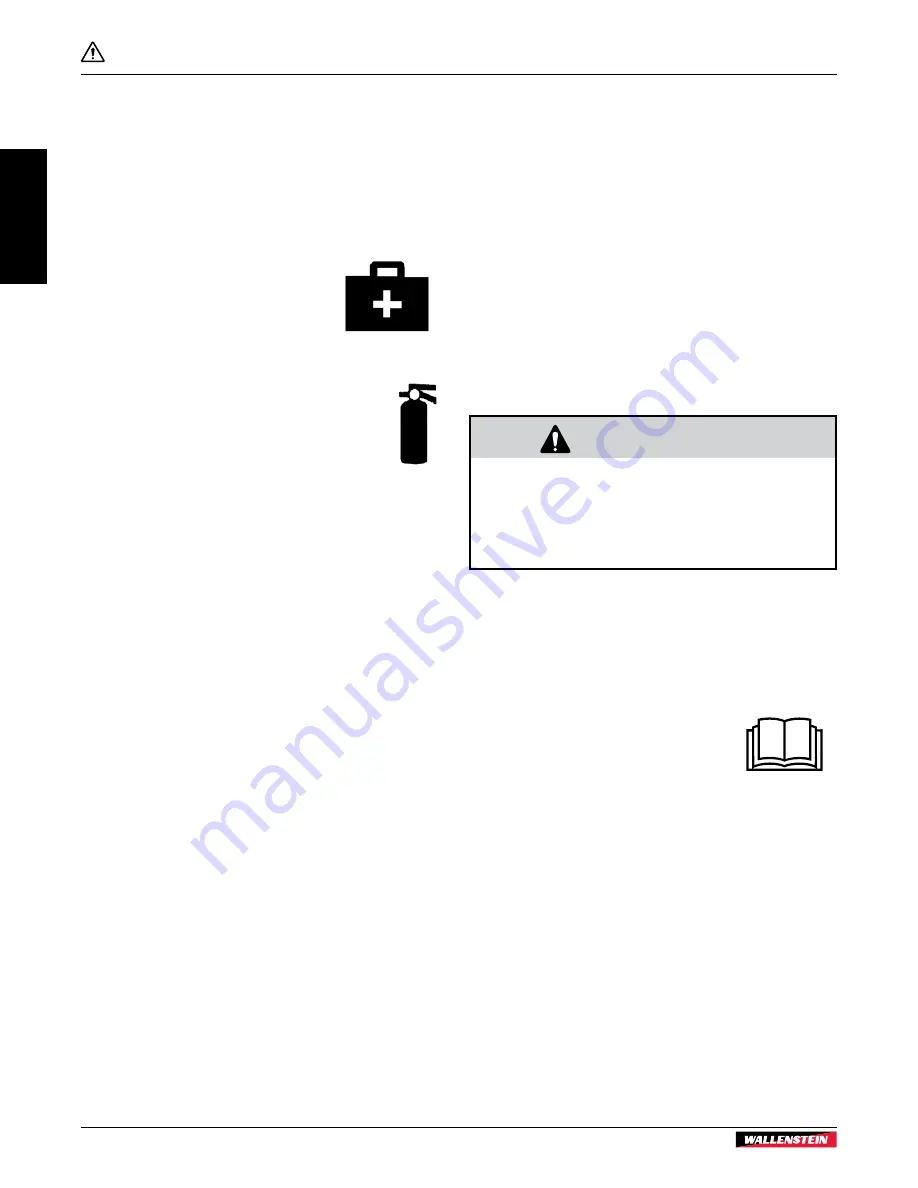
•
Wear appropriate Personal Protective Equipment (PPE)
when using this machine. This includes but is not limited
to:
- A hard hat
- Heavy gloves
- Hearing Protection
- Protective shoes with slip resistant soles
- Protective glasses, goggles or face shield
•
Keep a first-aid kit available for use
should the need arise and know how to
use it.
•
Inspect and secure all guards before starting.
•
Keep a fire extinguisher available for use should
the need arise and know how to use it.
• DO
think SAFETY! Work SAFELY!
• DO NOT
expect a person who has not read and understood
all use and safety instructions to operate the machine. An
untrained operator is not qualified and exposes himself
and bystanders to possible serious injury or death. It is the
owner's responsibility to the operator to ensure familiarity
and understanding of the machine.
• DO NOT
allow riders during transport.
• DO NOT
risk injury or death by ignoring good safety
practices.
2.5 Equipment Safety Guidelines
Operating machines safely is one of the main concerns in
designing and developing Wallenstein equipment. However,
accidents could occur that can be avoided by a few seconds of
thought and a more careful approach to handling equipment.
•
Keep all shields in place. If shield removal becomes
necessary for repairs, replace the shield prior to use. In
some cases, certain illustrations in this manual may show
an assembly with a safety shield removed for clarity.
However, equipment should never be used in this condition.
•
Replace any safety sign or instruction sign that is not
readable or is missing. Location and explanation of safety
signs start on
.
•
Never consume alcoholic beverages or drugs while using
this equipment. These can hinder alertness or coordination.
Consult your doctor about using this machine while taking
prescription medications.
•
Do not modify the equipment in any way. Unauthorized
modification may result in serious injury or death and may
impair the function and life of the equipment. Unapproved
modifications void warranty.
•
Never exceed the limits of a piece of machinery. If its ability
to do a job, or to do so safely is in question –
DO NOT TRY
IT
.
2.6 Safe Condition
Throughout this manual, we talk about a '
Safe Condition
'. What
this means is setting the machine in a state that makes it safe to
service or repair.
Place the machine in a Safe Condition before performing
any service, maintenance work or storage preparation by
performing the following:
SAFE CONDITION
•
Shut off engine. Remove ignition key.
•
Make sure all moving parts have stopped.
•
Disconnect battery ground (-) cable.
•
Block or chock wheels.
2.7 Safety Training
Safety is a primary concern in the design and manufacture of
Wallenstein products. Unfortunately, efforts to provide safe
equipment can be wiped out by a single careless act.
•
It is the operator's responsibility to read,
understand and follow ALL safety and
operation instructions in this manual.
•
Train all new personnel and review instructions frequently
with existing workers. Be certain only a properly trained
and physically able person will use the machinery. A person
who has not read and understood all instructions is not
qualified to use the machine. An untrained operator can
cause possible serious injury or death.
•
Know the tractor controls and how to stop the machine
quickly in an emergency.
•
If this machine is used by any other person, loaned or
rented, it is the owner's responsibility to make certain that
prior to using, every operator:
- reads and understands the owner's manual
- is instructed in safe and proper use of the equipment
- understands and knows how to perform the Safe
Condition procedure
BXMT4224 / BXMT4238
Trailer Chipper-Shredder
Safety
8
Safety
Summary of Contents for BXMT4224
Page 51: ......
Page 52: ...www wallensteinequipment com...