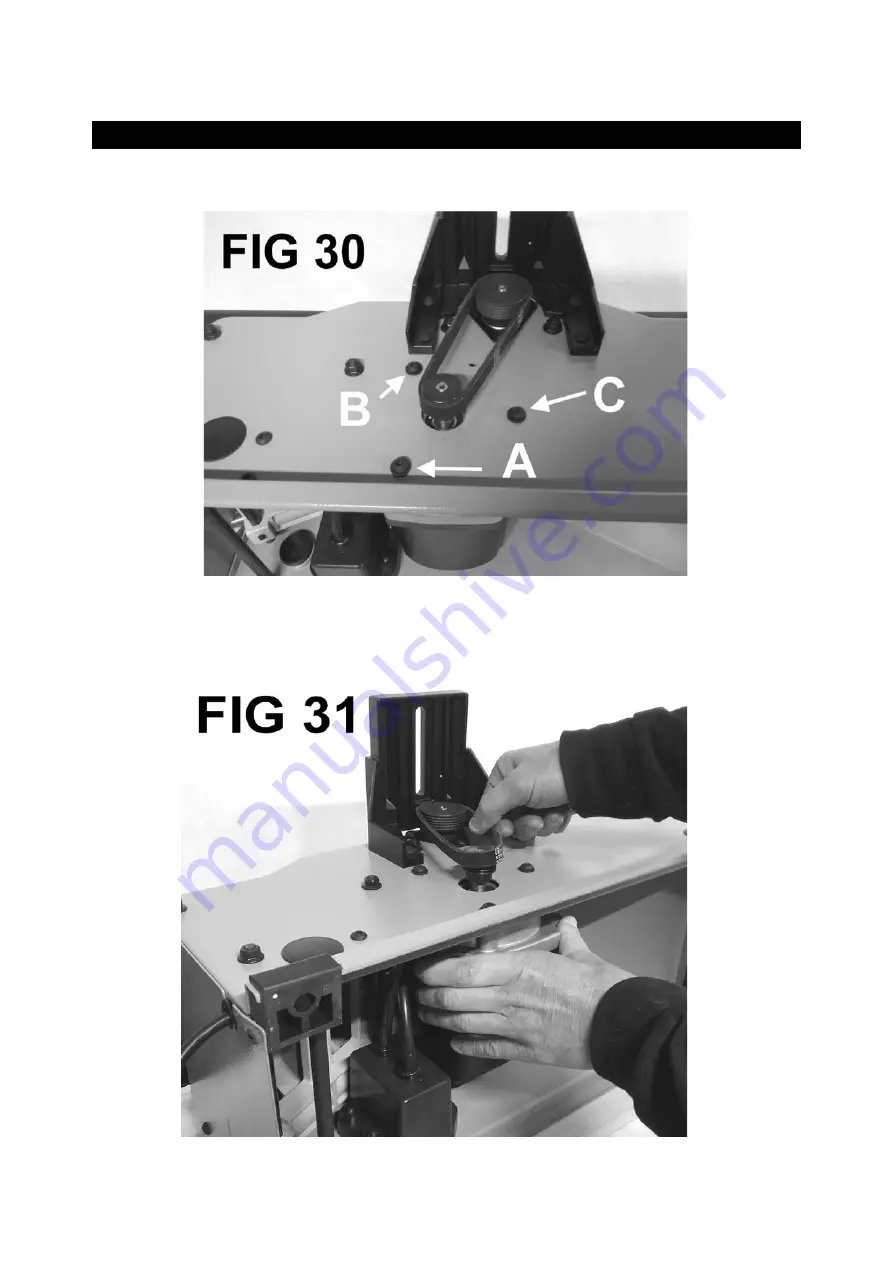
31
MAINTENANCE (cont.)
3. Loosen the 3 motor mounting screws “A”, “B” and “C”, about 1 full turn. See FIG 30
4. From the exposed open base, gently push motor away from you with left hand to release belt
tension and rotate the belt to walk the belt off the motor pulley with your right hand. See FIG 31
Summary of Contents for 50180CC-WHD
Page 13: ...13...
Page 34: ...34 TROUBLESHOOTING GUIDE cont...
Page 35: ...35 TROUBLESHOOTING GUIDE cont...
Page 43: ...43 PARTS DIAGRAM...