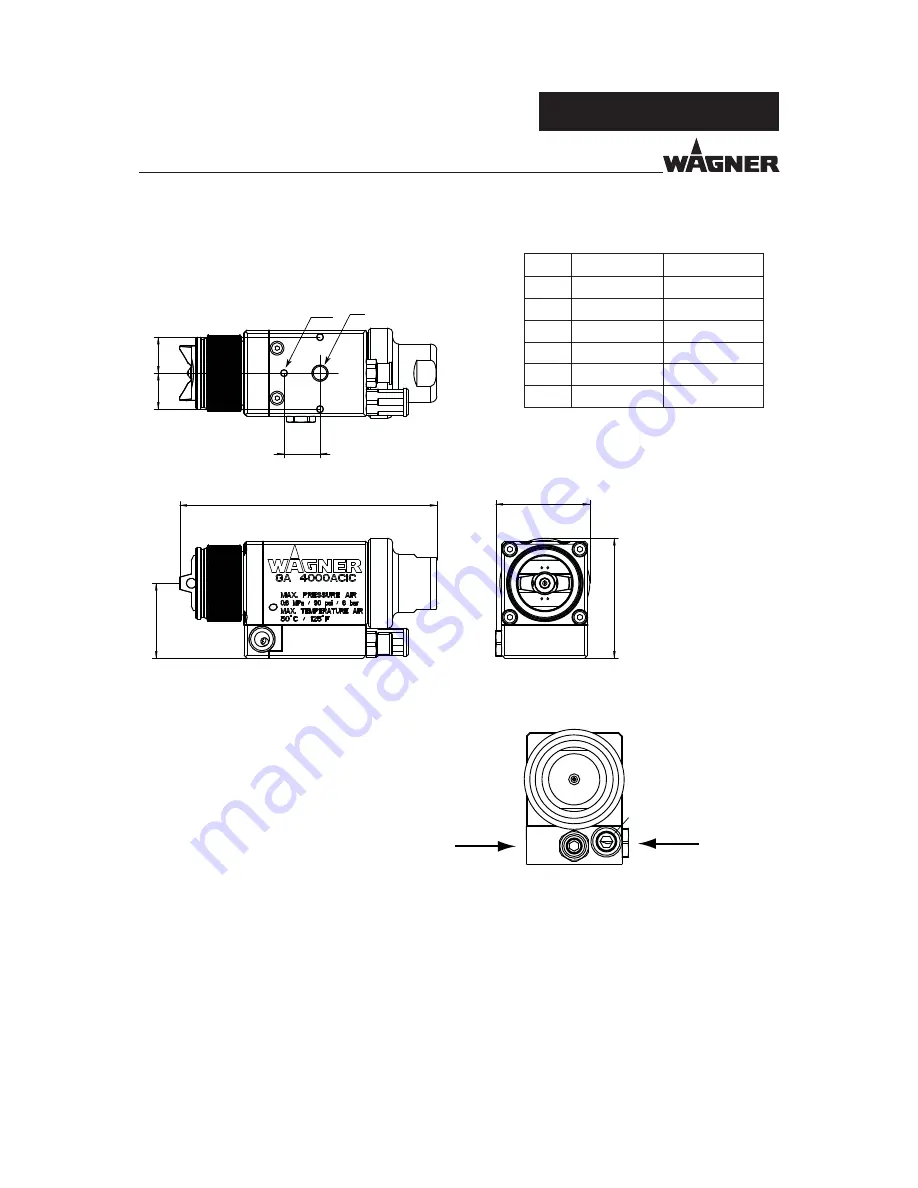
19
GA 4000ACIC
FF
E
A
D
C
B
B_03057
M8
Ø 3.2
mm
inch
A
129
5.08
B
47
1.85
C
60
2.36
D
37.5
1.48
E
18±0.1
0.71±0.004
F
18±0.1
0.71±0.004
B_3488
-
-
CA
AA
OPERATING MANUAL
EDITION 06/ 2011
PART NO. DOC2312956
Metals Plastic
Hard metal
UHMW-PE
Stainless steel 1.4310 PTFE
Stainless steel 1.4305 FPM
Stainless steel 1.4104 POM
PA
6.6
EPDM
4.3.3
MATERIALS OF PAINT WETTED PARTS
Connection data:
Ground plate to GA 4000ACIC S
CA = G1/8“ -> 6 mm; 0.24 inch (control air)
AA = G1/8“ -> 8 mm; 0.31 inch (atomizing air)
M = G1/4“ -> NPS1/4“ (material)