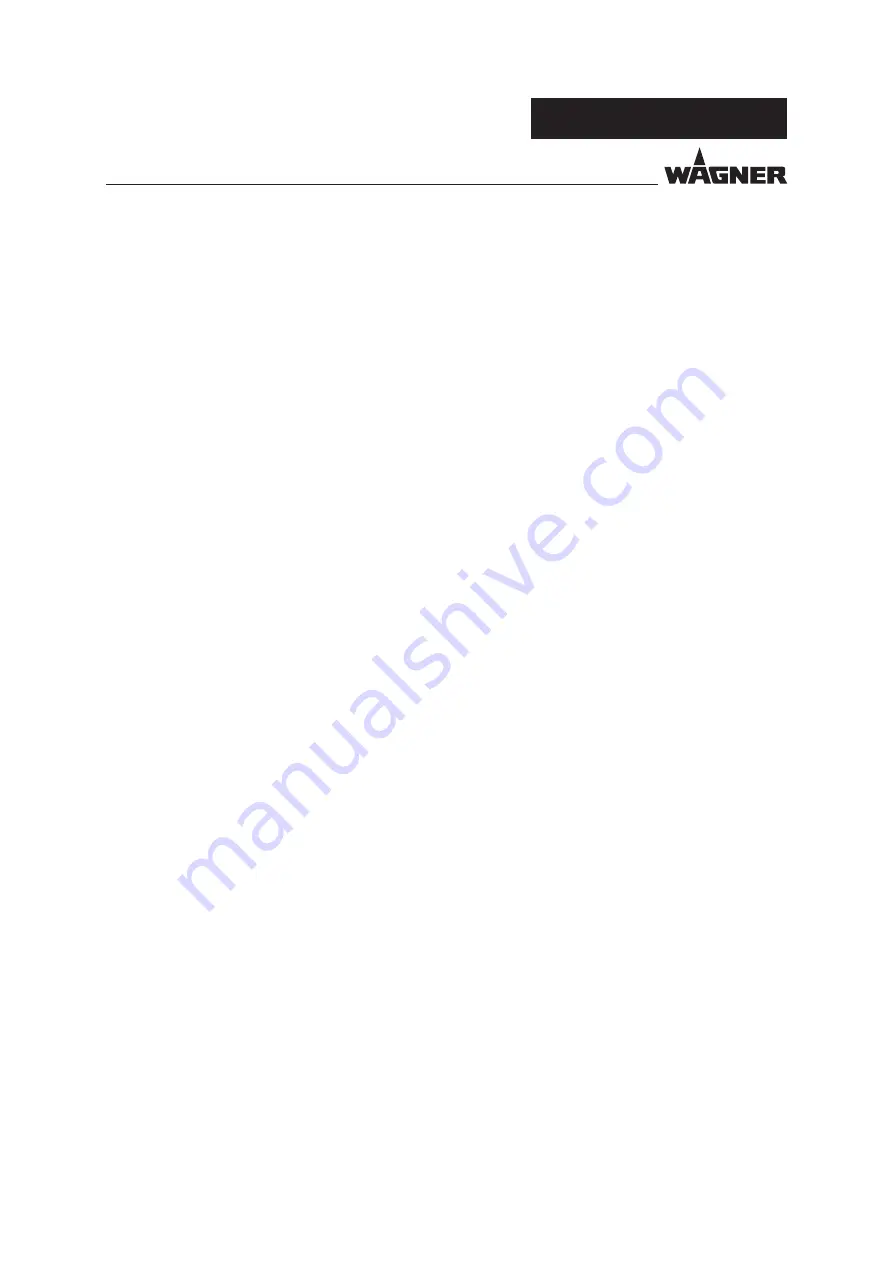
54
Prima Sprint
.
OPERATING MANUAL
VERSION 07/2009
ORDER NUMBER DOC 2305835
6.6
RINSE FUNCTION
The EPG-Sprint control unit has two different purge functions:
●
Hose purge function
●
Cleaning purge function
6.6.1
HOSE PURGE FUNCTION
This function blows dosage air through the powder feed hose and guns when the powder
fl ow is switched off (releasing of trigger lever on manual gun).
This function is set to the “OFF“ parameter value in the factory. The values can be changed
in the parameter settings for parameters C22 and C23 (see Device confi guration chapter).
6.6.2
CLEANING PURGE FUNCTION
This function is used at the end of a shift or when changing colour. All parts carrying powder
are purged in the process. The purge process takes place in pulses.
The cleaning purge function is only available when the control unit is switched on and in
the operating mode. In standby mode or in confi guration mode, this function is inactive.
Summary of Contents for Prima Sprint 3L
Page 2: ......
Page 96: ...96 Prima Sprint OPERATING MANUAL VERSION 07 2009 ORDER NUMBER DOC 2305835...
Page 124: ...124 Prima Sprint OPERATING MANUAL VERSION 07 2009 ORDER NUMBER DOC 2305835...
Page 125: ...125 Prima Sprint OPERATING MANUAL VERSION 07 2009 ORDER NUMBER DOC 2305835...
Page 127: ......