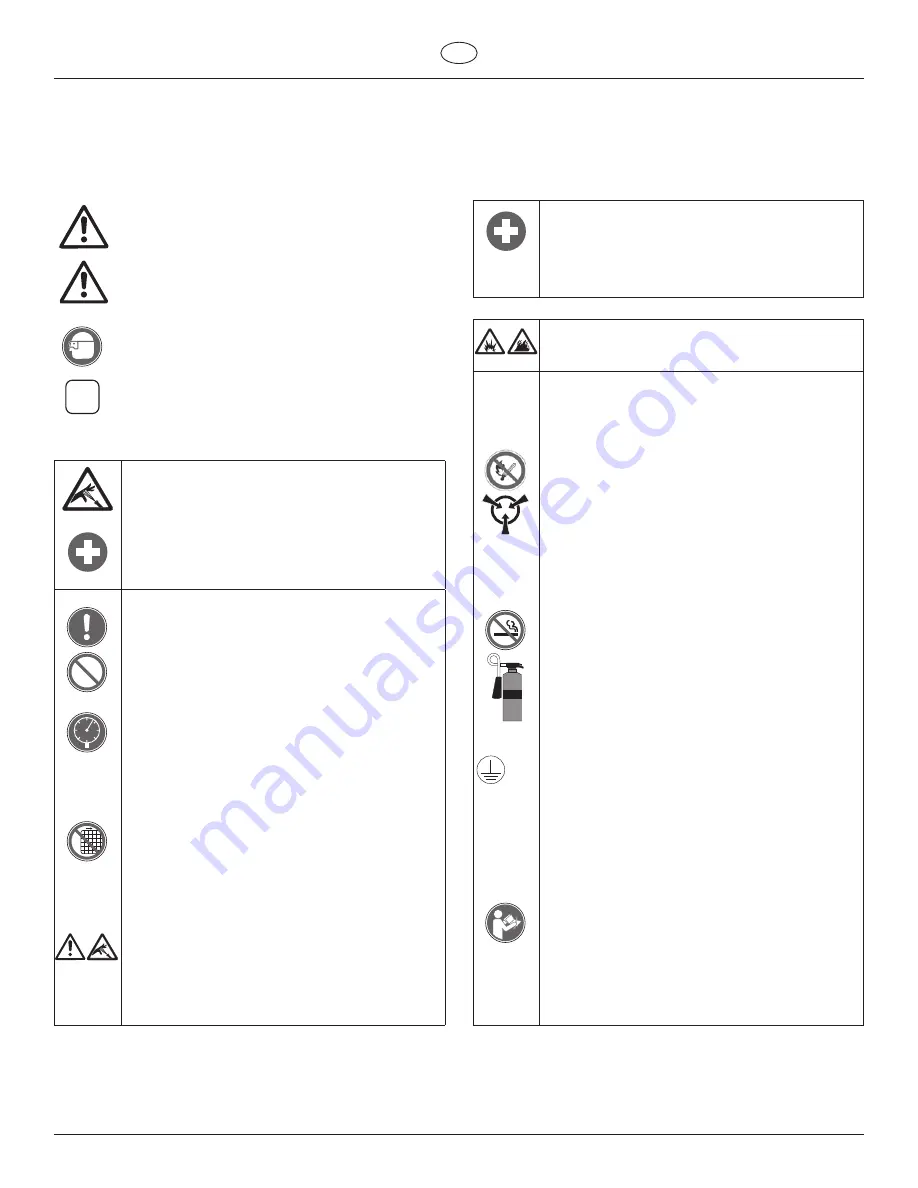
4
ProSpray 3.21
GB
Safety Regulations
1.
Safety regulations for Airless
spraying
This manual contains information that must be read and understood
before using the equipment. When you come to an area that has one of
the following symbols, pay particular attention and make certain to heed
the safeguard.
This symbol indicates a potential hazard that may cause
serious injury or loss of life. Important safety information
will follow.
