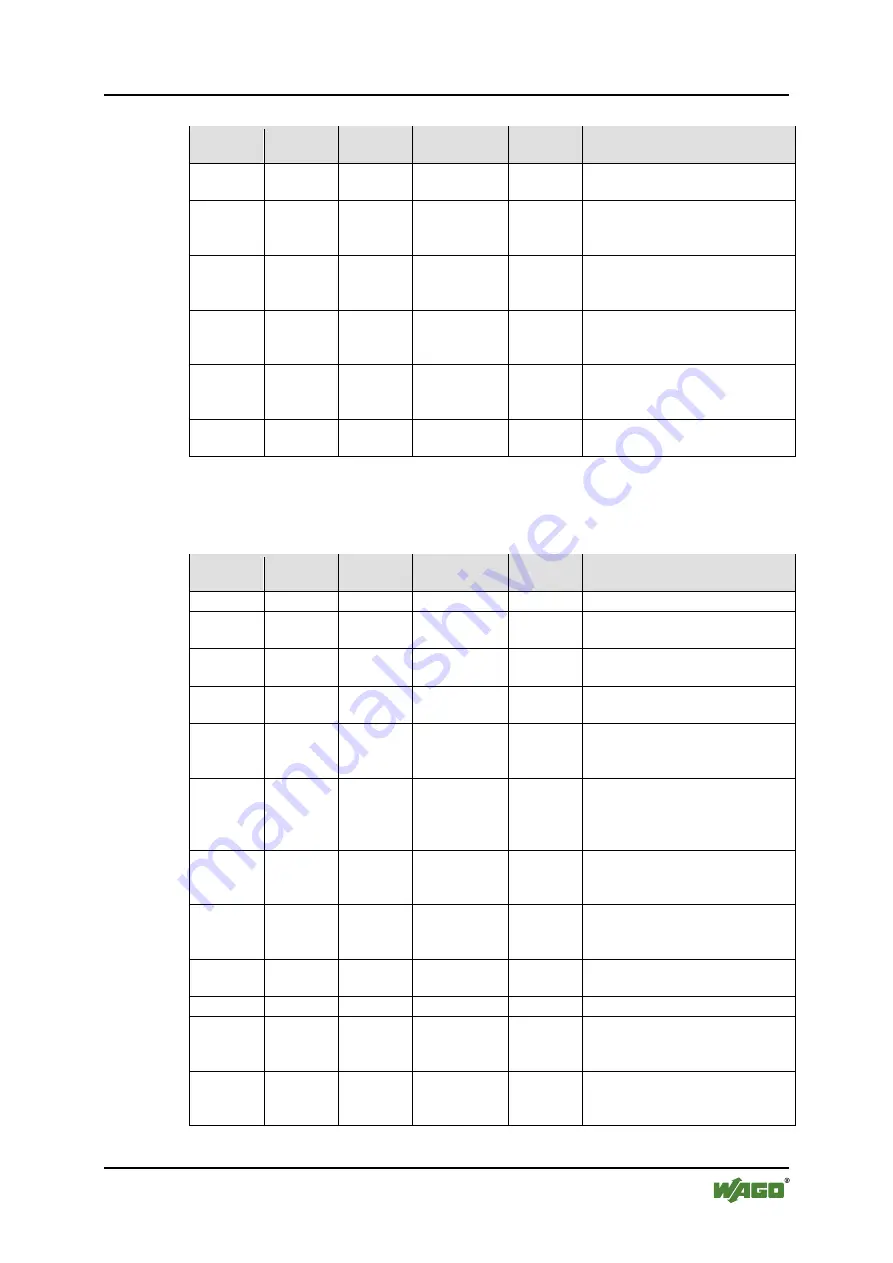
WAGO-I/O-SYSTEM 750
Fieldbus Communication 105
750-306 DeviceNet
TM
Fieldbus Coupler
Manual
Version 2.0.0
Table 74: Instance 2
Attributes
ID
Utilization
in Device
Access
Rights
Name
Data Type Description
12
required
get
watchdog_
timeout_action
USINT
Defines how to handle inactivity /
watchdog timeouts
13
required
get
produced_
connection_
path_length
UINT
Number of bytes in
“produced_connection_path”
attribute
14
required
get/set
produced_
connection_
path
Array of
USINT
Specifies application objects,
whose data are generated in this
connection object
15
required
get
consumed_
connection_
path_length
UINT
Number of bytes in
“consumed_connection_path”
attribute
16
required
get/set
consumed_
connection_
path
Array of
USINT
Specifies application objects,
whose data are received by this
“connection object”
17
required
get
production_
inhibit_time
USINT
Defines the minimum time
between data transmission
Instance 3 (Bit-Strobe I/O Connection)
Table 75: Instance 3
Attributes
ID
Utilization
in Device
Access
Rights
Name
Data Type Description
1
Available get
state
USINT
Object state
2
required
get
instance_
type
USINT
Displays “I/O” or “messaging
connection”
3
required
get
transportC
lass_trigger
USINT
Defines the connection behavior
4
required
get
produced_
connection_id
UINT
In the CAN identifier field when
transmitting
5
required
get
consumed_
connection_id
UINT
CAN identifier field value that
denotes the “message” that should
be transmitted
6
required
get
initial_comm_
characteristics
USINT
Defines the message groups
across which “productions” and
“consumptions” associated with
this connection occur
7
required
get
produced_
connection_
size
UINT
Maximum number of bytes that
can be transmitted via the
connection
8
required
get
consumed_
connection_
size
UINT
Maximum number of bytes that
can be received via the
connection
9
required
get/set
expected_
packet_rate
UINT
Defines the “timing” of the
connection
10, 11
N/A
get
N/A
N/A
not used
12
required
get
watchdog_
timeout_action
USINT
Defines how to handle
“inactivity” / “watchdog
timeouts”
13
required
get
produced_
connection_
path_length
UINT
Number of bytes in
“produced_connection_path”
attribute