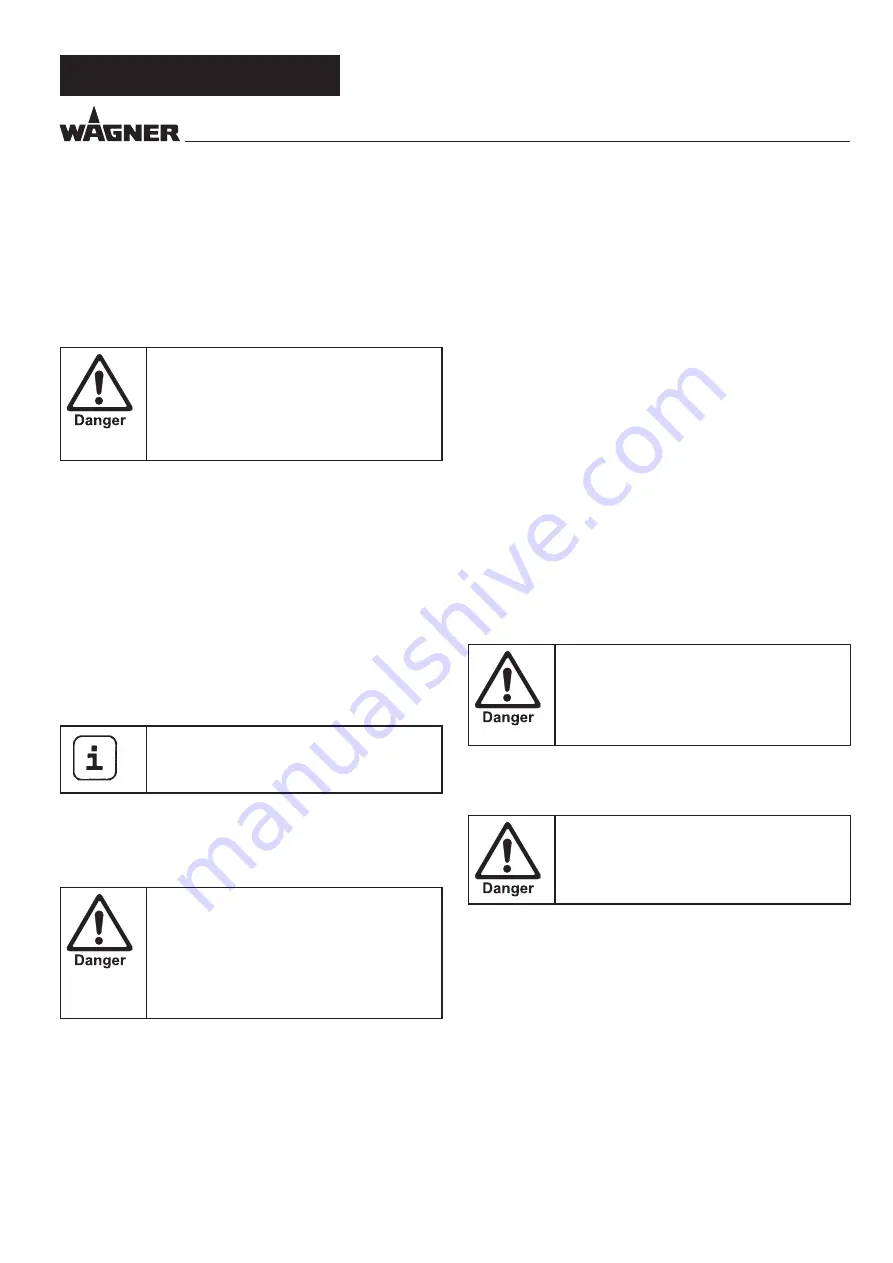
31
Super Finish 23 CR
SAFETY REGULATIONS
1.9
MAX. OPERATING PRESSURE
The permissible operating pressure for the spray gun, spray
gun accessories, unit accessories and high-pressure hose
must not fall short of the maximum operating pressure of 25
MPa (250 bar or 3625 psi).
1.10
HIGH-PRESSURE HOSE
Attention, danger of injury by injection! Wear
and tear and kinks as well as usage that is not
appropriate to the purpose of the device can
cause leakages to form in the high-pressure
hose. Liquid can be injected into the skin
through a leakage.
High-pressure hoses must be checked thoroughly before
they are used.
Replace any damaged high-pressure hose immediately.
Never repair defective high-pressure hoses yourself!
Avoid sharp bends and folds: the smallest bending radius
is about 20 cm.
Do
not drive over
the high-pressure hose. Protect against
sharp objects and edges.
Never pull on the high-pressure hose to move the device.
Do not twist the high-pressure hose.
Do not put the high-pressure hose into solvents. Use only
a wet cloth to wipe down the outside of the hose.
Lay the high-pressure hose in such a way as to ensure that
it cannot be tripped over.
Only use WAGNER original-high-pressure
hoses in order to ensure functionality, safety
and durability.
1.11
ELECTROSTATIC CHARGING (FORMATION OF
SPARKS OR FLAMES)
Electrostatic charging of the unit may occur
during spraying due to the flow speed of
the coating material. These can cause sparks
and flames upon discharge. The unit must
therefore always be earthed via the electrical
system. The unit must be connected to an
appropriately-grounded safety outlet.
An electrostatic charging of spray guns and the high-pressure
hose is discharged through the high-pressure hose. For this
reason the electric resistance between the connections of the
high-pressure hose must be equal to or lower than 1 MΩ.
1.12
USE OF UNITS ON BUILDING SITES AND
WORKSHOPS
The unit may only be connected to the mains network via a
special feeding point with a residual-current device with INF
≤ 30 mA.
1.13
VENTILATION WHEN SPRAYING IN ROOMS
Adequate ventilation to ensure removal of the solvent vapors
has to be ensured.
1.14
SUCTION INSTALLATIONS
The are to be provided by the unit user in accordance with the
corresponding local regulations.
1.15
EARTHING OF THE OBJECT
The object to be coated must be earthed.
(Building walls are usually earthed naturally)
1.16
CLEANING THE UNIT WITH SOLVENTS
When cleaning the unit with solvents, the
solvent should never be sprayed or pumped
back into a container with a small opening
(bunghole). An explosive gas/air mixture can
arise. The container must be earthed.
1.17
CLEANING THE UNIT
Danger of short-circuits caused by water in-
gression!
Never spray down the unit with high-pres-
sure or high-pressure steam cleaners.
1.18
WORK OR REPAIRS AT THE ELECTRICAL
EQUIPMENT
These may only be carried out by a skilled electrician. No li-
ability is assumed for incorrect installation.