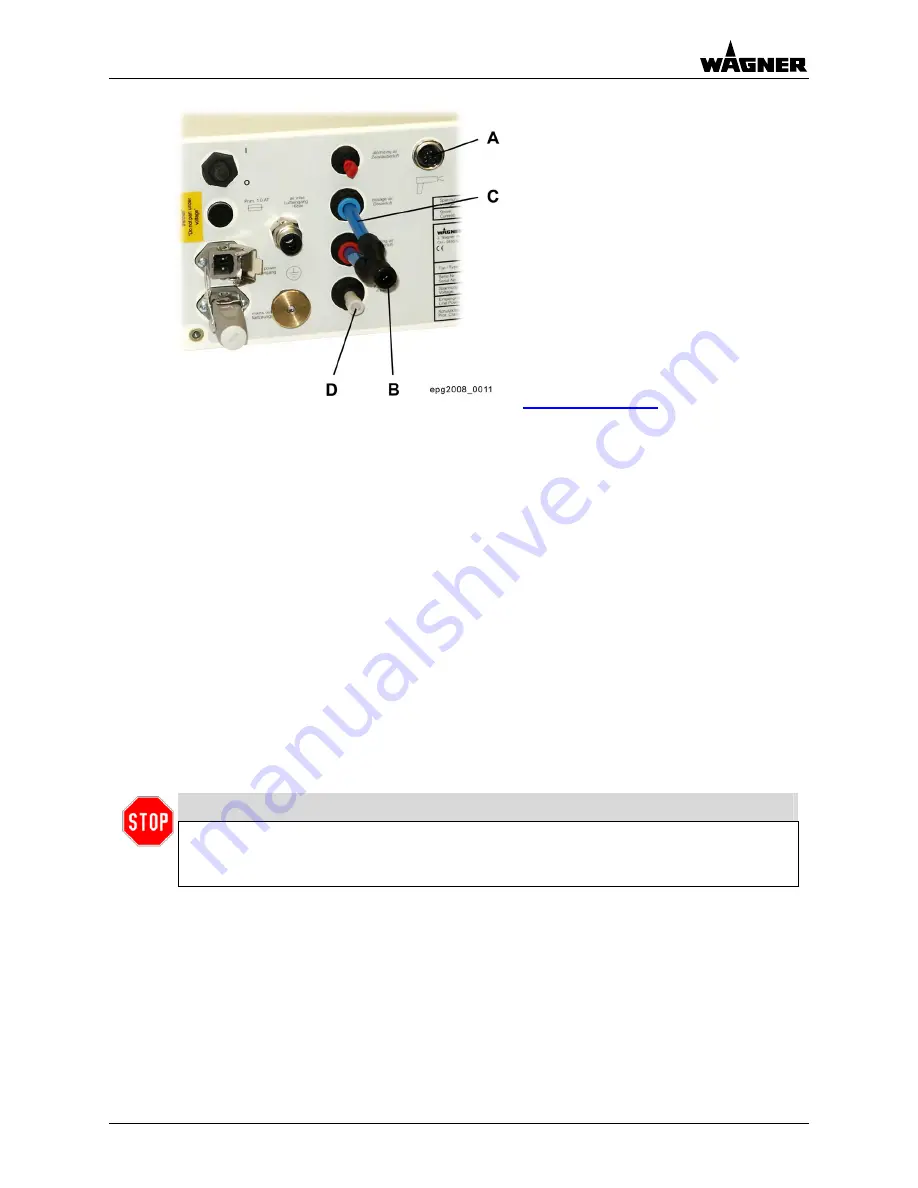
Preparing the spray gun
04/2006
0351717
- PEM-TG3
11
Rückwand
EPG 2008
the spray gun is connected to
the
EPG 2008
, then the reduction
piece (6/8) must be placed at the
other end of the hose and connected
to the Y-plug connection
B
.
•
The Y-plug connection (8-8) is
connected with the two blue hoses
(external
∅
8x1.5)
C
to the feed and
dosage air connection of the
EPG 2008.
•
The air vent has to be blocked with
the stopper
D
.
The required parts are listed in section
"
Special accessory
•
When
".
2.4
Grounding
For safety reasons, the
spray gun
must
be properly grounded. This occurs through the
electrical cable.
0203_ .doc
Good grounding of the
workpiece
is also necessary for optimum powder coating.
A poorly grounded workpiece causes:
•
dangerous electric charging of the workpiece
•
back-spray onto spray gun and user
•
uneven coating
•
very bad wrap around
Warning
Sparks between workpiece and conveyor hooks (hangers) can occur if hooks or
other hanger parts are not completely cleaned!
These sparks can cause heavy radio frequency interference.
Summary of Contents for PEM-TG3
Page 29: ...Notes 04 2006 0351717 PEM TG3 29...