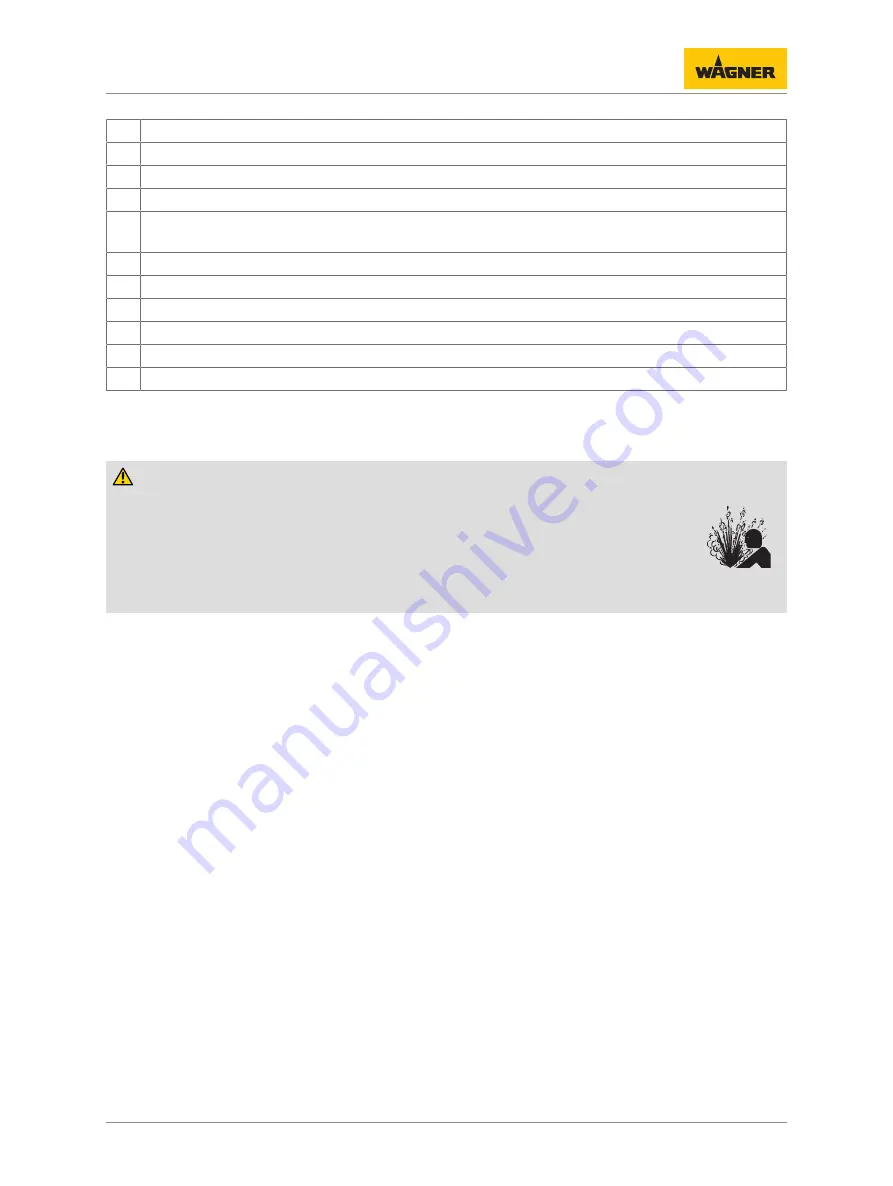
Operating manual Universal Control Unit for Powder Spray Guns EPG-SPRINT XE
6 Assembly and Commissioning
Order number 2354913 | Edition 10/2022
29
8
Powder injector
9
Powder feed, e.g., from the powder tank
10 Feed air, red
11 Grounding cable to the signal ground
12 EPG-Sprint X: mains output to next control unit
EPG-Sprint XE: mains output terminal (no application)
13 Mains input terminal
14 Start/Stop command from external controller (master controller)
15 Electrical connection cable
16 Powder hose connection
17 Tribo air
18 Electrical connection
* A Y-distributor (order no. 9990149) is needed to divide the Tribo and atomizing air.
6.6 GROUNDING
DANGER
No grounding!
Risk of explosion and risk of electric shock!
4
Electrostatic control units and the associated spray equipment may only be
connected to mains supplies with a protective conductor connection (PE
conductor)!
For safety reasons, the control unit must be properly grounded. The grounding connection
to the energy supply (socket) is made via the mains connection cable's protective conductor,
while that to the work piece/system is made via the knurled screw on the rear of the control
unit. Both connections are absolutely essential. The gun is grounded according to
instructions for proper commissioning.
Good grounding of the work piece is also necessary for optimum powder coating.
A poorly grounded work piece causes:
– dangerous electric charging of the work piece
– very bad wrap-around
– uneven coating
– back spraying to the spray gun, i.e., contamination
Prerequisites for perfect grounding and coating of a work piece are:
– Clean suspension of the work piece to be coated.
– Grounding of the powder coating booth, transport and suspension equipment to be
provided on site in accordance with the corresponding operating manuals or the
definitions laid down by the manufacturer
– That a grounding resistance of the work piece of 1 MΩ is not exceeded
(resistance to ground measured at 500 V or 1000 V).
Sparks between conveyor, conveyor hooks (hangers) and work piece can occur if
electric contact points between conveyor, conveyor hooks (hangers) and work piece
are not sufficiently cleaned and therefore the work pieces are not sufficiently
grounded! These sparks can cause heavy radio frequency interference (EMC).