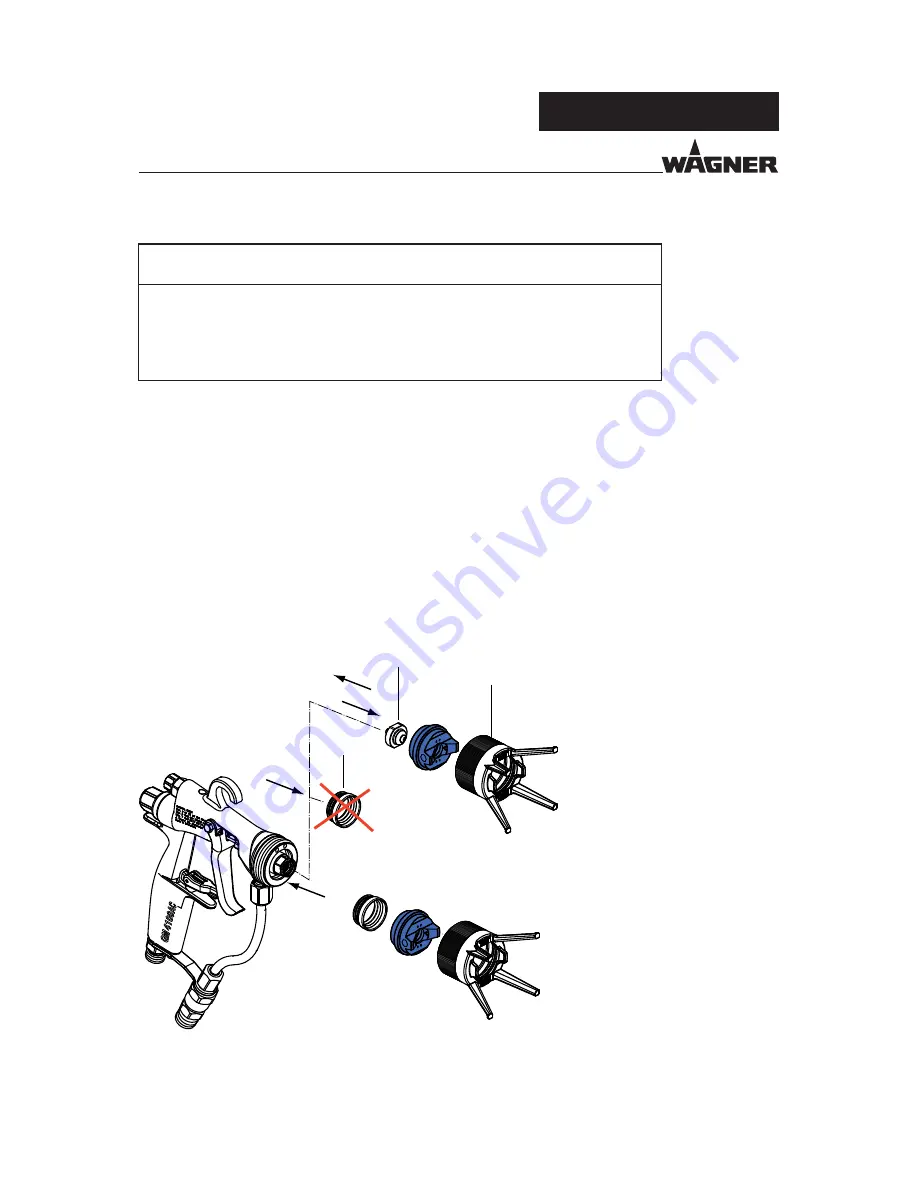
31
GM 4100AC
B_02270
14 (F)
13
36
33
?
?
?
?
OPERATING MANUAL
EDITION 12/2008
PART NO. DOC394821
1. Finishing work and cleaning.
2. Relieve spray gun and unit pressure.
3. Secure gun with trigger safety catch.
4. Unscrew the union nut with nozzle guard (33).
5. Remove air cap (36) and nozzle (13).
6. Remove defective sealing ring (14/F) with the help of pipe tongs or with a large
screwdriver.
7.
Assembling:
Fit new distributor seal (14/F) to air cap (36).
8. Place air cap in body of gun together with sealing ring (14).
9. Attach union nut (33) and screw in until the sealing ring snaps into place in the
mounting groove (snap hearable).
10.
Demount union nut (33) and air cap (36) and complete spray gun according to
paragraph 5.4.3
.
CAUTION
Forming air and atomizer air not separate!
Poor spray pattern
Spray jet cannot be adjusted
Treat the distributor seal (F) with care.
SIHI_0030_GB
6.6
REPLACING THE „AIR“ SEALING RING