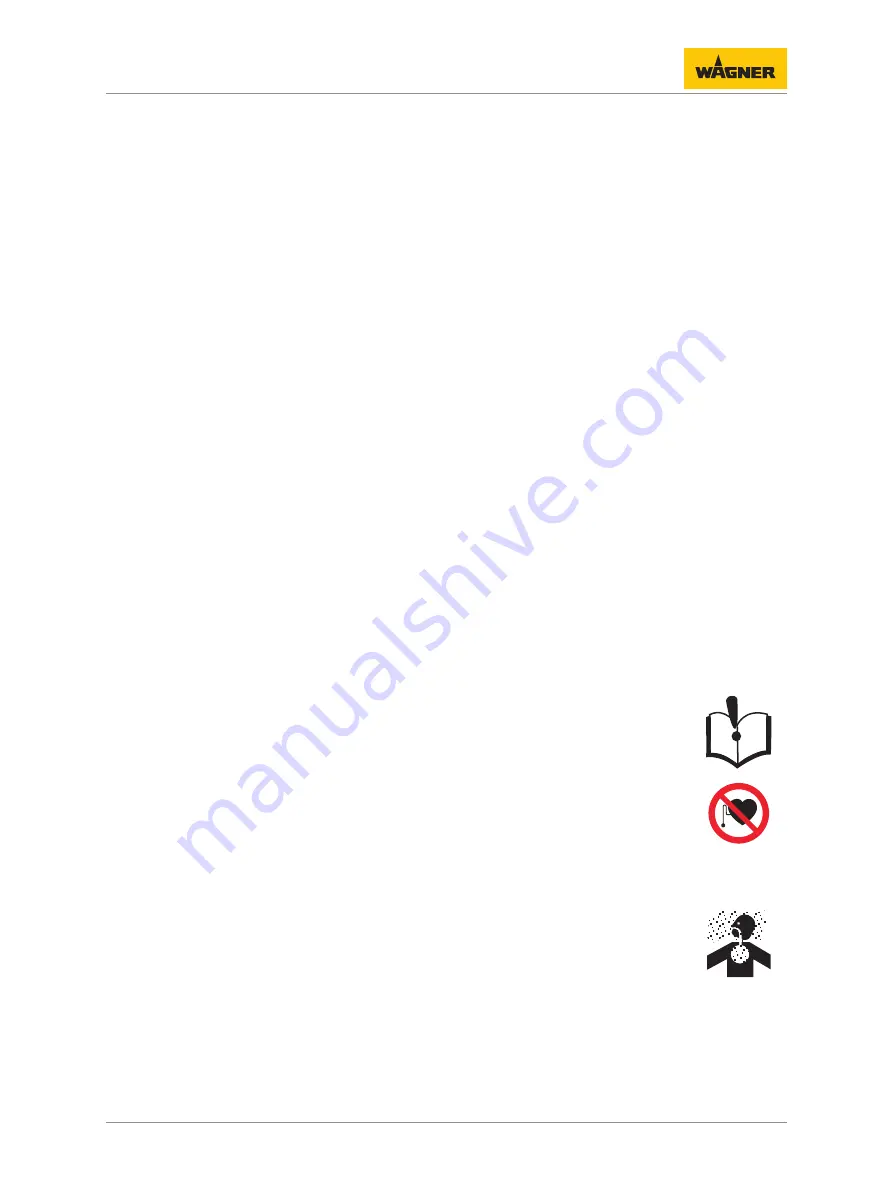
Operating manual Powder Cup Gun PEM-X1 CG
4 Basic Safety Instructions
Order number 2326960 | Edition 10/2022
13
4
Protective clothing including gloves, must correspond to EN 1149-5. The measured
insulation resistance must not exceed 100 MΩ.
4
Ensure that there are no ignition sources such as naked flames, sparks, glowing wires,
or hot surfaces in the spray booth. Do not smoke.
4
A suitable system for suppressing fire and explosion must be installed.
4
The powder release must be electrically interlocked with the connected technical
ventilation of the spray system.
4
Excess coating product (overspray) must be collected up safely.
Accumulations of powder in the spray booth is to be avoided. Set the parameters of the
floor cleaning and manually clean the spray booth as needed.
4
Ensure that maintenance and safety checks are performed regularly.
4
In case of defects, immediately shut down the device or system and repair before
switching back on.
Accumulations of powder are to be removed before switching the system back on.
4
The operator/responsible person must ensure that an average concentration of powder
lacquer in the air of 50% of the lower explosion limit (max. permitted powder/air
concentration) is not exceeded. If there is no reliable lower explosion limit value, the
average concentration of 20 g/m³ must not be exceeded.
4.1.3 Personnel Qualifications
Danger due to incorrect use of device!
Risk of death due to untrained personnel.
4
Ensure that the operating personnel has been instructed by the operator in accordance
with the operating manual and the operating instructions. The device must only be
operated, maintained and repaired by trained personnel. Refer to the operating
instructions for information about the required personnel qualifications.
4.2 SAFETY INSTRUCTIONS FOR THE PERSONNEL
4
Always observe the information in this manual, particularly the safety instructions and
the warning instructions.
4
Always follow existing regulations concerning occupational safety and accident
prevention regulations.
Danger due to high-voltage field!
Danger to life from malfunction of active implants.
4
Persons belonging to a risk group according to EMF guideline 2013/35/EU (e.g., carriers
of active implants), must not enter the high-voltage area.
4.2.1 Personal Safety Equipment
Danger due to dust formation!
Serious or fatal injuries due to inhalation, swallowing or contact with the skin or eyes.
4
Observe the processing regulations laid down by the manufacturer of the powder
lacquer being used, when preparing or processing the powder.
4
Take note of the manufacturer’s notification and the relevant environmental protection
regulations when disposing of powder lacquers.
4
Take the specified protective measures, in particular wear safety goggles, protective
clothing and gloves, as well as skin protection cream if necessary.
4
Use a mask or breathing apparatus if necessary.