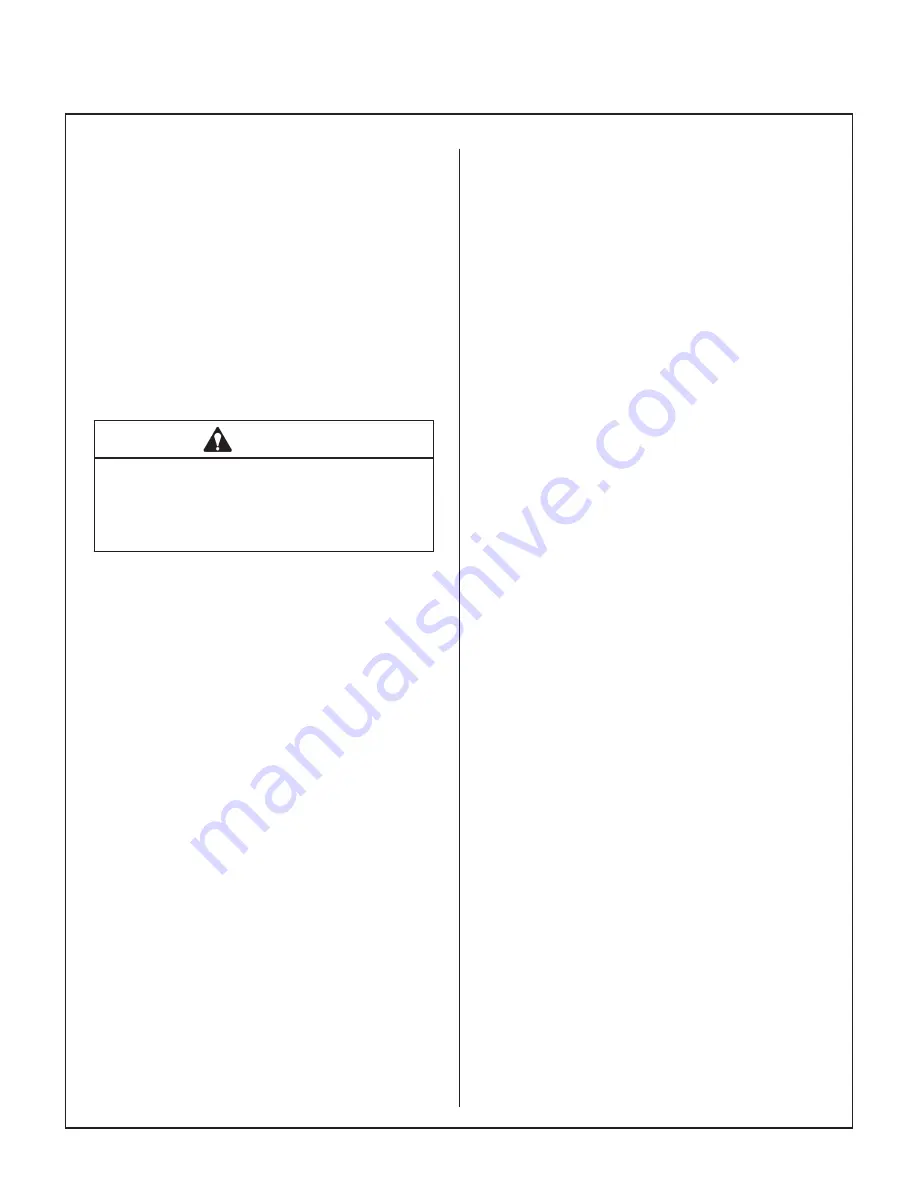
54
Maintenance Instructions
CHECKING/SERVICING
PTO U-Joints
The PTO U-joints should be inspected
yearly
for
looseness and wear. If either is noticed, the respec-
tive shaft or tube should be replaced. A worn U-joint
can cause vibration and extensive damage to the
PTO and the whole machine.
Ignition Wires
Good preventive maintenance calls for complete
replacement
of spark plug wires
every two (2)
years.
Safety Switch System
WARNING
It is important to check and maintain the
safety switch system for safe operation of
the machine.
There are three (3) safety interlock switches on the
tractor; Seat Switch, FSC Neutral-Park Switch, and
PTO Switch.
If any of the following conditions occur during start-
ing or operating, a safety interlock switch may be
malfunctioning. Contact your Walker dealer for trou-
bleshooting and/or replacement.
•
With or without an operator in the seat, the engine
starts with the Forward Speed Control (FSC) and/or
the PTO engaged.
•
With an operator in the seat, the engine starts but
dies soon after the Forward Speed Control (FSC) or
PTO is engaged.
•
Without
an operator in the seat, the engine con-
tinues to run with the Forward Speed Control (FSC)
and/or PTO engaged.
•
With an operator in the seat, the Forward Speed
Control (FSC) and PTO disengaged, but the starter
is not engaging.
Forward Speed Control Friction Lock
The FSC friction lock is designed to
hold the se-
lected forward travel speed
when the steering le-
vers are moved and yet the friction is not too heavy
to make
moving the FSC control
difficult (too much
friction). The procedure for checking the FSC fric-
tion lock is as follows:
1. With the engine off, place the FSC in the full
FORWARD
position and pull both steering le-
vers back; the FSC lever should not move. If
the FSC lever moves back when the steering
levers are pulled back, the
friction needs to be
increased.
2. With the steering levers held back, move the
FSC lever back from the
FORWARD
position.
With a proper amount of friction adjusted, the
FSC lever should move back with a slight
amount of resistance (friction). If the FSC lever
movement is “stiff”,
the friction needs to be
decreased.
If the FSC friction lock needs to be adjusted, refer to
ADJUSTMENTS
for
Step 7 -
Forward Speed Con-
trol Friction Adjustment
in this section.
Summary of Contents for B18
Page 73: ...69 Operator s Notes...
Page 74: ...70 Operator s Notes...