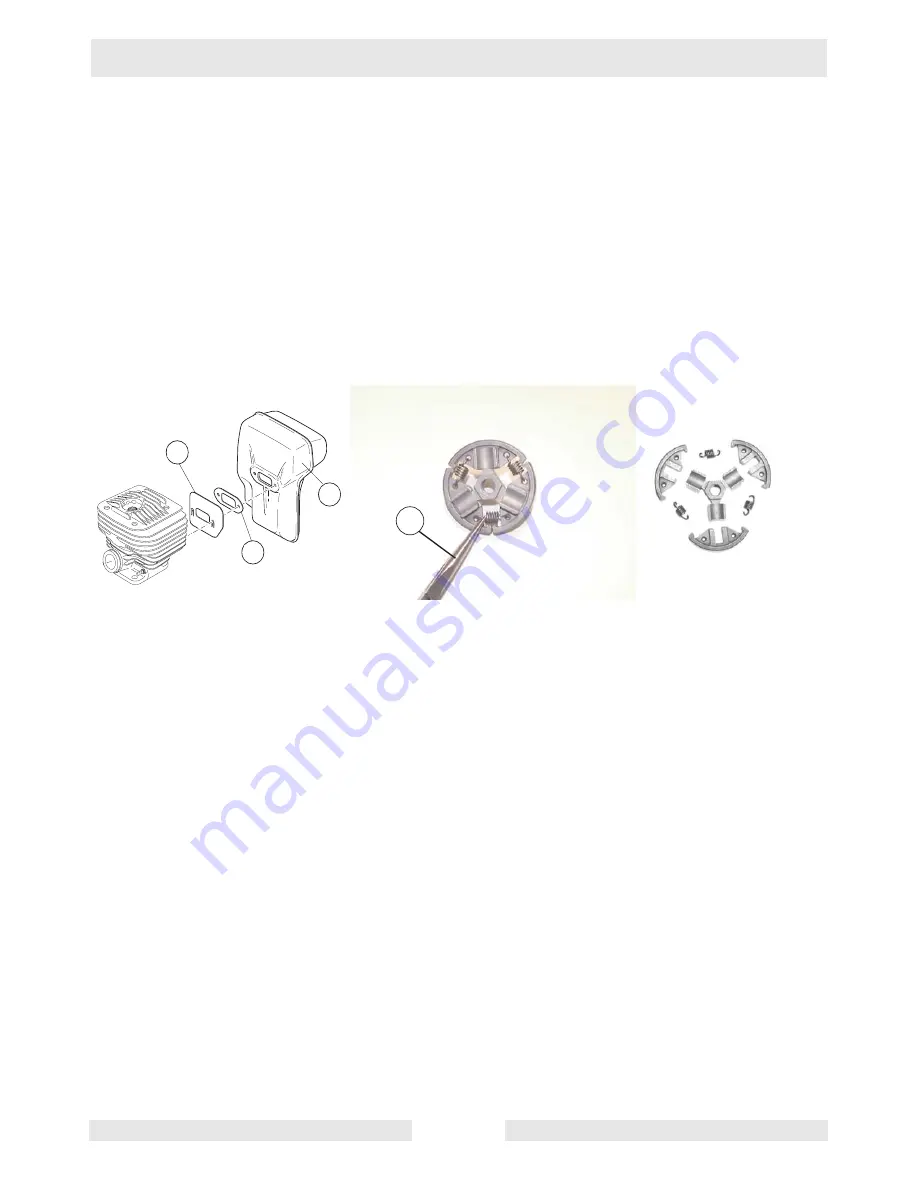
Clutch
BTS Repair
wc_tx000298gb.fm
8
3.2
Mounting muffler and heat plate
See Graphic: wc_gr001386
When mounting the muffler (10) ensure that the heat plate (12) is
installed correctly.
Note: The heat plate goes directly onto the cylinder, then the gasket
(13) and muffler.
3.3
Repairing the clutch
See Graphic: wc_gr001386
3.3.1
The tension springs of the clutch can be removed/ replaced with
pointed pliers (b). If spares are required, the 3 tension springs are only
available as individual parts.
3.3.2
The tension springs should only be replaced as a set if replacement is
required.
3.3.3
If the hub / flyweight is defective, the complete clutch must be
replaced.
wc_gr001386
b
1
12
12
1
13
1
1
10
10
Summary of Contents for BTS 930-8340
Page 2: ......
Page 6: ...Table of Contents BTS Repair wc_br0118754enTOC fm 4...
Page 38: ...Torques BTS Repair wc_tx000327gb fm 36...
Page 43: ......