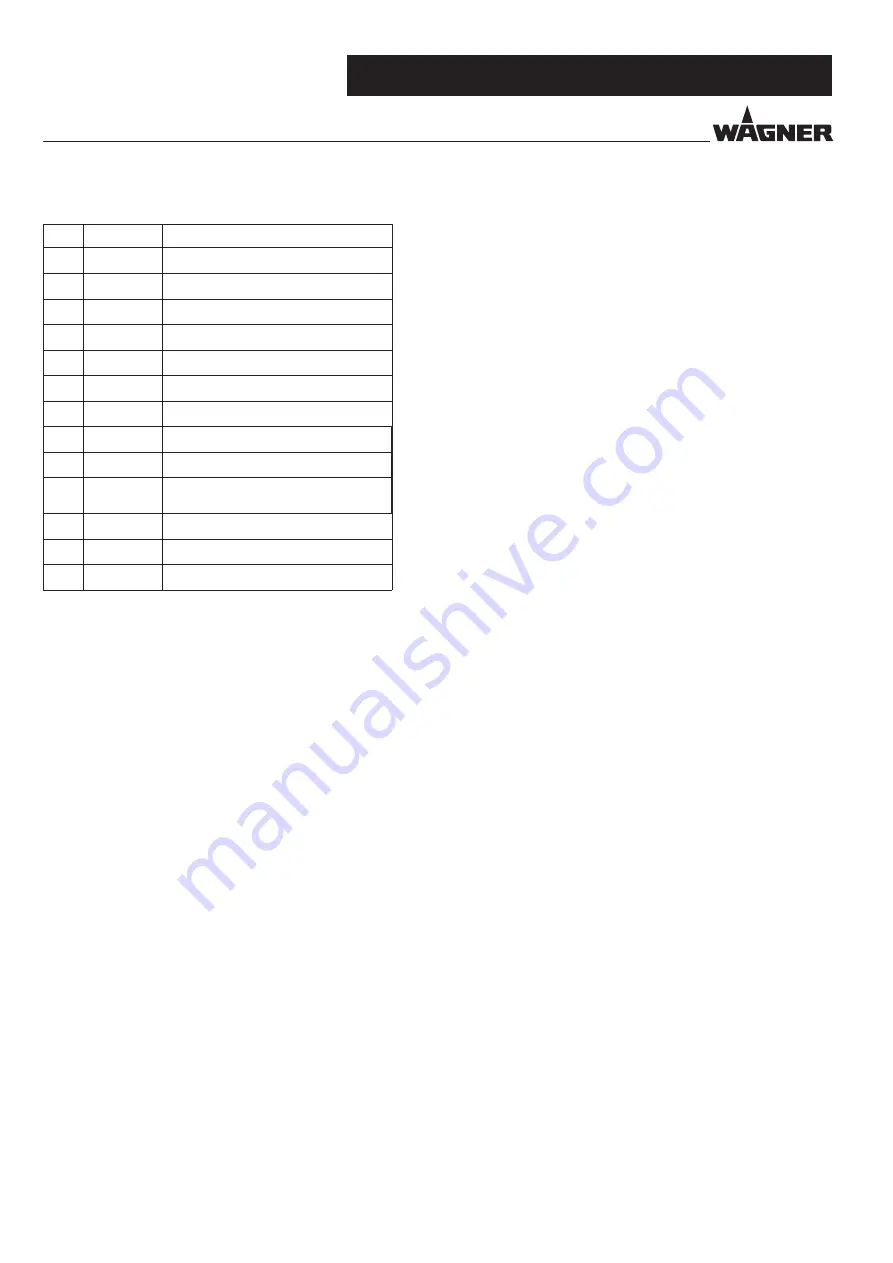
16
ProSpray 20
5.2
FLUID SECTION
#
Part No.*
Description
1
730-508
Retainer
2
700-587
Piston guide
4
0551 112
Transducer assembly
5
806-106
Fluid section housing
6
227-006
Fitting
7
0507 690
Bypass valve assembly
8
0507 745
Gasket
10
0509 151
Service Set piston
15
762-137
Inlet valve seat
16
0551 533
Service Set (consits of item 2, 3, 9, 11,
12, 13, 14, 16)
17
0532360A
Filter housing
18
581-060
Filter
18
560-038
O-ring
* Order number for 1 piece. Quantities in brackets indicate
the total number in the assembly.
GB
Summary of Contents for PROSPRAY 20
Page 2: ......
Page 13: ...13 ProSpray 20 GB...