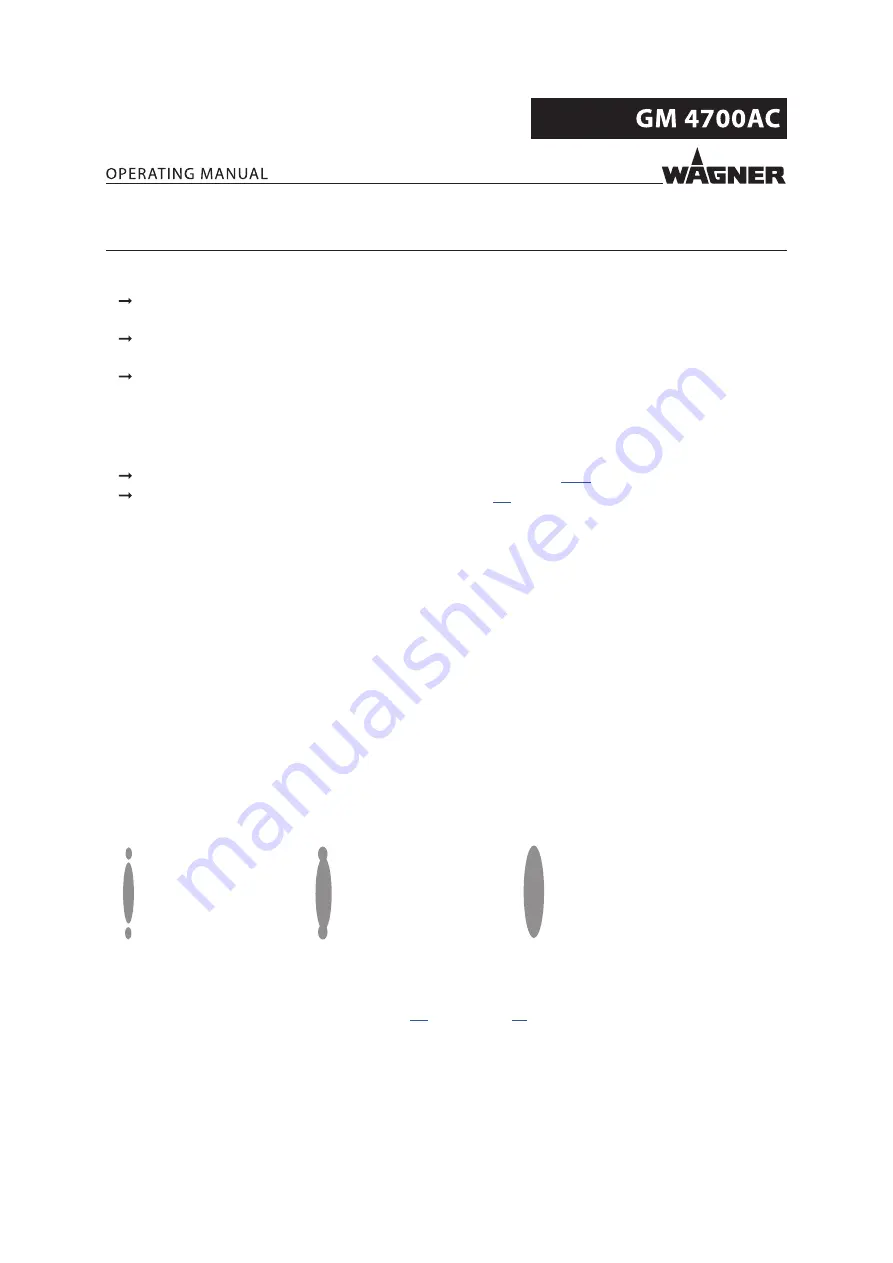
23
7
OPERATION
7.1
TRAINING THE OPERATING PERSONNEL
The operating personnel must be qualified to operate the entire system.
The operating personnel must be familiar with the potential risks associated with
improper behavior as well as the necessary protective devices and measures.
Before work commences, the operating personnel must receive appropriate system
training.
7.2
TASKS
Ensure that:
the regular safety checks are carried out in accordance with Chapter
commissioning is carried out in accordance with Chapter
.
7.2.1 STARTING TO SPRAY WITH THE AIRCOAT
1. Start up with product supply set to approx. 8 MPa; 80 bar; 1160 psi operating
pressure.
2. Spray (release locking device and pull trigger) and at the same time, observe how the
product is atomizing.
3. Set the spray pressure on the product pump to a point where good product
atomization is achieved.
4. Open the air pressure regulator for the atomizing air and adjust it so that an optimal
atomization is achieved. (The interrelation between spray pattern and atomizing air
is shown in the figure below).
5. Use the shaping air controller on the spray gun to adjust the shaping air to atomizing
air ratio, until the optimal spray pattern is achieved.
Note:
Repeat points 3, 4 and 5 until the optimum is reached (iterative process).
Spray pattern shapes
B_00071
No atomizing
air
Too little
atomizing air
Correct amount
of atomizing air
Note:
The flow rate can be changed by:
– changing the product pressure or
– Using a different flat jet nozzle (see Chapter
and Chapter
).
VERSION 06/2018
ORDER NUMBER DOC2311730
Summary of Contents for GM 4700AC
Page 1: ...AirCoat Manual Gun for Flat and Round Jet Nozzles Version 06 2018 B_02376...
Page 2: ......
Page 48: ...48...