Attention
This symbol indicates a potential hazard to you or to the
equipment. Important information that tells how to
prevent damage to the equipment or how to avoid
causes of minor injuries will follow.
A hazard symbol such as this one refers to a specific,
task-related risk. Be sure to heed the safeguard.
i
Notes give important information which should be given
special attention.
HAZARD: INjeCTION INjuRy
A high pressure stream produced by this equipment
can pierce the skin and underlying tissues, leading to
serious injury and possible amputation.
DO NOT TReAT AN INjeCTION INjuRy AS A
SIMPLe CuT! Injection can lead to amputation. See a
physician immediately.
The maximum operating range of the unit is 221 bar
(22.1 MPa, 3200 PSI) fluid pressure.
PReVeNTION:
• NEVER aim the gun at any part of the body.
• NEVER allow any part of the body to touch the fluid
stream. DO NOT allow body to touch a leak in the fluid
hose.
• NEVER put your hand in front of the gun. Gloves will
not provide protection against an injection injury.
• ALWAYS lock the gun trigger, shut the fluid pump off
and release all pressure before servicing, cleaning
the tip guard, changing tips, or leaving unattended.
Pressure will not be released by turning off the engine.
The PRIME/SPRAY valve or pressure bleed valve
must be turned to their appropriate positions to relieve
system pressure.
• ALWAYS keep tip guard in place while spraying. The
tip guard provides some protection but is mainly a
warning device.
• NEVER use a spray gun without a working trigger lock
and trigger guard in place.
• ALWAYS remove the spray tip before flushing or
cleaning the system.
• The paint hose can develop leaks from wear, kinking
and abuse. A leak can inject material into the skin.
Inspect the hose before each use.
• All accessories must be rated at or above the
maximum operating pressure range of the sprayer.
This includes spray tips, guns, extensions, and hose.
NOTe TO PHySICIAN:
Injection into the skin is a traumatic injury. It is
important to treat the injury as soon as possible. DO
NOT delay treatment to research toxicity. Toxicity is a
concern with some coatings injected directly into the
blood stream. Consultation with a plastic surgeon or
reconstructive hand surgeon may be advisable.
HAZARD: eXPLOSION OR FIRe
Solvent and paint fumes can explode or ignite. Severe
injury and/or property damage can occur.
PReVeNTION
:
• Provide extensive exhaust and fresh air introduction
to keep the air within the spray area free from
accumulation of flammable vapors.
• Avoid all ignition sources such as static electricity
sparks, electrical appliances, flames, pilot lights, hot
objects, and sparks from connecting and disconnecting
power cords or working light switches.
• Plastic can cause static sparks. Never hang plastic
to enclose spray area. Do not use plastic drop cloths
when spraying flammable materials.
• Always flush unit into separate metal container, at low
pump pressure, with spray tip removed. Hold gun
firmly against side of container to ground container and
prevent static sparks.
• Do not smoke in spray area.
• Fire extinguisher must be present and in good working
order.
• Place sprayer at least 6.1 m (20 feet) from the spray
object in a well ventilated area (add more hose if
necessary). Flammable vapors are often heavier than
air. Floor area must be extremely well ventilated. The
pump contains arcing parts that emit sparks and can
ignite vapors.
• The equipment and objects in and around the spray
area must be properly grounded to prevent static
sparks.
• Use only conductive or earthed high pressure fluid
hose. Gun must be earthed through hose connections.
• Power cord must be connected to a grounded circuit
(electric units only).
• The unit must be connected to an earthed object. Use
the green earthing wire to connect the unit to a water
pipe, steel beam, or other electrically earthed surface.
• Follow material and solvent manufacturer’s warnings
and instructions. Be familiar with the coating material’s
MSDS sheet and technical information to ensure safe
use.
• Do not use materials with a flashpoint below 21° C
(70° F). Flashpoint is the temperature at which a fluid
can produce enough vapors to ignite.
• Use lowest possible pressure to flush equipment.
PE
0 bar