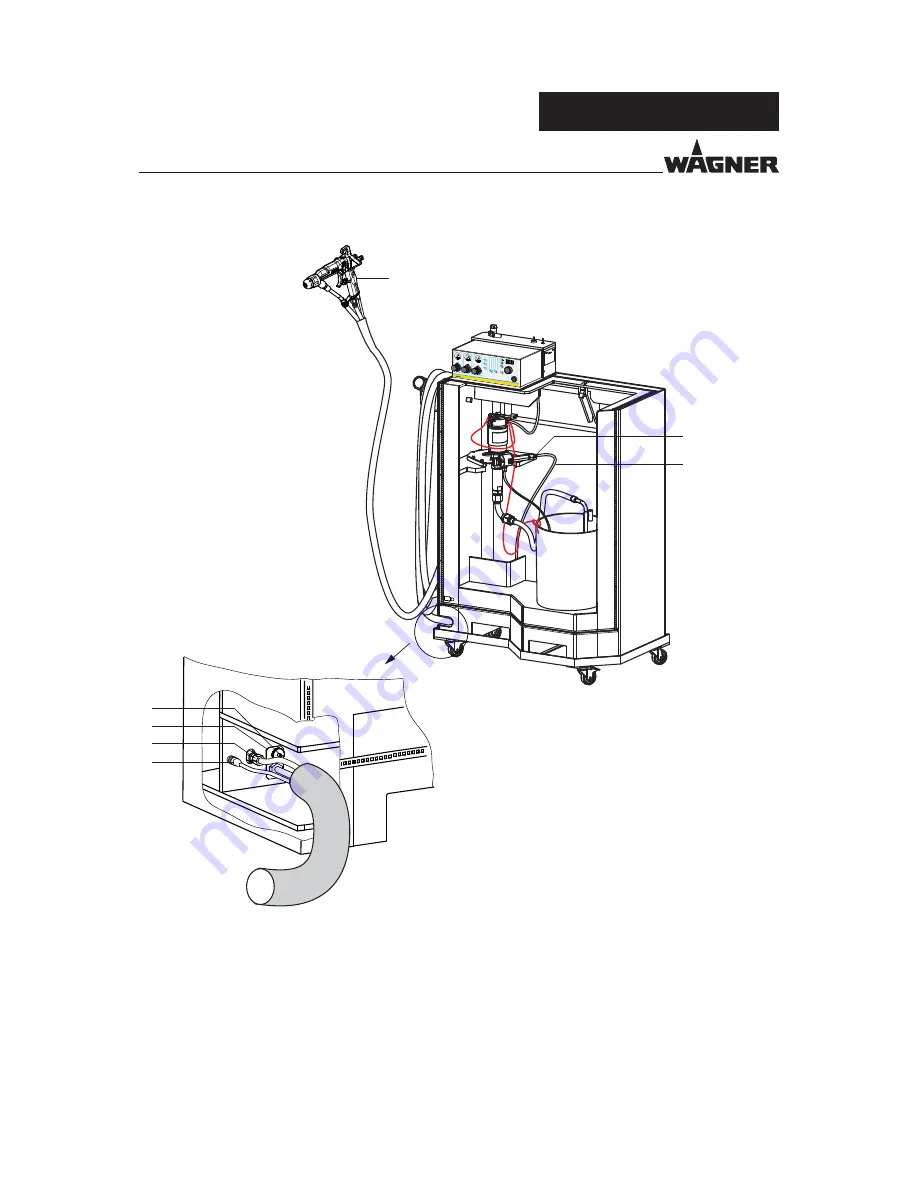
79
AquaCoat GM 5000EACW
AquaCoat
100
80
60
40
20
80
60
40
20
10
R3
R2
R1
Zerstäuberluft
Atomizing air
Mat. Druckre
gler
Mat. pressure reg.
Pumpe
Pump
POWER
0
1
μA
kV
1
5
2
3
4
3
6
B_03545
OPERATING MANUAL
EDITION 04/2012
PART NO. DOC2321362
8.4
REPLACING THE SPRAY GUN INCLUDING HOSE SET
Disassembling gun assy. (1)
1. Loosen the union nut (6) on the bared part of the material hose (3) with a universal
spanner.
2. Loosen the knurled nut on the gun cable (5) and remove connector.
3. Loosen the union nut (4) of the air hose at the AquaCoat cabinet.
4. Unscrew knurled nut (2).
5. Carefully remove the gun (1) together with the hose set.
Summary of Contents for AquaCoat AirCoat GM 5000EACW
Page 2: ......
Page 38: ...38 AquaCoat GM 5000EACW OPERATING MANUAL EDITION 04 2012 PART NO DOC2321362 ...
Page 92: ...92 AquaCoat GM 5000EACW OPERATING MANUAL EDITION 04 2012 PART NO DOC2321362 ...
Page 101: ...101 AquaCoat GM 5000EACW OPERATING MANUAL EDITION 04 2012 PART NO DOC2321362 ...
Page 111: ......