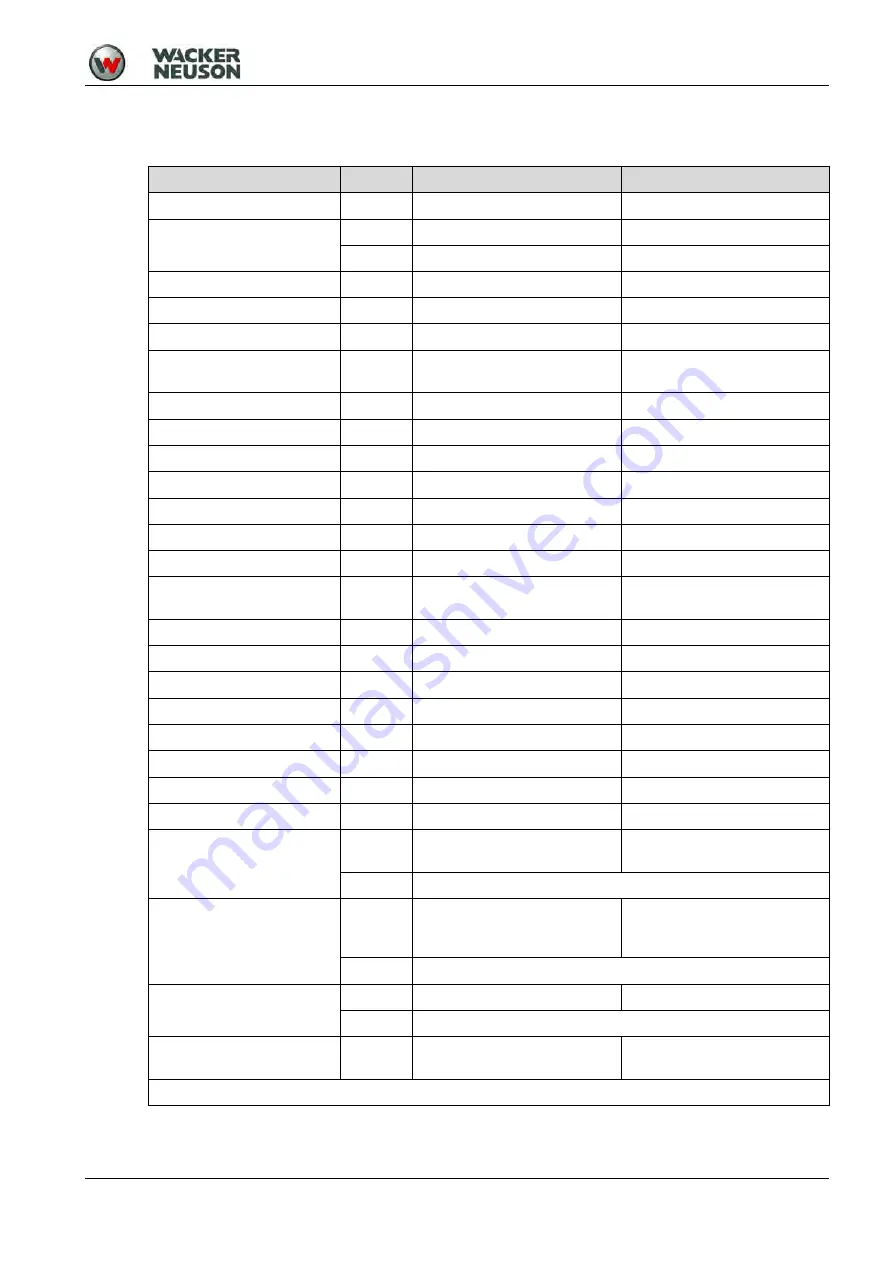
13 Technical data
100_0202_td_0018.fm
63
13 Technical data
13.1
DPU80
Designation
Unit
DPU80Le670
DPU80Le770
Centrifugal force
kN
80
80
Oscillations
Hz
56
56
1/min
3,380
3,380
Compaction performance
m
2
/h
1,166
1,340
Travel speed*
m/min
29
29
Gradeability
%
34
34
Length (center pole in working
position)
mm
2,409
2,409
Width
mm
670
770
Height
mm
1,541
1,541
Operating weight
kg
756
771
Ground clearance
mm
830
830
Electrical load rating
kW
11.0
11.0
Nominal speed
1/min
3,000
3,000
Working pressure of hydraulics
bar
165
165
Maximum allowable hydraulic
pressure
bar
230
230
Coolant volume
l
3.8
3.8
Type of coolant
SAE J1034: water (1:1)
SAE J1034: water (1:1)
Exciter oil volume
l
1.35
1.35
Exciter oil type
M 75W90
M 75W90
Hydraulic oil volume
l
17.7
17.7
Type of hydraulic oil
MR 520
MR 520
Storage temperature range
°C
-20 – +50
-20 – +50
Operating temperature range
°C
-10 – +50
-10 – +50
Sound pressure level
At location of operation L
pA
dB(A)
92
92
Standards
EN 500-4
Sound power level L
wa
measured
guaranteed
dB(A)
108
109
108
109
Standards
EN 500-4, 2000/14/EG
Vibration total value a
hv
m/s
2
< 2.5
< 2.5
Standards
EN 500-4
Uncertainty of measurement of
the vibration total value a
hv
m/s
2
0.5
0.5
*
Depending on the soil properties.
Summary of Contents for DPU80 Series
Page 74: ......