose of this liquid in accordance with environmental protection
legislation.
5.3.8
Screw in the oil drain plug (e). Torque to 54 Nm.
5.3.9
Remove sightglass (d) and fill with oil. See Technical Data for oil
quantity and type. Wrap the sightglass threads with teflon tape. Install
the sightglass (d). Torque to 9 Nm.
Summary of Contents for BS 65-V
Page 1: ...Rammer BS 65 V OPERATOR S MANUAL 0176651en 001 0808 0 1 7 6 6 5 1 E N...
Page 2: ......
Page 18: ...Safety Information BS 65 V wc_si000275gb fm 18 3 5 Label Locations wc_gr005418 C P N O M...
Page 29: ...BS 65 V Operation wc_tx000918gb fm 29 Notes...
Page 35: ...BS 65 V Maintenance wc_tx000923gb fm 35 wc_gr005326...