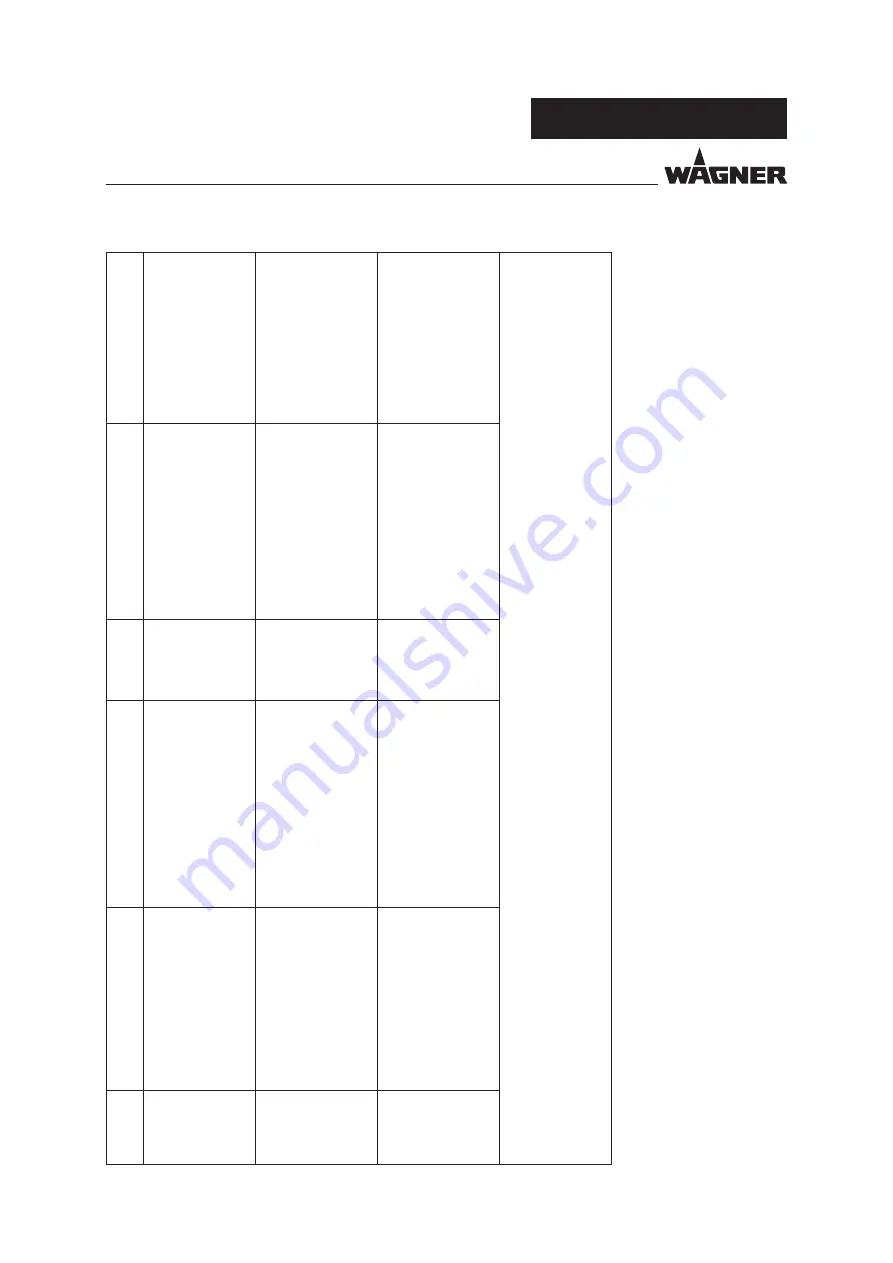
48
PEA-C4-HiCoat
OPERATING MANUAL
VERSION 05/2012
ORDER NUMBER DOC 390829
S
e
c
tion
T
y
pe of Inspec
tion
Requir
emen
ts
Inspec
tion
by
T
y
pe of Inspec
tion
Inspec
tion In
ter
v
al
1E
ff
ec
tiv
eness of t
echnical
v
e
ntilation check
Eff
ec
tiv
eness of t
echnical
v
e
ntilation check
TP/CP
ME
e
.g
. measur
ements of air fl
ow
speed / air quantities
,
check
ing of the diff
er
ential
pr
essur
e indicat
or ac
co
rding
to
the cabin manufac
tur
er's
instruc
tions
.
co
ntinuously
ac
co
rding t
o
the cabin
manufac
tur
er's instruc
tions
2
Int
erlock bet
w
een t
echnical
v
e
ntilation and high-v
oltage
,
compr
essed air and c
o
ating
mat
e
rial supply
T
he t
echnical v
e
ntilation should
be int
e
rlocked such that the high-
v
oltage cannot be swit
ched on
while the t
echnical v
e
ntilation is
not w
o
rk
ing eff
ec
tiv
ely
.
CP
FI
Test whether the sy
st
em is saf
ely
st
opped and the mat
e
rial supply
,
supply air and high-v
oltage
ar
e swit
ched off
when the
v
e
ntilation is shut do
wn.
annually
3
P
ro
te
c
tion against ig
nition of
fl
ammable cleaning agents
If
fl
ammable cleaning fl
uids
ar
e
used
, all par
ts carr
ying high-
v
oltage must be dischar
ged t
o
a
dischar
ge ener
gy of less than 0,24
mJ
, onc
e the high-v
oltage has
been swit
ched off
, bef
or
e they can
be r
eached
.
CP
ME/FI
F
unc
tion t
est of the r
esidual
ener
gy monit
oring equipment
ac
co
rding t
o
the manufac
tur
er's
instruc
tions
.
ac
co
rding t
o
the
manufac
tur
er's instruc
tions
Ke
y
:
M
A
= M
anufac
tur
er
EM = Emplo
y
e
r
CP = C
apable person
FSE = F
ir
e
saf
et
y eng
ineer
EL
C = Elec
trician
TP =
T
rained person
FI = F
unc
tion inspec
tion
ME = M
easur
ement
SI = Standar
d inspec
tion
VI =
V
isual inspec
tion
CI = C
o
ntinuous inspec
tion
TI =
Technical inspec
tion
9.1
OVERVIEW OF INSPECTIONS