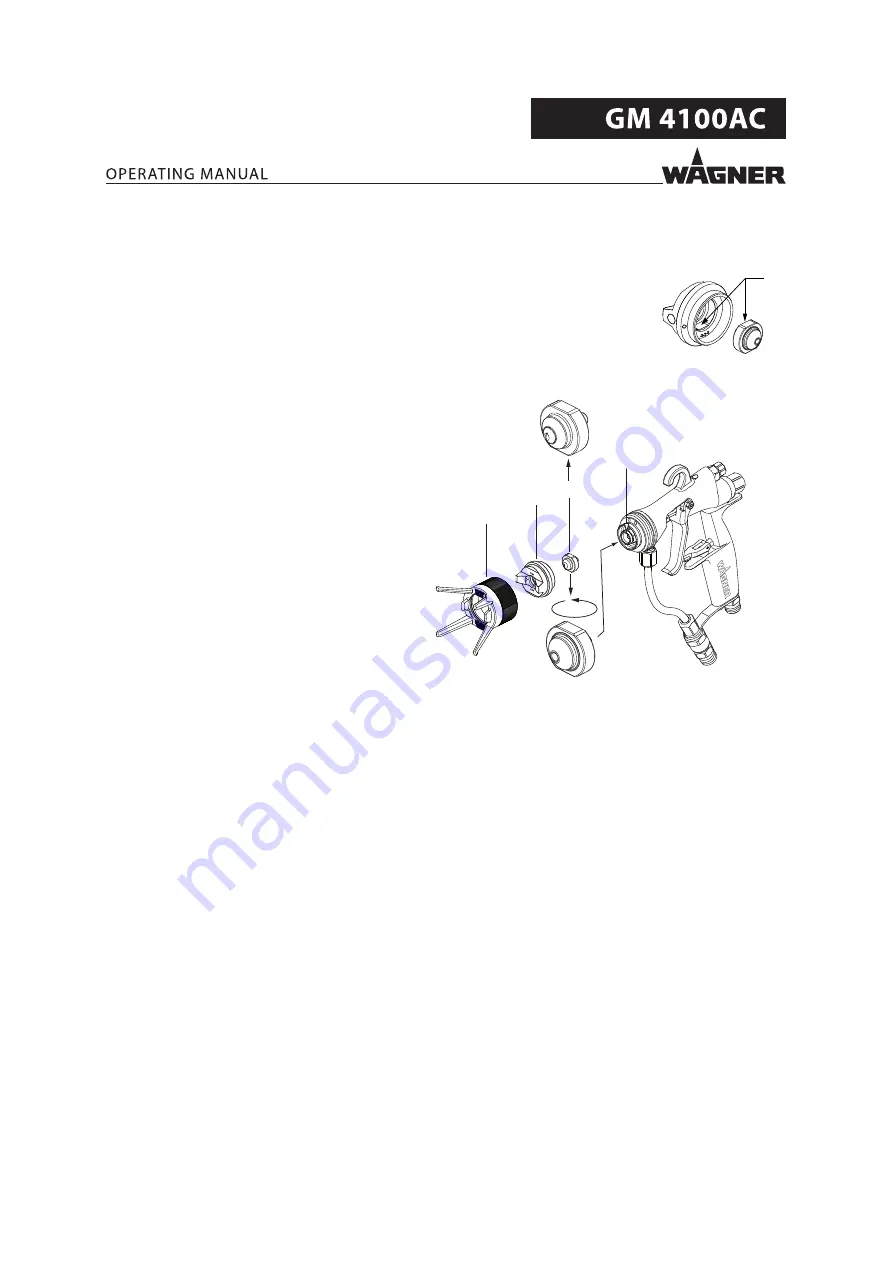
26
VERSION 01/2018
ORDER NUMBER DOC 394821
7.4.2 ELIMINATING NOZZLE CLOGGING
1. Relieve the pressure of the spray gun and
device.
B_02261
x
B_02264
A
B
C
D
Nozzle in cleaning position
Nozzle in spray position
2. Secure the spray gun with the trigger locking
device.
3. Unscrew the union nut with nozzle guard (A).
4. Remove air cap (B).
5. Push AirCoat nozzle (C) manually out of
the air cap (B), reverse it and put it onto the
nozzle seal (D) with nozzle tip facing towards
the rear.
6. Refit air cap (B) on nozzle (C). Note the
flattened parts (X) on the nozzle and in the
air cap.
7. Screw the union nut with nozzle guard (A)
over the air cap (B) onto the spray gun and
tighten by hand.
8. Switch the product pressure back on.
9. Turn the locking device to the spraying
position and briefly pull trigger.
10. When the blockage has been flushed out,
secure the spray gun with the trigger locking
device.
11. Relieve the pressure of the spray gun and
device.
12. Unscrew the union nut with nozzle guard (A).
13. Remove air cap (B) and push AirCoat nozzle
(C) out by hand.
Clean the nozzle and put it back on nozzle
seal (D) in the spray position.
14. Refit air cap (B) on nozzle (C). Note the
flattened parts (X) on the nozzle and in the
air cap.
15. Screw the union nut with nozzle guard (A)
over the air cap (B) onto the spray gun and
tighten by hand.
16. Switch the product pressure and the air
supply pressure back on.
Summary of Contents for AirCoat GM 4100 AC
Page 1: ...B_02254 GM 4100 AC AirCoat Manual Gun for Flat and Round Jet Nozzles Version 01 2018...
Page 2: ......
Page 49: ......
Page 50: ......
Page 51: ......