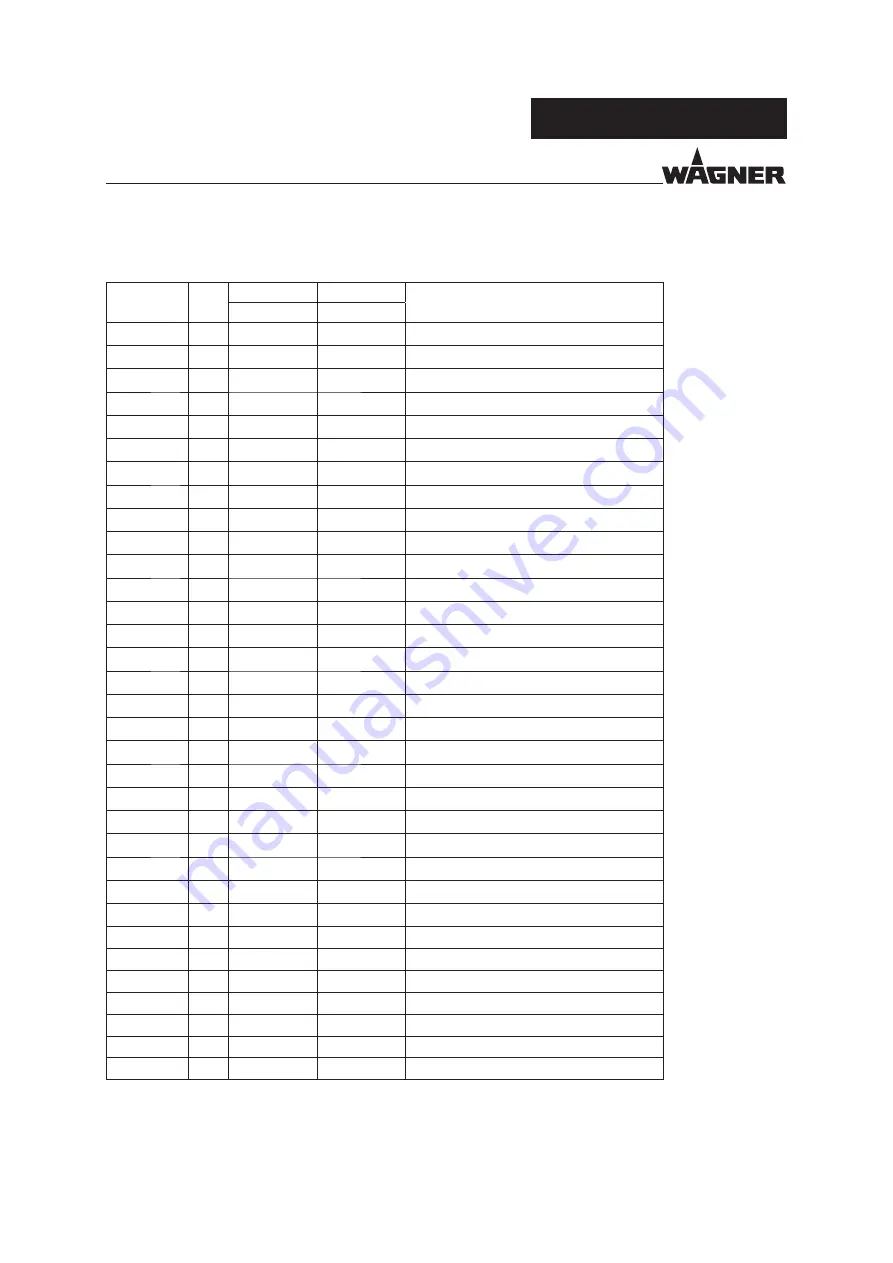
39
GM 4600AC
OPERATING MANUAL
EDITION 05/2011
Part No. DOC394861
10.2
SPARE PARTS LIST GM 4600AC
Spare parts list GM 4600AC
Pos
K
Qty
16 MPa
25 MPa
Description
Part No.
Part No.
1
1
394004
3940014
GM 4600AC; XX MPa; NPSM1/4“
2
1
9999501
9999501
Screw spring Material
3
1
9999500
9999500
Screw spring Air
4
1
394256
394256
Tension sleeve compl.
5
1
394335
-
Spring cap 16 MPa; 160 bar: 2320 psi
5
1
-
394333
Spring cap 25 MPa; 250 bar: 3625 psi
6
1
394924
394924
Air tappet assy.
8
◆
1
2311320
2311320
Valve rod unit assy.
10
1
394327
394327
Sealing screw
11
✭ ◆
1
394328
394328
Sealing collar
12
✭ ◆
1
9971445
9971445
O-ring
13
◆ ●
1
379xxx
379xxx
AC nozzle (see chapter 9.2)
14
✭ ◆
1
394339
394339
Sealing ring
15
✭ ◆
1
9974245
9974245
O-ring
16
✭ ◆
1
394922
394922
Valve seat compl.
17
✭ ◆
1
394338
394338
Nozzle seal
18
1
394330
394330
Chuck
19
1
394257
394257
Valve tappet compl.
20
1
394318
394318
Nut
21
1
394601
394601
Trigger
22
1
394319
394319
Screw
23
1
394334
394334
Safety catch
24
1
9935088
9935088
Cylindrical shaft
34
✭ ◆
1
394920
394920
Valve rod compl.
35
✭ ◆
1
394323
394323
Valve rod seal
36
◆ ●
1
2313494
2313494
Air cap LV complete (red)
36
◆ ●
1
2313497
2313497
Air cap HV complete (blue)
36
◆ ●
1
2313498
2313498
Air cap LA plus (bronze)
50
1
394309
394309
Valve tappet
51
✭ ◆
1
179338
179338
Air valve seal
52
✭ ◆
1
179395
179395
Seal
53
✭ ◆
1
394322
394322
Cap
55
●
1
394336
394336
Nozzle body
◆
= Wearing part
✭
= Included in service set
●
= Not part of standard equipment for spray gun. Available, however, as additional
extra
Summary of Contents for AirCoat GM 4600AC-H
Page 2: ......
Page 45: ...45 GM 4600AC 45 GM 4600AC OPERATING MANUAL EDITION 05 2011 Part No DOC394861...
Page 47: ......