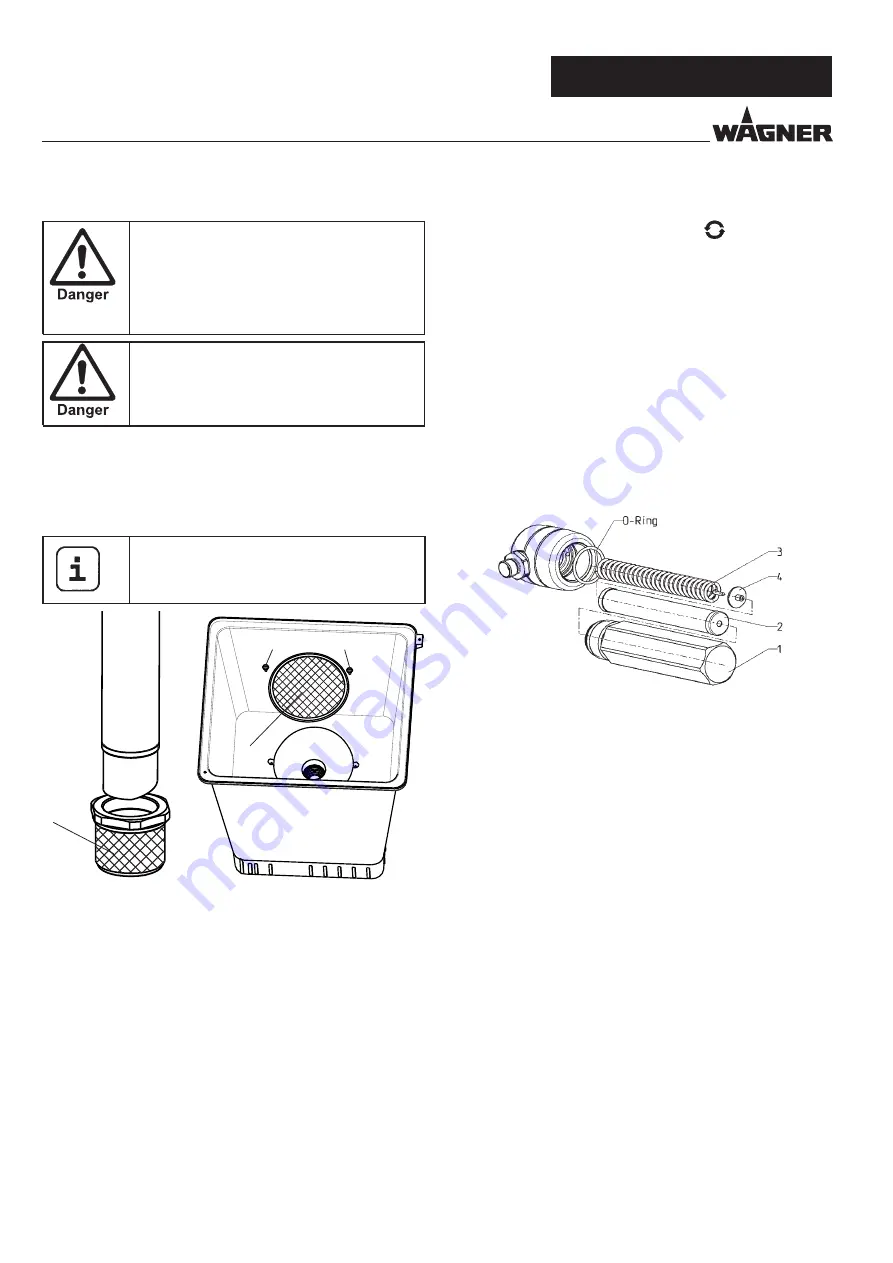
50
Super Finish 33 PRO
GB
8.1
CLEANING THE UNIT FROM THE OUTSIDE
First unplug the power plug from the outlet.
Danger of short-circuits caused by water
ingression! Never spray down the unit with
high-pressure or high-pressure steam clean-
ers.
Do not put the high-pressure hose into sol-
vents. Use only a wet cloth to wipe down the
outside of the hose.
Wipe down unit externally with a cloth which has been im-
mersed in a suitable cleaning agent.
8.2
SUCTION FILTER
Clean filters always ensure maximum volume,
constant spray pressure and problem-free
functioning of the unit.
Unit with suction system
1. Unscrew the filter (Item 1) from the suction tube.
2. Clean or replace the filter.
Carry out cleaning with a hard brush and a corresponding
cleaning agent.
8.3
HIGH-PRESSURE FILTER
1. Open the relief valve, valve setting
(circulation) and
switch off the device.
2. Open the high-pressure filter and clean the filter insert. To
do so:
3. Unscrew the filter housing (1) by hand.
4. Remove the filter insert (2) and pull out the bearing spring
(3).
5. Clean all the parts with the corresponding cleaning agent.
If compressed air is available – blow through the filter in-
sert and bearing spring.
6. When mounting the filter ensure that the bearing ring (4)
in the filter insert is positioned correctly and check the O-
ring at the filter housing for damage.
7. Screw on the filter housing by hand until it stops (a higher
tightening force only impedes later dismantling).
CLEANING THE UNIT
suction tube
hopper
Unit with hopper
1. Release screws with a screwdriver (Item 2).
2. Lift and remove filter disk with a screwdriver
3. Clean or replace the filter disk.
Carry out cleaning with a hard brush and a corresponding
cleaning agent.
1
2
1
2
Summary of Contents for Super Finish 33 Pro
Page 21: ...57 Super Finish 33 PRO GB ...
Page 29: ...65 Super Finish 33 PRO GB ...