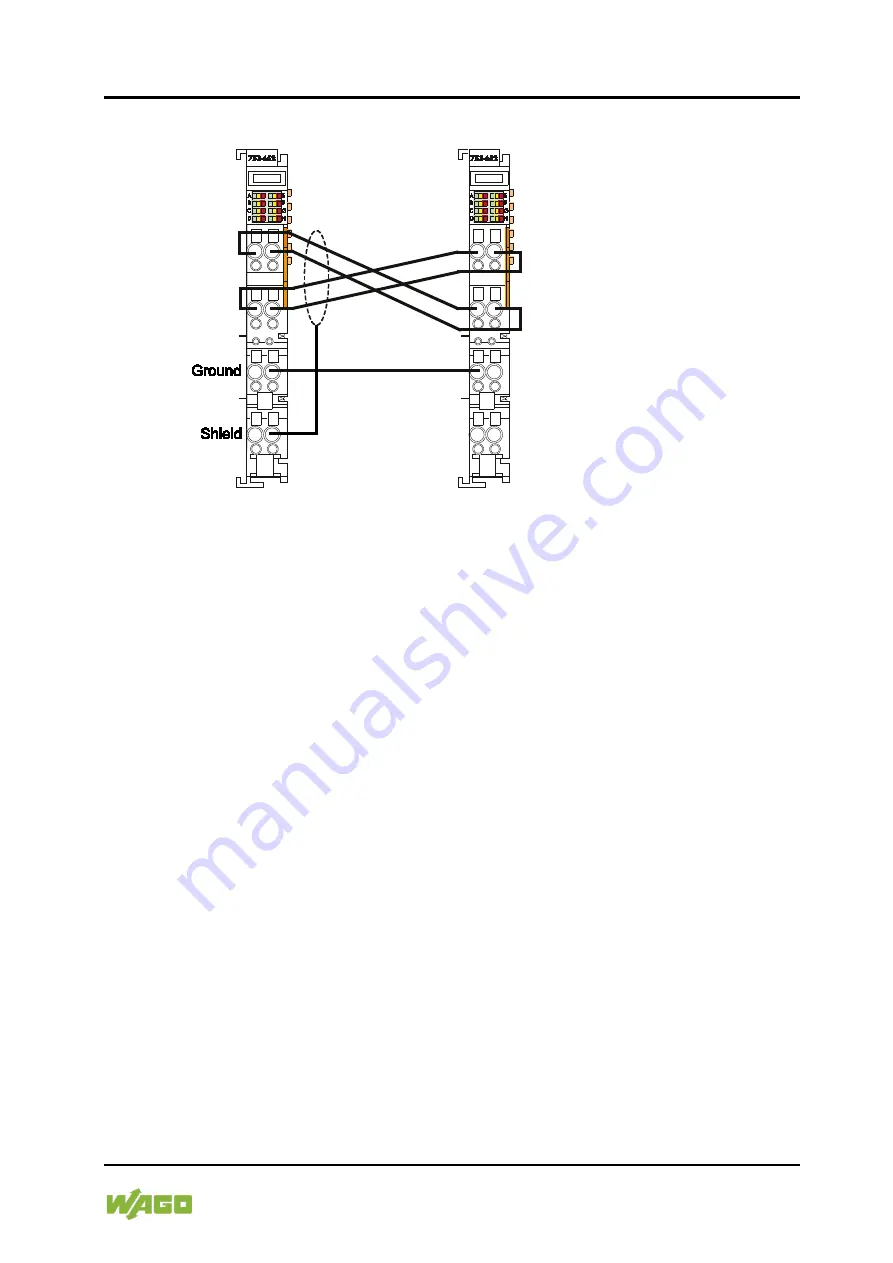
WAGO-I/O-SYSTEM 750 XTR
Connect Devices 53
750-652/040-000 Serial Interface RS-232/RS-485 XTR
Manual
Version 1.3.0
7.2.5
Data Exchange Mode
Figure 16: Point-to-point Connection Between 2 Nodes
In this mode, the contacts of the I/O modules to connect are connected to each
other crosswise.
In the Data Exchange operating mode (point-to-point connection), a twisted-pair
cable should be used at least for larger cable lengths. 2 wire pairs and 1 ground
wire are required. The ends of the cable should be terminated with a terminal
resistor.
Generally, a passive resistance is used by connecting the signal lines via one
100
Ω
… 120
Ω
resistor apiece to the ends of the cable (A-B).