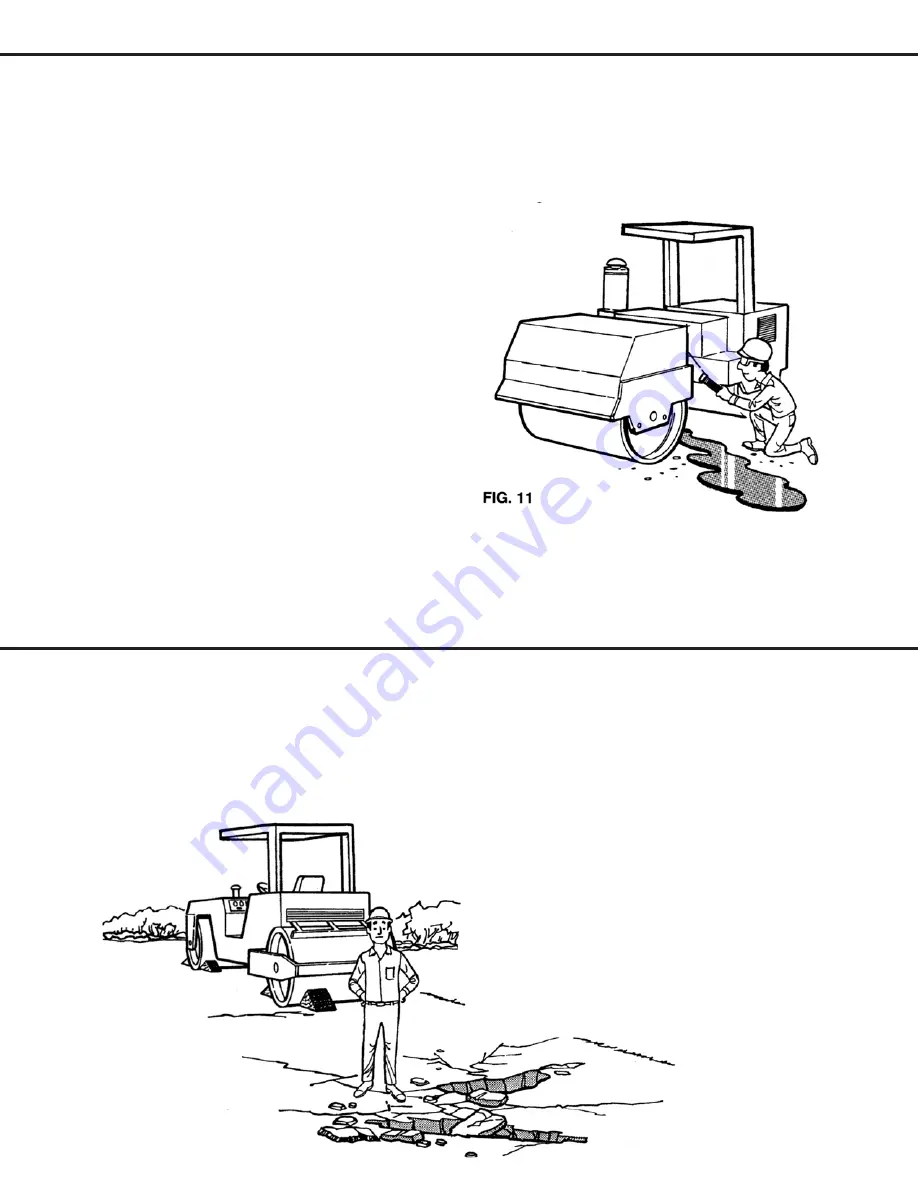
Before starting, carefully inspect your machine for
any evidence of physical damage such as cracking,
bending or deformation of plates or welds. Check for
cracking or flaking of paint, which may indicate an
excessive strain or dangerous crack in the material
below. Check for loose, broken or missing parts such
as Roll-Over Protective Structure (ROPS) support
brackets, vibration isolators, and nuts and bolts. If
potentially serious problems are found, do not
operate the machine until appropriate repairs are
completed.
Check the level of all fluids … brake, transmission,
power steering, engine coolant, hydraulic system and
others. Fill low reservoirs only to the proper level.
Check the various systems (hydraulic, cooling, etc.)
for leaks. (FIG. 11) Inspect all plugs, filler caps and
fittings for tell-tale signs of leaks. ALWAYS use a
flashlight or shielded trouble light when checking …
NEVER an open flame. Repair any leaks, or have
them repaired by authorized service personnel. (See
pages 30 through 44 for additional service cautions.)
Check the fuel level and, if low, fill the tank with the
proper grade of clean fuel before extended operation
(following the instructions on page 36).
A stalled or faltering engine can result in a real
hazard when operating on grades, in traffic or in
heavily congested areas.
NEVER smoke when checking fuel level or refueling.
13
PREPARE FOR SAFE OPERATION
BE SURE THE WORK AREA IS SAFE
Before beginning operation, thoroughly check
the area for any unusual conditions that could
be dangerous. (FIG. 12) Check for hidden holes,
drop-offs or overhead obstacles that could be
dangerous. Check the clearance under overhead
power and phone lines. LOOK UP AS WELL AS
DOWN.
Be observant of other workmen, bystanders and
other machines in the area. Be especially careful if
trenches, lightpoles, tiles, buildings, etc. are within
the effective range of a vibratory compactor.
IMPROPER OPERATION COULD RESULT IN
DAMAGE OR INJURY.
Remember, the danger of sliding and/or tipping on
steep slopes is always present … regardless of
how heavy or “stable” your machine may appear to
be. When operating under these conditions, the
use of ROPS and seat belts reduces the hazard to
operating personnel.
14
PREPARE FOR SAFE OPERATION
FIG. 12
Summary of Contents for RD 27-100
Page 1: ...Operator s Manual Roller RD 27 100 RD 27 120 0171754en 003 1109 0 1 7 1 7 5 4 E N...
Page 8: ...Table of Contents RD 27 8 wc_bo0171754en_003TOC fm...
Page 49: ...RD 27 Operation wc_tx000814gb fm 49 Notes...
Page 56: ...Maintenance RD 27 56 wc_tx000815gb fm Seat assembly diagram wc_gr007044...
Page 58: ...Maintenance RD 27 58 wc_tx000815gb fm Seat switch diagram wc_gr007045...
Page 100: ...Schematics RD 27 100 wc_tx000863gb fm 6 Schematics 6 1 Electrical Schematic...
Page 101: ...Schematics RD 27 wc_tx000863gb_1 fm Electrical Schematic Page 1 of 3 101...
Page 102: ...wc_tx000863gb_1 fm RD 27 Schematics Electrical Schematic Page 2 of 3 102...
Page 103: ...Schematics RD 27 wc_tx000863gb_1 fm Electrical Schematic Page 3 of 3 103...
Page 104: ...Schematics RD 27 104 wc_tx000863gb fm Notes...
Page 105: ...RD 27 Schematics wc_tx000863gb fm 105 Notes...
Page 106: ...Schematics RD 27 106 wc_tx000863gb fm 6 2 Hydraulic Schematic...
Page 109: ...RD 27 Schematics wc_tx000863gb fm 109 Notes...
Page 114: ......
Page 141: ......
Page 142: ...FORM RC 0809 Printed in U S A...