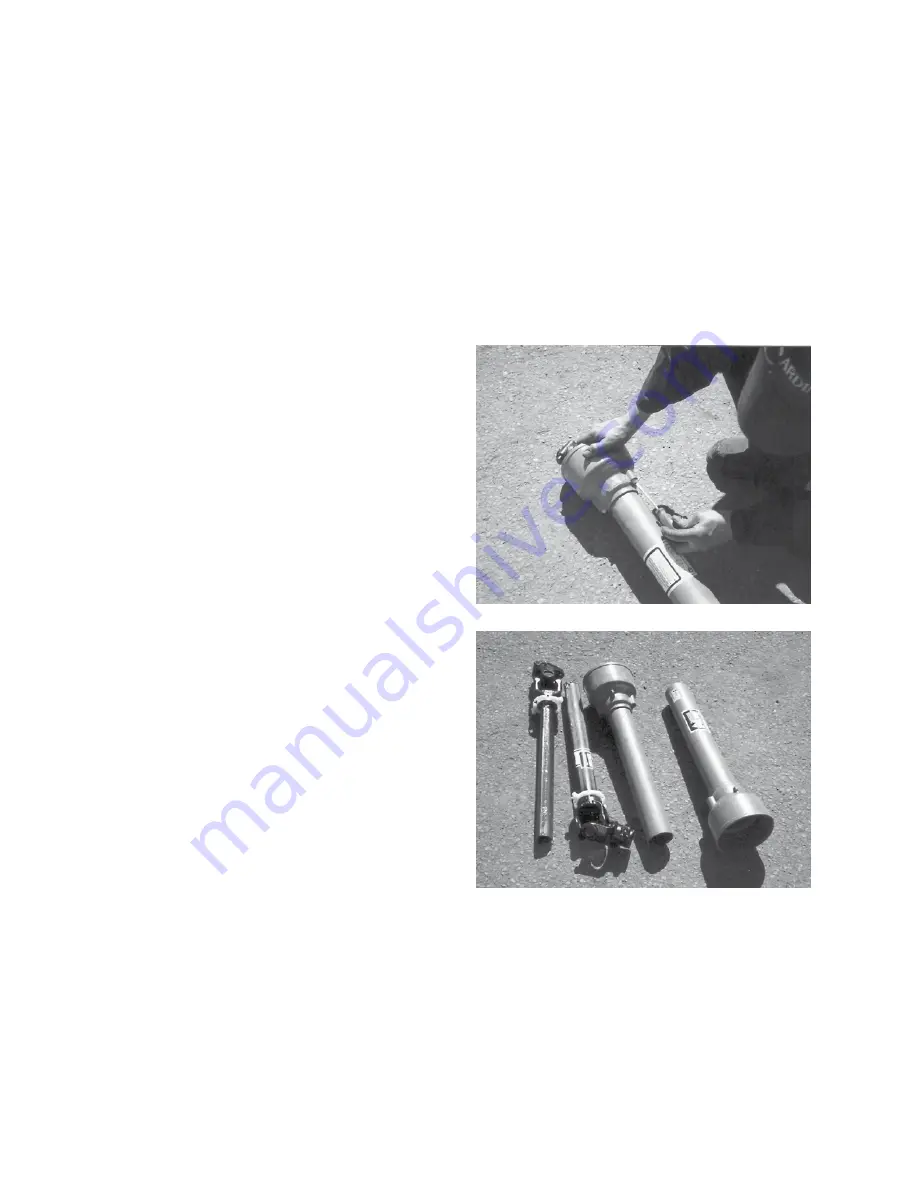
36
7.2.2 DRIVELINE MAINTENANCE
The PTO driveline is designed to telescope to allow for dimensional changes as the machine goes
through its operational range. A tubular guard encloses the driving components and is designed to turn
relative to the driving components. The driveline should telescope easily and the guard turn freely on the
shaft at all times. Annual disassembly, cleaning and lubrication is recommended to insure that all compo-
nents function as intended. To maintain the driveline, follow this procedure:
Fig. 20 DRIVELINE COMPONENTS
1. Disengage the PTO, stop the engine, remove
the ignition key and place it in your pocket and
wait for all moving parts to stop
2. Remove the driveline from the machine.
3. Pull driveline apart.
4. Use a screwdriver to turn lock studs on each
end. There are 2 studs per guard.
5. Pull the shaft out of the plastic tubular guard.
6. Use a solvent to clean the male and female
portions of the telescoping ends.
7. Apply a light coat of grease to each end.
8. Use a solvent to wash the grooves on each
end where the studs are located. Clean each
end also.
9. Apply a light coat of grease to each groove.
10. Insert the shaft into its respective guard and
align the studs with the holes.
11. Insert the studs through the holes and seat in
the groove.
12. Turn each stud to secure guard to shaft.
13. Check that each guard turns freely on the
shaft.
14. Assemble the driveline.
15. Check that the driveline telescopes easily.
16. Replace any components that are damaged
or worn.
17. Install the driveline on the machine.
Guard Removal
Disassembled
Summary of Contents for BXM32
Page 48: ...PRINTED IN CANADA ...