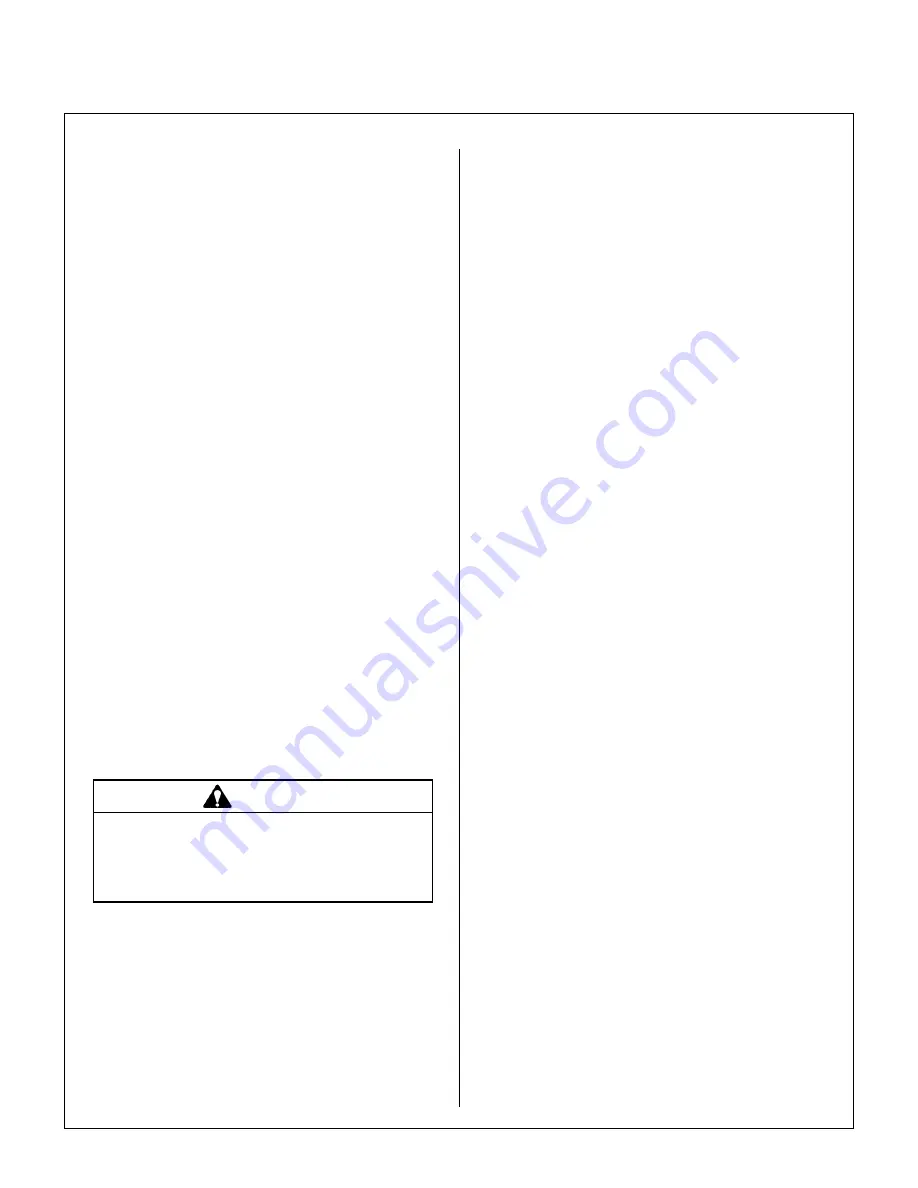
Maintenance Instructions
KAWASAKI TIPS
41
IMPORTANT TIPS FOR CARE OF THE
KAWASAKI ENGINE
Fuel System
•
Fuel must be clean - free from water, dirt, and or-
ganic material.
•
Clean the fuel filter on a regular basis and when
contamination is suspected or found in the fuel.
Starting
•
Start engine with the throttle advanced off idle
(1/4 to 1/2 throttle). This will aid starting, especially
in cold weather.
•
Keep the battery fully charged.
•
Match crankcase oil viscosity to the ambient tem-
perature, allowing the engine to crank faster and
start easier.
•
Allow engine to run at idle for a few seconds be-
fore stopping engine to avoid run-on or backfiring.
Cooling System
•
Keep engine air intake screen and cylinder head
fins free of grass clippings, chaff, and dirt. Inspect
intake screen and cooling fins for cleanliness and
damage.
•
Check performance of the cooling system by
starting the engine, holding a hand adjacent to the
cylinder head, and feeling the cooling airflow.
•
Operate the engine at full speed when mowing.
This will allow the engine to produce full horsepower
and move more cooling air through the engine cool-
ing fins.
Air Cleaner
•
Use only Donaldson air cleaner elements. After-
market elements may not seal in the air cleaner
housing, allowing dirt to enter the engine. Also, af-
termarket filters often skimp on the filtration media
and require more frequent cleaning and replace-
ment (see instructions below).
•
Use the air flow restriction gauge to indicate the
need to service the air filter.
•
DO NOT overservice or frequently “disturb” the
air filter. A dirty air filter actually cleans better than
a new one. Changing and cleaning the filter too of-
ten can actually reduce filter efficiency and increase
the opportunity for traces of dust to enter the engine.
Wait until the element really needs servicing as indi-
cated by the loss of engine power.
•
When the air filter element is removed or re-
placed, make sure all dust is cleaned out of the air
cleaner housing and hose. Use a damp cloth and
wipe the interior of the canister and hose clean (a
little dirt left here will be sucked into the engine and
reduce engine life). When the filter is reinstalled,
make sure the element is held tight and straight
in the canister for proper seating and sealing.
•
Periodically check the air intake hose for cuts,
nicks, etc., and the hose clamps for tightness.
Oil
•
DO NOT screw filler cap into crankcase when
checking oil level.
•
Single viscosity or multi-viscosity oils may be
used with the viscosity matching ambient tempera-
tures for the engine operating conditions. This will
aid starting in cold weather and assure proper lu-
brication in hot weather.
•
Use only Kawasaki oil filters. Aftermarket filters
may not seal properly and/or have the incorrect
pressure relief valve for proper lubrication.
DANGER
Make sure to keep hands clear of exhaust
pipe, muffler, and moving parts when
checking airflow.
Summary of Contents for MS (13 HP)
Page 70: ...66 Operator s Notes...