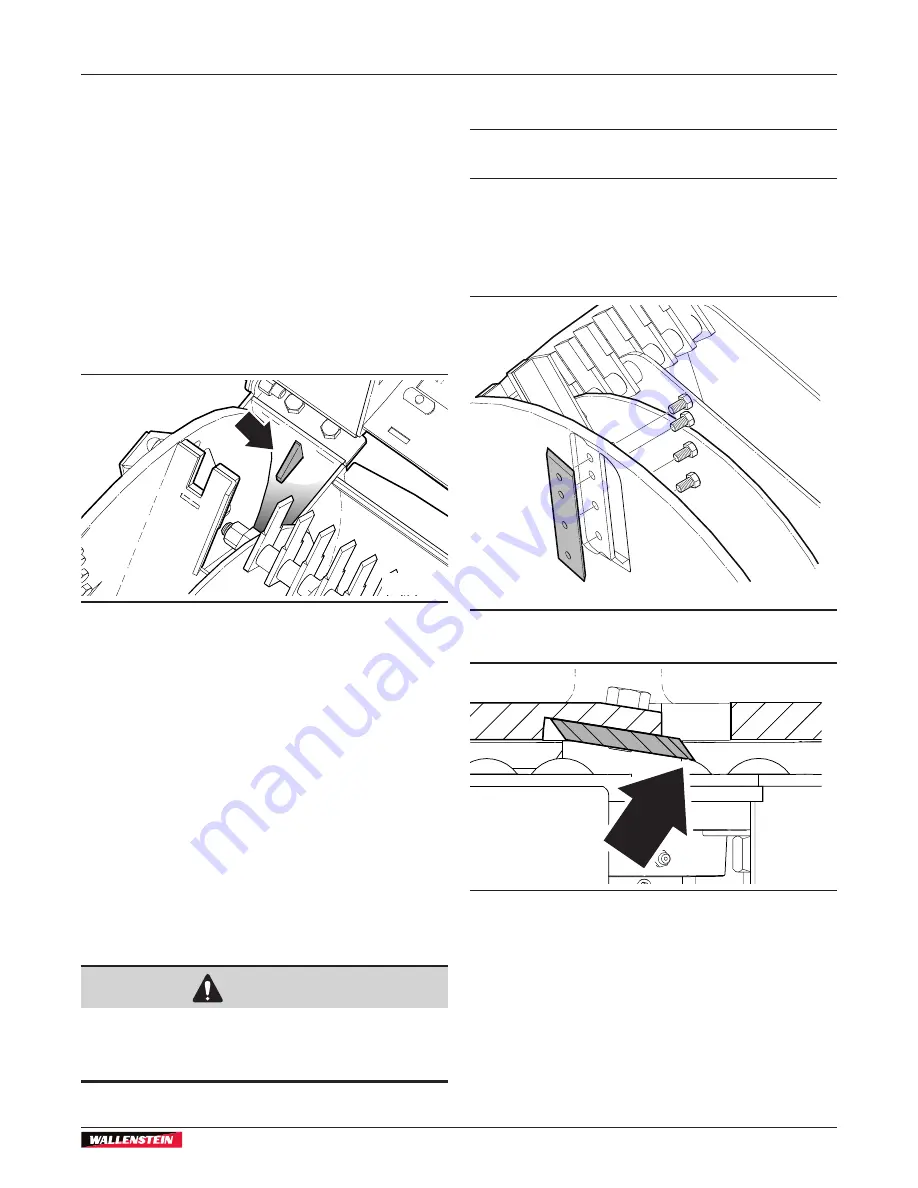
BXM32, BXM42
3-point Hitch Chipper-Shredder
Service and Maintenance
41
Replace broken shear pins with one the same size. Always
determine the cause of the problem and correct it before
resuming work. Shear pins are available from your distributor or
dealer.
9.5
Twig Breaker (BXM42 only)
Inspect the twig breaker for damage, bent or missing teeth
every 50 hours.
The twig breaker is located inside the lower rotor housing.
Material in the chipper is broken up into smaller pieces as the
discharge paddles rotate past it.
A damaged or worn twig breaker should be replaced.
00914
Fig. 41 –
Twig Breaker
9.6 Rotor Blades
Check rotor blade sharpness daily.
If the chipper is not pulling the material or material has to
pushed into the chipper, the rotor blades are probably dull.
Reverse or sharpen the blades if the cutting edge becomes dull.
Check blade sharpness more often if processing material with a
lot of sand, soil or dirt in it.
Keeping the blades sharp reduces the amount of power required
during operation. If one blade needs to be sharpened or
changed, the opposite one should be done as well.
Sharpening Rotor Blades
1.
Open the upper rotor housing.
CAUTION!
Risk of getting hands pinched or wedged
between lower rotor housing and rotor. Turn
rotor slowly and be aware of hand positioning.
W032
2.
Turn the rotor by hand so that one blade is fully exposed.
3.
Remove the blade from the rotor to sharpen. Sharpen at a
45° angle to provide the best cutting effect.
IMPORTANT! Sharpen both blades equally to maintain
proper rotor balance.
4.
Install rotor blades with leading edge out, towards the
ledger blade. Tighten the blade mounting bolts to
33 lbf•ft
(45 N•m)
.
5.
Repeat the steps for the other blade.
00915
Fig. 42 –
Changing rotor blade
00872
Fig. 43 –
Rotor blade leading edge